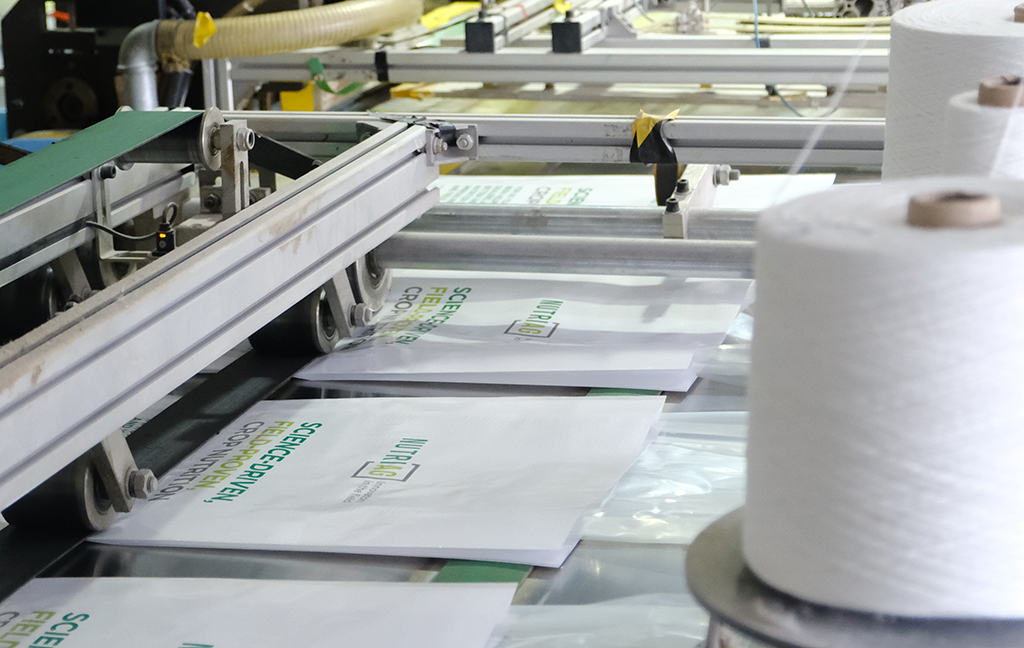
Sewn open mouth polypropylene (PP) bags are widely used in many industries, including agriculture, construction, and manufacturing, due to their strength, versatility, and cost-effectiveness. At VidePak, we are committed to producing high-quality PP bags that exceed industry standards. Our quality control process spans the entire production journey—from extrusion to weaving, coating, printing, and final bag production. Using advanced equipment from global leaders like Starlinger and W&H, we ensure that every bag is durable, reliable, and perfectly suited to its intended use.
1. The Production Process: Step-by-Step
1.1 Extrusion and Drawing: Building Strength
The first step in manufacturing PP bags is extrusion. Polypropylene pellets are melted and formed into films or yarns. This step is crucial because it affects the strength and flexibility of the material.
Why is this important?
The extrusion process sets the foundation for the bag’s performance. If the material isn’t properly extruded, it can lead to weak spots that compromise the bag’s ability to hold heavy loads. At VidePak, we use Starlinger technology in extrusion. This ensures that the PP material is evenly distributed and of the highest quality, giving the bags superior tensile strength. For example, when used for packaging cement or fertilizers, these bags can endure high pressures without tearing or losing shape.
1.2 Weaving: Strengthening the Fabric
After extrusion, the polypropylene yarn is woven into fabric. This step is crucial for determining the bag’s overall strength and durability. A tightly woven fabric increases the load-bearing capacity of the bags.
Why does this matter?
The weave density directly affects how much weight the bag can carry and how resistant it is to wear and tear. VidePak uses W&H weaving machines, which offer precision control over the weave, ensuring uniformity and high durability. This is especially important in industries like construction, where bags must withstand rough handling and heavy weights. A strong, consistent weave ensures the bag can safely hold and transport materials like gravel or sand without breaking.
1.3 Coating: Protection Against Elements
Once the fabric is woven, we apply a coating to enhance the bag’s durability. This coating can be polyethylene (PE) or other materials, which protect the bag from moisture, chemicals, and UV radiation.
Why is coating necessary?
For products that need protection from the elements—like seeds, fertilizers, or grains—a coating is essential. The coating makes the bag water-resistant, preventing the contents from getting wet or spoiled during transport. Additionally, UV protection ensures that the bags do not degrade when exposed to sunlight. By using advanced co-extrusion technology, we apply multiple layers of protective coatings, providing superior resistance against weathering.
1.4 Printing: Branding and Customization
At VidePak, we offer custom printing options to help businesses brand their bags. Using flexographic or gravure printing techniques, we ensure that logos, product information, and designs appear clearly and vibrantly on every bag.
Why is printing important?
Custom printing allows businesses to enhance their visibility and create a stronger connection with customers. For example, in the food industry, where packaging plays a significant role in consumer decision-making, clear branding can help attract attention and increase sales. Our printing technology ensures that the designs remain intact even under challenging conditions, such as moisture or abrasion, ensuring that your brand message lasts throughout the product’s lifecycle.
1.5 Bag Manufacturing: The Final Touch
Finally, the woven fabric is sewn into bags. The open mouth is stitched together, ready to be filled with the product. This stage is crucial for ensuring the bag’s final strength and usability.
Why is the sewing step vital?
Proper stitching ensures that the bag remains intact, even when it’s filled to capacity. Any weak stitching can cause the bag to rupture under load. Our automated stitching systems guarantee precision, with reinforced seams to prevent failure. The bags are then tested for quality before being shipped.
2. VidePak’s Commitment to Quality Control
At VidePak, quality control is at the heart of our manufacturing process. We apply strict measures at every step to ensure that our bags are durable, reliable, and meet the specific needs of our customers.
2.1 Raw Material Testing
We start with high-quality polypropylene pellets, sourced from trusted suppliers. These materials undergo rigorous testing to ensure they meet our strict standards for purity and composition.
Why is this testing necessary?
Impure or poorly processed raw materials can result in weak bags that tear or degrade too quickly. By conducting thorough testing on raw materials, we ensure that every bag made from these materials will be of the highest quality.
2.2 In-Process Monitoring
During the production process, we continuously monitor each stage—extrusion, weaving, coating, and printing. This ensures that any issues are caught early and corrected immediately.
Why is in-process monitoring important?
Without regular monitoring, small defects can go unnoticed, leading to larger problems down the line. Our real-time monitoring systems help identify and resolve potential issues before they impact the final product. This approach prevents delays and guarantees that every bag meets our high standards.
2.3 End-Product Testing
Once the bags are manufactured, they undergo several tests to ensure they meet durability, strength, and environmental resistance requirements. These tests simulate the conditions the bags will face in real-world use.
Why do we test the end product?
Testing the final product ensures that each bag can withstand the conditions it will face in its intended environment. Whether it’s holding heavy cement or withstanding outdoor conditions, we ensure that our bags perform as expected.
3. Product Specifications and FAQs
Here is a summary of our sewn open mouth PP bags’ key specifications:
Feature | Sewn Open Mouth PP Bags |
---|---|
Material | Polypropylene (PP) |
Coating | PE or other moisture-resistant coatings |
Printing | Flexographic or gravure printing |
Strength | High tensile strength, tear-resistant |
UV Resistance | Yes, with UV inhibitors |
Custom Sizes | Yes, tailored to specific customer needs |
Applications | Agriculture, construction, chemicals, etc. |
Recyclability | Yes, eco-friendly solution |
FAQs:
Q1: What sets VidePak’s sewn open mouth PP bags apart from others?
Our bags are manufactured using advanced technology from Starlinger and W&H, ensuring top-tier strength, durability, and quality. The use of premium materials and strict quality control processes guarantees that our bags outperform others in the market.
Q2: Can these bags be used for food packaging?
Yes, we offer food-grade options that meet safety standards for food contact. Our bags are made with high-quality, non-toxic materials that ensure the safety of the contents.
Q3: Are VidePak’s bags strong enough to hold heavy loads?
Definitely. Our bags are designed to handle heavy loads such as cement, grains, and fertilizers. The high-quality materials and advanced weaving techniques ensure that the bags can carry substantial weight without tearing or breaking.
Q4: How can I customize my bags?
We offer a variety of customization options, including size, color, and printing. You can add logos, product information, or custom designs to enhance your brand’s visibility and customer appeal.
4. Conclusion
At VidePak, we are dedicated to producing the highest-quality sewn open mouth PP bags. Using world-class technology from Starlinger and W&H, combined with our rigorous quality control measures, we ensure that every bag meets the highest standards. Whether you need bags for agriculture, construction, or other industries, we deliver durable, reliable, and cost-effective packaging solutions.
To learn more about how VidePak can meet your packaging needs, check out our approach to sustainable packaging solutions and the versatility of woven polypropylene bags in industrial packaging.