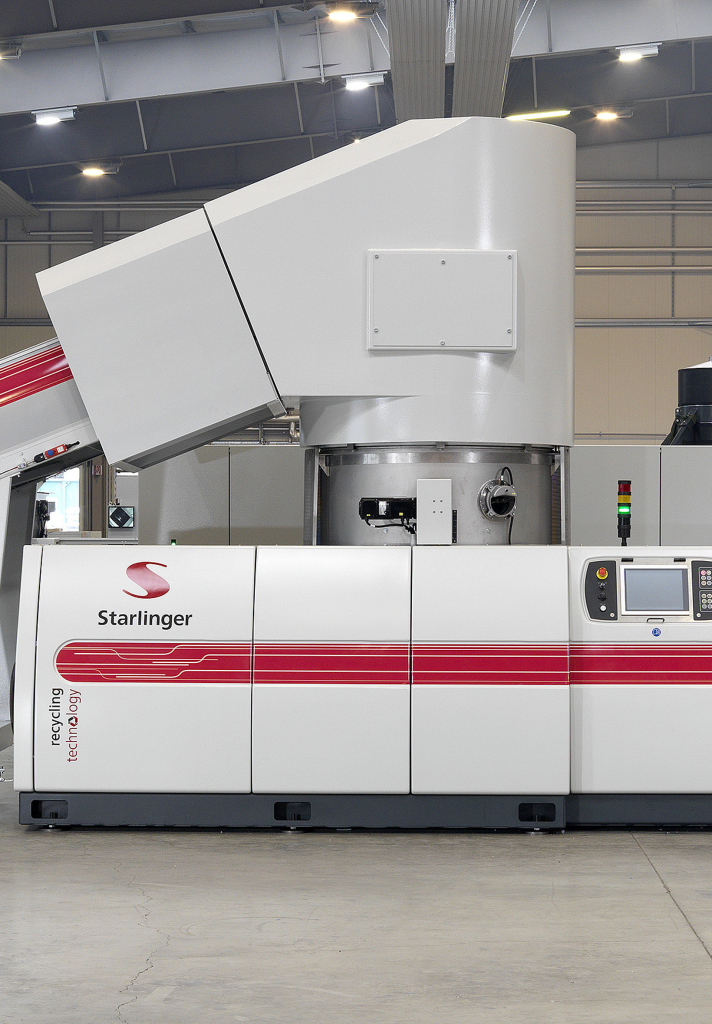
A Conversation with Ray, CEO of VidePak
Interviewer: “VidePak has grown into a global leader in woven bag manufacturing. What’s the secret behind your success?”
Ray: “Our commitment lies in two pillars: leveraging Starlinger’s cutting-edge machinery to achieve unmatched production precision and aligning our products with sustainability trends, particularly in waste management. These strategies ensure our kraft paper laminated woven bags meet both industrial demands and environmental responsibilities.”
1. Introduction
The packaging industry is undergoing a paradigm shift toward sustainable and high-performance solutions. Kraft paper laminated woven bags, combining the durability of polypropylene (PP) weaving with the eco-friendly appeal of kraft paper, have emerged as a versatile choice for industries ranging from agriculture to waste management. VidePak, a pioneer in this space, exemplifies how technological integration—specifically through Starlinger’s advanced equipment—can elevate product quality, operational efficiency, and environmental impact. This report explores VidePak’s innovative approach, supported by data, case studies, and industry trends.
2. VidePak: Company Overview
Founded in 2008 and led by Ray, VidePak operates with a workforce of 526 employees and a sprawling infrastructure:
- Production Capacity: 100+ circular looms, 16 extrusion lines, 30+ lamination/printing machines.
- Product Range: BOPP woven bags, valve bags, kraft paper laminated bags.
- Market Reach: $80 million annual revenue, global clientele across agriculture, construction, and recycling sectors.
The company’s use of virgin PP resin ensures consistency, while Starlinger’s machinery enables high-speed production (e.g., 500,000 bags/month capacity) and customization, including multi-color printing and lamination variations.
3. Starlinger’s Technology: Driving Precision and Speed
Starlinger’s equipment is central to VidePak’s operational excellence. Key features include:
3.1 High-Speed Circular Looms
- Output: Up to 200 meters of fabric per minute, reducing production time by 30% compared to conventional looms.
- Uniform Weaving: Ensures consistent tensile strength (e.g., 1,200 N/cm²), critical for heavy-duty applications like cement or construction waste packaging.
3.2 Lamination and Printing Systems
- Kraft Paper Integration: Starlinger’s adhesive lamination technology bonds kraft paper to PP fabric seamlessly, enhancing tear resistance and moisture barrier properties.
- Customization: Supports 8-color printing with ±0.5mm registration accuracy, vital for branding and regulatory labeling.
Case Study: VidePak’s collaboration with a European waste management firm resulted in a 25% reduction in bag breakage during recycling collection, attributed to Starlinger’s precision lamination.
4. Waste Management Applications: A Sustainable Edge
Kraft paper laminated bags are increasingly adopted in waste collection due to their recyclability and strength. VidePak’s solutions address critical needs:
4.1 Recyclable Material Collection
- Design: Bags with UV-resistant coatings and anti-static liners for safe storage of paper, plastics, and metals.
- Market Demand: The global waste management packaging market is projected to grow at 6.2% CAGR (2023–2030), driven by regulations like the EU’s Circular Economy Action Plan.
4.2 Case Study: Municipal Waste Programs
VidePak supplies kraft-PP composite bags to a municipal recycling initiative in Germany. Key outcomes:
- Durability: 98% of bags withstand multiple reuse cycles.
- Cost Efficiency: 15% lower logistics costs due to reduced replacement frequency.
5. Product Specifications and Customization
VidePak’s kraft paper laminated woven bags are tailored to diverse needs:
Parameter | Specification |
---|---|
Material | PP woven fabric + 80–120 GSM kraft paper |
Lamination | PE/PP adhesive, heat-sealed edges |
Load Capacity | 20–50 kg (static)/10–25 kg (dynamic) |
Printing Options | Up to 8 colors, CMYK/Pantone matching |
Certifications | ISO 9001, SGS, REACH compliance |
6. Addressing Common Questions (FAQs)
Q1: How does kraft paper enhance sustainability?
A: Kraft paper is biodegradable and recyclable, reducing landfill waste. Combined with PP’s reusability, these bags align with circular economy goals.
Q2: Can these bags handle sharp or abrasive waste?
A: Yes. Starlinger’s double-layer lamination prevents punctures, making them ideal for construction debris or glass recycling.
Q3: What’s the lead time for custom orders?
A: VidePak delivers within 15–20 days, leveraging automated workflows and in-house design teams.
7. Future Trends and Strategic Alignment
- Automation: VidePak is exploring Starlinger’s self-opening sack systems to further streamline packaging.
- Circular Economy: Partnerships with recyclers like Visy (processing 40% of Australia’s kerbside waste) highlight the role of durable packaging in closing material loops.
8. Conclusion
VidePak’s synergy with Starlinger’s technology positions it at the forefront of sustainable packaging innovation. By prioritizing efficiency, customization, and waste management applications, the company not only meets current market demands but also shapes future industry standards. As Ray notes, “Investing in advanced machinery isn’t just about productivity—it’s about building a legacy of quality and responsibility.”
For insights into material innovations, explore our analysis of eco-friendly woven bags and their market impact.
This report integrates data from industry reports, case studies, and VidePak’s operational metrics to provide actionable insights for stakeholders in packaging and waste management.