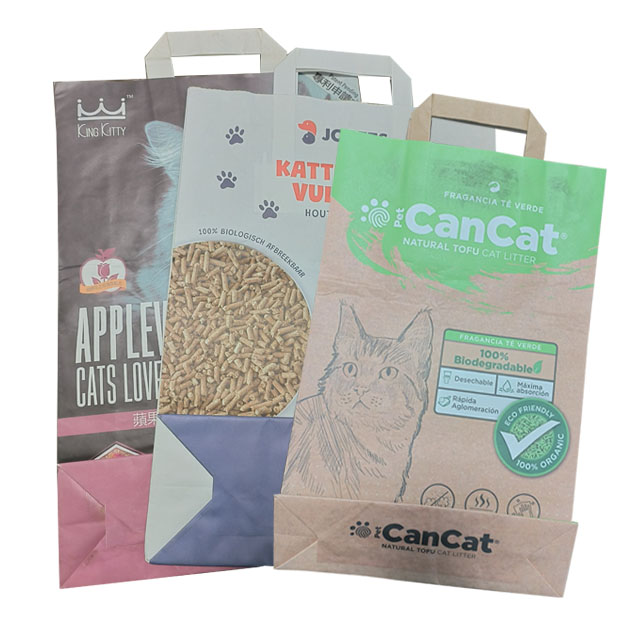
In today’s rapidly evolving world, packaging plays an essential role in safeguarding food products, particularly in the highly regulated food industry. Among the various packaging options, Food Grade Woven Fabric Bags have gained significant popularity due to their strength, flexibility, and environmental benefits. These bags are particularly used in storing and transporting food products, ensuring that the contents remain safe, dry, and protected from contaminants. However, ensuring that these bags meet the stringent standards required for food packaging involves meticulous attention to every detail—from the selection of materials to the manufacturing and transportation processes. Additionally, understanding the best manufacturing techniques such as stitching, sealing, and bag designs is crucial to meet industry standards and consumer expectations.
Key Considerations in Material Selection, Production, and Transportation
Material Selection for Food Grade Woven Fabric Bags
The foundation of any successful Food Grade Polypropylene Bags starts with high-quality materials. Polypropylene (PP) is the most commonly used material for producing Food Grade Woven Fabric Bags due to its non-toxic, durable, and moisture-resistant properties. It is essential that the PP material used for food-grade bags is virgin, not recycled, to avoid contamination from harmful chemicals. Furthermore, the material should comply with international standards such as FDA and EU regulations, ensuring that no harmful substances leach into the food.
Another critical factor is the quality of the woven fabric. The Food Grade Woven Sacks should be constructed with tightly woven fibers that ensure durability and resistance to tear and puncture. This is particularly important for maintaining the integrity of the packaging during transportation and handling, preventing any contamination or damage to the food inside.
Production Process for Food Grade Bags
The manufacturing process of Food Grade Woven Poly Bags must adhere to strict hygiene standards to prevent contamination. It begins with the selection of high-quality raw PP granules, which are then extruded into fibers and woven into fabric. At this stage, it is crucial to maintain clean production facilities to avoid any risk of contamination.
One important aspect of production is the lamination process, where an additional layer is applied to the woven fabric. This step can enhance the strength and moisture resistance of the bag, making it more suitable for packaging food products that may be sensitive to environmental conditions. Lamination also provides a barrier against dust, dirt, and other contaminants, ensuring that the food remains clean and safe.
Another consideration during production is the application of custom prints. Many food-grade woven bags feature custom printing for branding purposes. It is essential to use non-toxic inks that meet food safety standards to prevent any risk of chemical migration into the food.
Packaging and Transportation
Once the bags are produced, the next stage involves proper packaging and transportation. Ensuring that the Food Grade Woven Bags are stored in a clean and dry environment during transportation is key to preserving the quality of the product. The bags should be carefully packed to avoid damage, and extra care should be taken when handling and transporting food products to prevent contamination or physical damage.
During transportation, it is critical to avoid exposure to extreme temperatures or humidity, as these factors can compromise the integrity of the bags and, by extension, the safety of the food inside. Additionally, the bags should be transported in clean, sealed containers to protect them from dirt, pests, and other environmental factors that could affect the food.
Manufacturing and Sewing Techniques for Food Grade Woven Bags
The construction of Food Grade Woven Polypropylene Bags involves careful consideration of various factors, from the stitching and sealing methods to the choice of bag opening and closure. These elements play a significant role in ensuring that the bags are functional, secure, and compliant with food safety standards.
Stitching and Sealing Methods
The choice of stitching or sealing method used for Food Grade Woven Fabric Bags is crucial in ensuring durability and preventing leakage. The two primary methods are stitching and heat sealing, with ultrasonic welding becoming increasingly popular in recent years for certain applications.
- Stitching: In this traditional method, threads are used to sew the fabric together. The type of stitching used can vary, with single-needle, double-needle, and overlock stitches being the most common. The density and quality of stitching play an important role in the bag’s ability to hold its contents without breaking or tearing.
- Heat Sealing: In contrast to stitching, heat sealing uses high temperatures to fuse the edges of the fabric together, creating a strong bond without the need for stitching. This method is particularly suitable for Food Grade PP Bags because it ensures a leak-proof seal, which is essential for preventing contamination.
- Ultrasonic Welding: This advanced technique uses high-frequency sound waves to create a bond between the fabric layers. It offers superior strength and durability compared to traditional stitching or heat sealing and is ideal for high-volume production. It also eliminates the need for additional materials, such as stitching thread, which may potentially pose a risk for contamination.
Choice of Thread Material
The material used for stitching is also a key consideration. Threads made from food-safe, non-toxic materials such as polyester or nylon are commonly used for food-grade packaging. These materials are resistant to abrasion, high temperatures, and moisture, ensuring that the bag remains intact throughout its life cycle. Additionally, the stitching density, which refers to the number of stitches per unit length, should be optimized to ensure that the bag can carry heavy loads without tearing.
Bag Opening and Closure Design
The design of the bag opening and closure is another crucial factor in the functionality and safety of Food Grade Woven Sacks. Several closure options are available, each with its benefits and drawbacks:
- Open Mouth Bags: These bags are the most basic type, with an open top that can be sealed manually with a tie, tape, or other methods. They are ideal for products that are easy to close and do not require extensive sealing.
- Valve Bags: These bags feature a valve at the top, which allows the bag to be filled easily and sealed automatically. Valve bags are commonly used for packaging powders, grains, and other bulk food products. They offer excellent protection against contamination and are efficient for high-volume packaging.
- Heat Sealed Bags: Bags that use heat-sealing technology offer a secure closure with a strong, tamper-evident seal. They are ideal for packaging products that require airtight protection.
- Sewn Bags: These bags use stitching to close the opening, offering a more secure closure than open-mouth bags. However, they may not provide the same level of protection against contamination as heat-sealed or valve bags.
Table: Comparison of Bag Closure Methods
Closure Type | Strength | Tamper Protection | Ideal Application |
---|---|---|---|
Open Mouth | Medium | Low | Grains, Produce |
Valve Bag | High | High | Powders, Bulk Foods |
Heat Sealed | Very High | Very High | Dry and Wet Foods |
Sewn Bags | Medium | Low | Lightweight Products |
Conclusion
Food packaging plays a pivotal role in ensuring the safety, quality, and hygiene of food products. Food Grade Woven Fabric Bags, particularly those made from Food Grade Polypropylene Bags, offer a robust and versatile solution for packaging a variety of food items. By adhering to strict production standards, selecting the right materials, and employing high-quality manufacturing techniques, food-grade woven bags can be an excellent choice for safe and efficient food storage and transportation.
For a more in-depth exploration of packaging technologies, such as advanced Food Grade Woven Fabric Bags, refer to the versatility of Food Grade Woven Fabric Bags and the craftsmanship of Food Grade Polypropylene Bags.