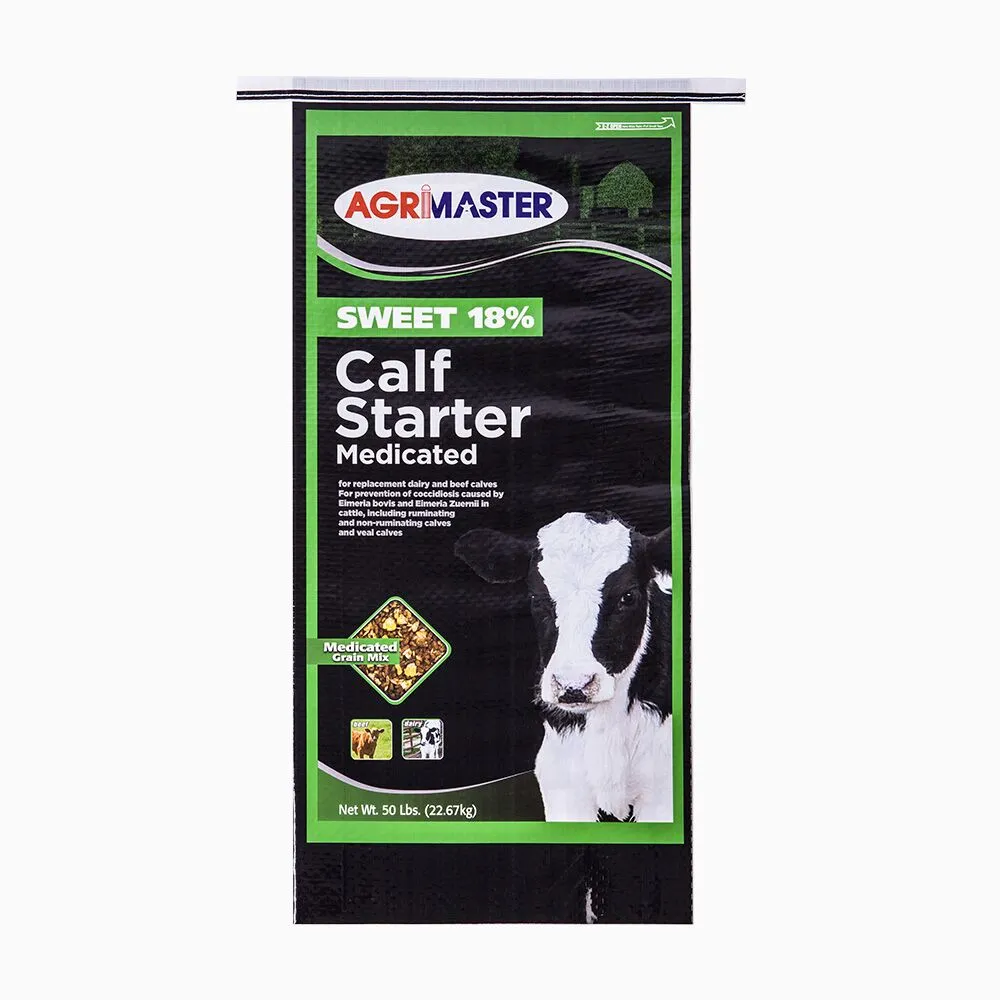
In today’s fast-paced packaging industry, efficiency, durability, and quality assurance are essential. Form-fill-seal (FFS) woven bags, also known as FFS woven sacks or FFS PP bags, are becoming indispensable in automated packaging processes due to their resilience, convenience, and versatility. VidePak leverages advanced equipment and robust quality standards, particularly in the production of tubular woven bags, to ensure that our products meet the highest industry demands. This article will explore how FFS woven bags contribute to automated packaging and delve into the rigorous quality control measures VidePak employs to maintain superior standards.
The Role of Form-Fill-Seal Woven Bags in Automated Packaging
Form-fill-seal woven bags streamline the packaging process by integrating filling and sealing into one continuous system. This approach not only enhances operational efficiency but also optimizes resource utilization and minimizes waste. The benefits of automated packaging with FFS woven bags are numerous, with applications across diverse industries, including agriculture, construction, and consumer goods.
FFS woven bags have unique features that facilitate automated packaging:
- Tubular Design: The cylindrical structure of tubular woven bags ensures uniform filling, reducing the likelihood of material spillage.
- High Tensile Strength: Made from polypropylene (PP), these bags offer excellent tensile strength, allowing them to handle heavy loads without tearing or stretching.
- Versatile Sealing Options: VidePak’s FFS bags are compatible with heat sealing, ultrasonic sealing, and mechanical sealing, providing flexibility to suit different materials and packaging needs.
By utilizing these features, VidePak’s FFS woven bags are tailored to optimize packing speeds, reduce labor costs, and improve accuracy in filling operations, particularly in high-volume packaging environments.
VidePak’s Quality Control Measures: Ensuring Reliable Performance in Every Bag
At VidePak, we are committed to ensuring the durability and reliability of our FFS woven bags through rigorous quality testing. Our quality control process includes tests on stretchability, tear resistance, heat seal performance, aging resistance, and UV stability. These tests are critical for confirming that each bag can withstand the demands of automated packing lines and storage conditions.
The following sections detail the essential quality control tests we perform, along with examples of typical parameters for each test.
Quality Test | Purpose | Test Parameters |
---|---|---|
Tensile Strength | Measures resistance to pulling and stretching | 1,000 N/mm for tubular woven bags |
Tear Resistance | Assesses the durability against tearing forces | 250 N in warp and weft directions |
Heat Seal Strength | Ensures secure sealing under high-temperature fills | Sealing pressure: 2 MPa at 160°C |
UV Resistance | Evaluates long-term exposure to UV rays | 3,000 hours under UV light |
Thickness Tolerance | Verifies uniform material thickness | ±10% tolerance on standard thickness |
Weight Consistency | Confirms material density and filling volume | 100–200 g/sq.m for PP woven bags |
Color Consistency | Monitors for uniform color and printing | ≤ 2 Delta E color variation |
Edge Quality (Cutting) | Ensures smooth, unfrayed edges | ≤ 2 mm fraying along cut lines |
1. Tensile Strength Testing
Tensile strength is a crucial factor for FFS PP bags, especially given their use in automated lines where filling speed and bag stability are essential. We use a tensile testing machine to apply gradually increasing force until the material ruptures, ensuring our bags can handle heavy weights.
2. Tear Resistance Testing
Tear resistance is another critical parameter for bag durability, as it determines the woven bag’s ability to resist tearing under pressure. VidePak measures tear resistance along both the warp and weft directions of the fabric to assess and control durability.
3. Heat Seal Strength Testing
For FFS woven bags to be effective, heat seal strength is essential. The heat seal test involves applying temperature and pressure to ensure a solid bond. Our standard testing for seal strength ensures that the bags can handle the high-temperature sealing process without any compromise on integrity.
4. UV Resistance Testing
As FFS woven bags are often exposed to varying environmental conditions, UV stability is a significant consideration for VidePak. We conduct accelerated UV exposure tests by subjecting samples to 3,000 hours under controlled UV light, replicating extended exposure to sunlight. This ensures our bags are capable of maintaining structural integrity in outdoor storage conditions.
5. Thickness and Weight Consistency
VidePak’s quality assurance extends to dimensional consistency. We monitor thickness tolerance and weight consistency in each production batch. The thickness tolerance test allows us to maintain a specified uniform thickness, typically within ±10% of the standard thickness, which ensures strength and reliability.
6. Edge Quality and Color Consistency
For clients seeking customized and branded packaging, maintaining edge quality and color uniformity is crucial. VidePak ensures that each batch of FFS woven bags adheres to strict guidelines on color and edge quality. Edge quality testing focuses on ensuring that there are minimal frays and consistent cuts, while color consistency tests confirm uniformity across large production runs.
Ensuring Comprehensive Testing and Quality in Every Batch of FFS Woven Bags
VidePak’s comprehensive quality control measures are designed to deliver products that consistently meet and exceed industry standards. Each bag undergoes multiple stages of testing, from raw material selection to final inspection. The following list highlights some of the additional checks VidePak performs on each production batch:
- Color Difference Testing: VidePak performs color testing for consistency in brand-specific colors.
- Tolerance in Thickness: By measuring tolerance, we maintain consistency and stability in bag performance.
- Weight Verification: We ensure each bag meets the specified weight for optimal handling.
- Edge Quality: Smooth and fray-free edges contribute to a higher-quality product appearance and increased longevity.
- Tensile and Elongation Testing: These tests are conducted on both raw material and finished bags to ensure flexibility and strength.
How VidePak’s Testing Standards Benefit Our Clients
VidePak’s commitment to quality benefits our clients in several ways. The consistent high quality of our FFS woven bags minimizes disruptions in packaging lines, reduces downtime, and contributes to lower operational costs. With rigorous quality standards, our bags are designed to last, providing excellent cost-effectiveness and reliability for clients worldwide. Our bags not only support automated filling and sealing but also comply with stringent safety and environmental standards, making them suitable for a variety of applications.
For more insights into the benefits of using Form-fill-seal woven bags, you can explore our link on industrial woven packaging standards. Our commitment to quality also extends to our FFS woven sacks, ensuring they perform reliably under diverse conditions. For more details on these sacks, check out our article on FFS woven sacks.