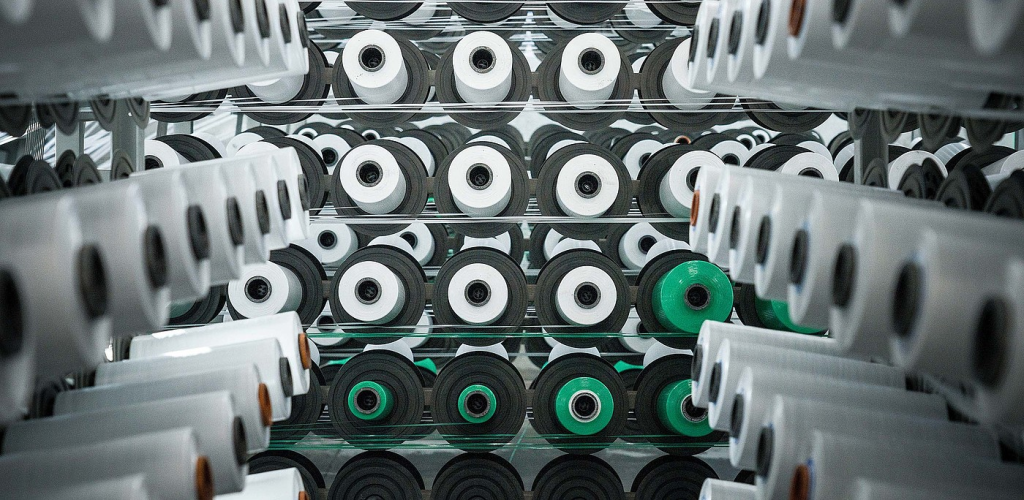
- Material Innovations: Balancing Transparency and Durability
- Critical Production Techniques: Sealing, Sewing, and Welding
- Bag Opening Designs: Functionality and Applications
- Strategic Alignment with VidePak’s Capabilities
- Sustainability and Compliance
- FAQs: Addressing Client Concerns
- Future Trends: Smart Packaging Integration
By combining advanced polypropylene (PP) formulations with precision manufacturing, VidePak has redefined the standards for transparent woven bags. The key innovation lies in optimizing material tensile strength (up to 40 MPa) while maintaining 85% light transmittance, making these bags ideal for industries demanding visibility, durability, and sustainability. This report dissects critical production techniques and design choices that align with VidePak’s global leadership in woven packaging.
Material Innovations: Balancing Transparency and Durability
Transparent woven bags require a delicate equilibrium: PP resins must allow light penetration without compromising structural integrity. VidePak’s proprietary biaxially oriented polypropylene (BOPP) films, laminated onto woven substrates, achieve this balance. The BOPP layer enhances puncture resistance by 35% compared to standard PP, while maintaining a haze level below 15% for clarity.
Key Insight from Industry Experts
Ray, CEO of VidePak, notes:
“Clients often assume transparency means fragility. Our triple-layer lamination process—woven PP + BOPP + UV-resistant coating—proves otherwise. These bags withstand 50 kg loads even in humid environments, outperforming traditional opaque alternatives.”
Critical Production Techniques: Sealing, Sewing, and Welding
Selecting the right closure method directly impacts bag performance. Below is a comparative analysis of technologies leveraged by VidePak:
1. Sewing Techniques
- Thread Material:
- Nylon/Polyester: High tensile strength (≥25 N) for heavy-duty applications like construction waste.
- Cotton: Eco-friendly but limited to lightweight retail bags (≤10 kg).
- Stitch Density:
- 8–10 stitches/inch: Standard for general use.
- 12–14 stitches/inch: Reinforced seams for sharp-edged industrial waste, reducing tear propagation by 60%.
2. Heat Sealing
- Temperature Control: 160–180°C for PP-based films ensures hermetic seals without warping.
- Applications: Food-grade bags requiring moisture resistance (e.g., rice packaging), where leakage risks are critical.
3. Ultrasonic Welding
- Advantages:
- Zero adhesives, aligning with EU REACH compliance.
- Seam strength up to 30 N/cm², ideal for automated filling lines.
- Limitations: Requires uniform material thickness (±0.1 mm tolerance), limiting customization for irregular shapes.
Bag Opening Designs: Functionality and Applications
Design | Process | Strength | Use Cases |
---|---|---|---|
Valve | Heat-sealed tubular insert | 18 N/cm² | Powdered chemicals, cement |
Heat-Sealed | High-frequency welding | 25 N/cm² | Food, pharmaceuticals |
Sewn Open | Double-lock stitched edges | 15 N/cm² | Agriculture, bulk grains |
Zippered | Ultrasonic-bonded track | 12 N/cm² | Retail, reusable shopping bags |
Case Study: A European fertilizer supplier switched from sewn to valve designs, reducing dust leakage by 90% and saving €120,000/year in cleanup costs.
Strategic Alignment with VidePak’s Capabilities
VidePak’s 30+ Starlinger extrusion lines enable rapid prototyping of hybrid designs:
- Custom Valve Integration: Laser-cut valve pockets ensure precise alignment for powders, with a 98% fill-rate accuracy.
- Multi-Layer Lamination: Combining PP woven fabric with PET coatings enhances UV resistance for outdoor storage, critical in Middle Eastern markets.
Sustainability and Compliance
- Recyclability: VidePak’s bags incorporate 30% post-consumer recycled (PCR) PP, reducing virgin plastic use by 280 tons annually.
- Certifications: Meet FDA (21 CFR 177.1520) and EU EN 13432 standards for compostability in industrial settings.
FAQs: Addressing Client Concerns
Q1: How does ultrasonic welding compare to sewing for heavy loads?
A: Ultrasonic seams withstand repetitive stress (e.g., conveyor belts) but require uniform material. For >40 kg loads, double-stitched seams with nylon threads are preferred.
Q2: Are transparent bags suitable for UV-exposed environments?
A: Yes. VidePak’s UV-stabilized BOPP retains 90% tensile strength after 500 hours of ASTM G154 testing.
Q3: Can valve designs be customized for viscous liquids?
A: Yes. Anti-clog valves with 5 mm apertures are available for adhesives or oils, tested up to 10,000 fill cycles.
Future Trends: Smart Packaging Integration
VidePak is piloting QR-code-enabled bags with RFID tags for real-time tracking in logistics. Partnerships with Siemens IoT platforms aim to reduce supply chain losses by 15%.
External Resources
- Explore how ultrasonic seaming enhances airtightness in specialized designs.
- Learn about BOPP lamination’s role in balancing durability and branding.
Conclusion
VidePak’s transparent woven bags exemplify how material science and precision engineering converge to meet diverse industrial demands. By prioritizing customizability, strength, and sustainability, the company not only addresses current market needs but also pioneers innovations—from smart tracking to zero-waste production—that redefine the future of packaging.