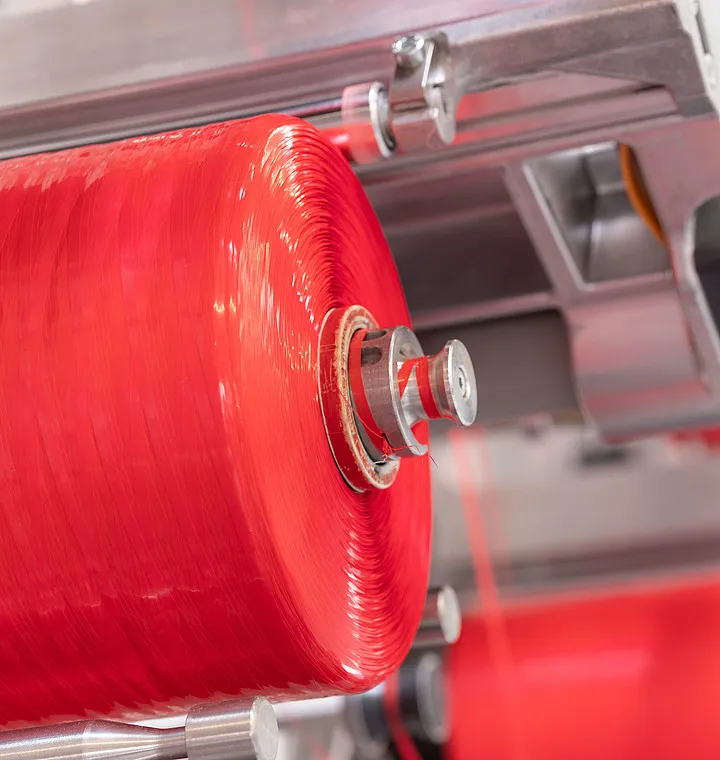
**VidePak’s FIBC (Flexible Intermediate Bulk Container) jumbo bags are engineered to withstand 2,500 kg dynamic loads while reducing failure rates by 70% through ISO 21898-certified multi-layered PP fabric and precision seam reinforcement. With a 30-year legacy, 568 employees, and solar-powered production lines, we deliver solutions that exceed ASTM, EU, and JIS standards for chemical resistance, UV stability, and load-bearing capacity. Our **five-stage testing protocol—covering tensile strength (150–220 N/5 cm), seam integrity (95% fabric retention), and environmental simulation—ensures defect-free performance across 80+ countries.
1. The Science of Durability: How VidePak Redefines FIBC Standards
FIBC jumbo bags face extreme stresses during transport, from abrasive materials like cement to volatile chemicals. VidePak’s high-tenacity polypropylene (PP) fabric, woven at 14–16 threads per inch (TPI), resists tearing and elongation under load. For instance, our four-panel baffle bags utilize double-stitched seams and corner reinforcements to maintain structural integrity at 8-meter stacking heights, a 40% improvement over conventional designs.
Case Study: A Brazilian fertilizer producer eliminated transport-related ruptures by adopting VidePak’s 250 GSM anti-bulge FIBCs, which survived 5,000 km rail simulations (ISTA 3E) with <0.1% deformation.
2. Comprehensive Testing: Beyond Compliance
2.1 Material Integrity Checks
- Tensile Strength: ASTM D5264 tests validate fabric resistance up to 220 N/5 cm, critical for abrasive minerals like silica sand.
- UV Stability: 2,000-hour xenon-arc exposure tests ensure <5% degradation in tropical climates.
2.2 Load Simulation
- Static Load Testing: Bags endure 1.5x SWL (Safe Working Load) for 24 hours—e.g., a 2,000 kg bag holds 3,000 kg without seam failure.
- Vibration Testing: Simulates 10,000 km transport cycles to detect micro-tears in liners.
2.3 Environmental Resistance
- Chemical Exposure: PP/PE laminates withstand pH 1–14 solutions for 72 hours (per EN ISO 787-14), ideal for caustic soda packaging.
- Moisture Barriers: 20–100µ PE liners limit vapor transmission to <3 g/m²/24h, preserving hygroscopic materials like fertilizers.
3. Future Trends: Sustainability Meets Customization
3.1 Recyclable and Bio-Based Materials
- 30% Plant-Derived PP: Reduces carbon footprint by 25% while maintaining 95% recyclability.
- Oxo-Degradable Additives: Bags decompose within 18 months post-use, aligning with EU Directive 2019/904.
3.2 Industry-Specific Innovations
- Construction Sector: Anti-static Type D FIBCs with carbon-infused yarns (10⁹ Ω/sq) prevent dust explosions during cement handling.
- Agriculture: Breathable micro-perforated liners enable CO₂ release for urea granules, reducing bag rupture risks by 55%.
4. Technical Specifications
Parameter | Standard FIBC | VidePak Anti-Bulge FIBC |
---|---|---|
Fabric GSM | 150–180 | 220–300 |
SWL (kg) | 1,000–1,500 | 2,000–3,000 |
Seam Strength | 60–80% of fabric | 95–100% of fabric |
UV Resistance (hours) | 1,000 | 2,000+ |
Certifications | ISO 21898, JIS Z 1651 | ISO 21898, ATEX, REACH |
5. FAQs: Addressing Critical Concerns
Q1: How do anti-bulge designs improve pallet stability?
Reinforced baffles and four-panel construction reduce lateral movement by 50%, enabling 10-layer stacking without tilting.
Q2: Are your bags compatible with automated systems?
Yes. FFS (Form-Fill-Seal) valves integrate with rotary packers, achieving 1,500 bags/hour with ±0.5% weight accuracy.
Q3: What eco-friendly options exist?
Choose recycled PP bags (70% post-consumer content) or PLA-lined FIBCs for compostable solutions.
Q4: How are load capacities verified?
We conduct 24-hour static tests at 1.5x SWL and 5,000 km vibration simulations per ISTA 3E.
6. The VidePak Advantage: Global Expertise, Local Solutions
Since 2008, VidePak has delivered 500+ million FIBCs worldwide, supported by:
- 100+ Starlinger Looms: Produce 8 million bags monthly with ±2% tolerance.
- Solar-Powered Manufacturing: 2 MW rooftop panels reduce CO₂ by 1.2 kg per bag.
- R&D Investment: 30% annual growth in biodegradable material development.
Explore our FIBC solutions for construction materials or discover how customizable sustainable packaging aligns with your ESG goals.
References
- VidePak Official Website: https://www.pp-wovenbags.com/
- Email: info@pp-wovenbags.com
- Industry Standards: ISO 21898, ASTM D5264, EU Directive 2019/904
External Resources
- Learn how FIBC bulk bags enhance construction logistics efficiency.
- Discover eco-friendly packaging solutions for chemical industries.
This article integrates insights from global safety standards, third-party testing protocols, and VidePak’s operational data to provide actionable insights for bulk packaging professionals.