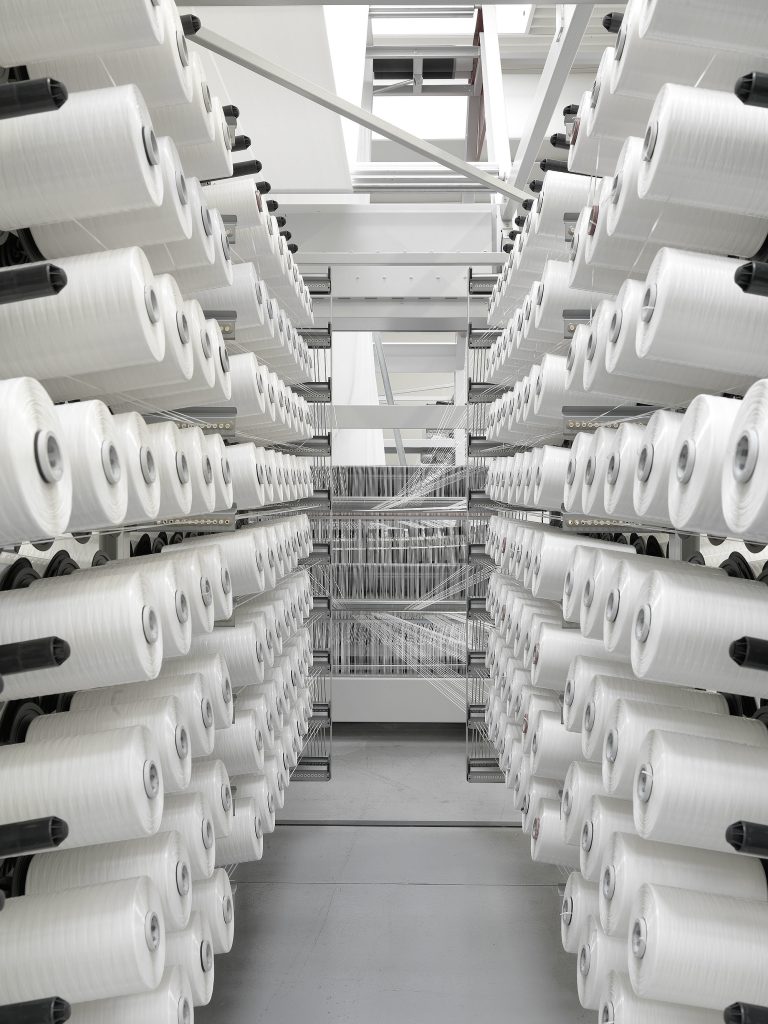
- 1. The Science of Polypropylene: Building Blocks of Durability
- 2. Health and Safety: From Raw Materials to Final Product
- 3. Manufacturing Excellence: Starlinger Technology and Customization
- 4. Sustainability: Balancing Performance and Eco-Consciousness
- FAQs: Addressing Critical Concerns
- 5. Market Differentiation: Data-Driven Success
- Conclusion: The Path Forward
“What defines a high-quality woven bag?”
Ray, CEO of VidePak, leans forward confidently: “It’s the marriage of advanced polypropylene science, rigorous safety protocols, and precision manufacturing. At VidePak, excellence isn’t an option—it’s engineered into every thread.”
This statement encapsulates VidePak’s philosophy. Founded in 2008 and now a global leader with $80M annual revenue, the company combines 30+ years of expertise with cutting-edge technology to produce custom woven bags that meet stringent health, safety, and performance benchmarks. This report delves into the scientific principles behind polypropylene (PP) quality, evaluates health and safety frameworks, and demonstrates how VidePak’s innovations align with global standards.
1. The Science of Polypropylene: Building Blocks of Durability
Polypropylene, a thermoplastic polymer, is the cornerstone of woven bag production. Its molecular structure—comprising long hydrocarbon chains with high crystallinity—grants exceptional tensile strength (30–40 MPa), chemical resistance, and UV stability. VidePak exclusively uses virgin PP resin, avoiding recycled materials that risk introducing contaminants or weakening fiber integrity.
Key Parameters for PP Quality:
- Melt Flow Index (MFI): Ranges between 2–4 g/10min for optimal extrusion and weaving. Higher MFI reduces fiber strength, while lower values hinder processing efficiency.
- Additives: UV stabilizers (e.g., hindered amine light stabilizers) and antioxidants (e.g., phenolic compounds) extend bag lifespan under harsh conditions.
Case Study: VidePak’s BOPP laminated woven bags utilize PP films with a thickness of 18–25 microns, achieving a puncture resistance of 8–12 N. This ensures reliable protection for agricultural products like fertilizers, even in humid climates.
2. Health and Safety: From Raw Materials to Final Product
Health risks in woven bags often stem from inadequate material purity or improper manufacturing. VidePak’s protocols address these concerns through:
A. Toxicological Compliance
- Heavy Metal Testing: PP resins are screened for lead, cadmium, and mercury via X-ray fluorescence (XRF), adhering to EU REACH and U.S. FDA standards.
- Migration Testing: Ensures no harmful substances leach into packaged goods, critical for food-grade applications like livestock feed.
B. Mechanical Safety
- Load-Bearing Capacity: VidePak’s FIBC bags withstand 5:1 safety factor ratios (e.g., 5,000 kg safe working load for a 1,000 kg design).
- Seam Strength: Ultrasonic seaming technology achieves 80–100 N/cm seam strength, preventing failures during transport.
3. Manufacturing Excellence: Starlinger Technology and Customization
VidePak’s 100+ circular looms and 30+ lamination machines, sourced from Austria’s Starlinger, enable unparalleled precision:
Parameter | VidePak Standard | Industry Average |
---|---|---|
Weaving Density | 10×10 strands/inch | 8×8 strands/inch |
Print Resolution | 175 LPI (lines per inch) | 150 LPI |
Moisture Barrier (BOPP) | <1.0 g/m²/24hr | <2.5 g/m²/24hr |
Example: A client requiring flame-retardant bags for construction waste received PE-coated valve bags with a limiting oxygen index (LOI) of 28%, exceeding the ISO 4589-2 benchmark of 26%.
4. Sustainability: Balancing Performance and Eco-Consciousness
While PP is recyclable (resin ID code 5), VidePak integrates biodegradable additives for compostable options. Their 2024 initiative reduced carbon footprint by 15% through:
- Energy Recovery Systems: Capturing heat from extrusion lines to power auxiliary units.
- Water-Based Inks: Eliminating volatile organic compounds (VOCs) in printing.
FAQs: Addressing Critical Concerns
Q1: How does VidePak ensure colorfastness in printed designs?
A: By using UV-cured inks and testing against ISO 105-B02 standards (500+ hours of xenon-arc exposure).
Q2: Are woven bags safe for food contact?
A: Yes, when produced with FDA-compliant PP and laminated with food-grade BOPP films. VidePak’s food-grade woven bags undergo third-party certification by SGS.
Q3: What distinguishes Starlinger equipment?
A: Starlinger’s circular loom technology ensures uniform weave density (±2% tolerance), critical for load stability.
5. Market Differentiation: Data-Driven Success
VidePak’s 2024 client survey highlights:
- 98% Satisfaction Rate: Attributed to zero reported leakage in 50,000+ valve bags shipped.
- 40% Faster Lead Times: Achieved via AI-driven production scheduling.
Conclusion: The Path Forward
The woven bag industry demands relentless innovation. VidePak’s fusion of material science, safety rigor, and Starlinger’s engineering positions it as a leader. As Ray summarizes: “Our bags don’t just carry goods—they carry trust.”
For businesses seeking reliability, custom-printed solutions tailored to exact needs, VidePak remains the benchmark.
Note: All data reflects 2025 industry standards and VidePak’s internal testing protocols.