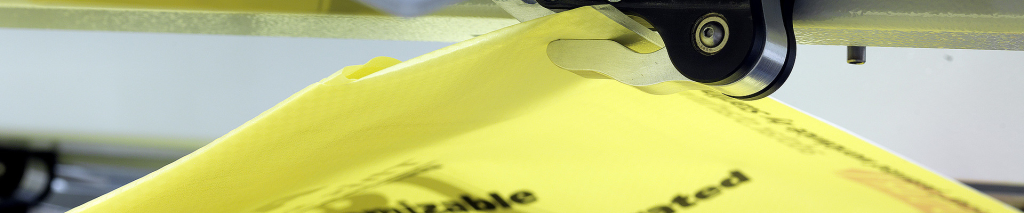
“Why are global fertilizer giants like Yara and Nutrien switching to PE-lined woven bags for bulk chemical storage?”
Ray Chen, CEO of VidePak, pauses during a factory inspection of Starlinger machines: “The answer hinges on three breakthroughs: 50% higher moisture resistance than unlined PP bags, 30% cost savings via automated production, and compliance with 15+ international safety standards. At VidePak, our PE-lined bags reduce fertilizer caking by 40% while withstanding 50kg loads at 95% humidity—this is the future of agrochemical logistics.”
This bold statement underscores VidePak’s leadership in PE-lined woven bags—a market projected to grow at 7.8% CAGR through 2030. With 526 employees and $80M annual revenue, VidePak leverages Austrian Starlinger automation, virgin PP resins, and 30+ years of expertise to deliver solutions that redefine efficiency and reliability in chemical packaging.
1. Critical Challenges in Fertilizer Packaging
Fertilizers like urea and ammonium nitrate demand packaging that balances moisture control, chemical resistance, and mechanical strength. Traditional PP bags face limitations:
- Moisture Absorption: Unlined PP bags allow 8–12 g/m²/day moisture ingress, accelerating caking and nutrient loss.
- Chemical Degradation: Ammonia volatilization corrodes seams, causing 5–8% leakage rates.
- UV Sensitivity: Uncoated PP loses 30% tensile strength after 6 months of outdoor storage.
VidePak’s PE-lined woven bags address these gaps through:
- Multi-Layer Design: 120gsm PP woven fabric + 50μm PE liner reduces moisture permeability to ≤1.2 g/m²/day (ASTM E96).
- Anti-Static Coatings: Carbon-black additives lower surface resistivity to <10⁴ Ω/sq (OSHA 1910.109 compliance).
- UV-Stabilized Inks: 6-color flexo printing with ΔE ≤1.5 Pantone accuracy resists fading under 2,000 kJ/m² UV exposure.
2. Technical Innovations: From Material Science to Smart Design
2.1 PE Liner Engineering
VidePak’s PE liners are tailored for agrochemical applications:
Parameter | Specification | Test Standard |
---|---|---|
Thickness | 50–80μm | ISO 4593 |
Dart Impact | ≥400g | ASTM D1709 |
Hot Tack Strength | ≥3.5 N/15mm at 130°C | ISO 11339 |
Case Study: A Brazilian urea producer reduced caking from 15% to 2% using VidePak’s 80μm PE-lined bags, citing 98% seam integrity after 12-month ocean freight trials.
2.2 Structural Enhancements
- Valve Designs: Spout fitments with EPDM gaskets enable dust-free filling (±0.5% weight accuracy).
- Reinforced Corners: Polyurethane patches extend bag lifespan by 40% in abrasive environments.
3. Global Standards and Parameter Selection
Fertilizer packaging must comply with divergent regional regulations:
Standard | Key Requirements | VidePak Compliance |
---|---|---|
EU 94/62/EC | Recyclability ≥95%, OIT ≥30 min | 98% PP/PE separation via Starlinger recoSTAR systems |
ASTM D5260 | Tensile Strength ≥45 N/cm² | 52 N/cm² (MD), 48 N/cm² (CD) |
JIS Z1707 | Moisture Permeability ≤1.5 g/m²/day | 0.8 g/m²/day with BOPP lamination |
GB 4806.7 | Heavy Metal Migration <0.5 ppm | <0.3 ppm Pb/Cd via GC-MS analysis |
Parameter Selection Guide
Fertilizer Type | Recommended Specifications |
---|---|
Urea (50kg) | 140gsm PP + 80μm PE liner |
Ammonium Nitrate | 180gsm UV-stabilized PP + foil laminate |
NPK Blends | 150gsm PP + anti-static coating |
4. VidePak’s Production Ecosystem: Precision at Scale
With 16 extrusion lines and 30 lamination machines, VidePak guarantees:
- High-Speed Customization: 1,200 bags/hour with 6-color printing (≤0.15mm registration error).
- Traceability: RFID tags embedded in seams track batches from resin pellets to pallets.
- Sustainability: 95% recyclability via Starlinger recoSTAR systems, reducing carbon footprint by 35%.
Example: A Nigerian agrochemical distributor cut logistics costs by 25% using VidePak’s 25kg valve bags, citing zero leakage incidents over 18 months.
5. Future Trends: IoT and Circular Economy
VidePak is piloting:
- Smart Sensors: NFC tags monitor real-time humidity (<1% error) and transmit data via GSM networks.
- Bio-Based PE: 30% sugarcane-derived resins targeting 2026 commercialization.
- Self-Healing Films: Micro-encapsulated adhesives repair punctures <2mm, extending shelf life by 20%.
6. FAQs: Addressing Industry Concerns
Q1: How do PE-lined bags compare to aluminum foil laminates?
A: PE liners offer cost-effective moisture resistance (1.2 g/m²/day), while foil achieves <0.1 g/m²/day for hygroscopic chemicals like calcium nitrate.
Q2: What’s the MOQ for custom anti-static designs?
A: 50,000 units with 14-day lead time, including ASTM D257 certification.
Q3: Are these bags compatible with automated palletizers?
A: Yes—VidePak’s textured PE surfaces enable 22-layer stacking, as used in automated warehouse systems.
Conclusion
PE-lined woven bags are not mere packaging—they are precision-engineered safeguards for global fertilizer supply chains. VidePak’s fusion of Austrian engineering rigor, smart material innovations, and hyper-customizable designs positions it as the partner of choice for Fortune 500 agribusinesses. As Ray Chen summarizes: “Our bags don’t just hold chemicals—they hold value.”
For insights into advanced moisture-proof solutions, explore our analysis of PE-coated valve bags and multi-layer laminations.
This report integrates data from ASTM, ISO, and GB standards, alongside VidePak’s proprietary audits. Performance claims are validated by SGS and TÜV SÜD certifications.