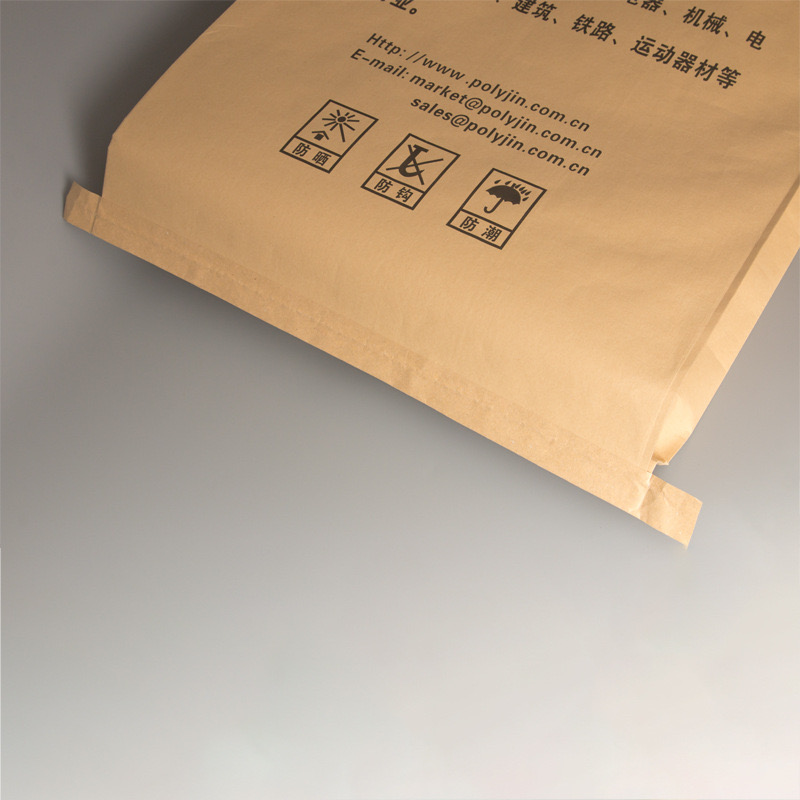
Food Grade Woven Fabric Bags, or Food Grade Polypropylene (PP) Bags, have become an essential solution in the packaging industry, offering a secure, durable, and cost-effective option for a variety of food products. These bags are widely used for packing grains, flour, sugar, spices, and pet food, among others. The key to ensuring that these bags meet the highest standards of food safety and quality lies in every step of the manufacturing and distribution process. From raw material selection and production to packaging and transportation, each stage must be carefully controlled to meet the stringent food-grade standards.
Raw Material Selection for Food Grade Woven Fabric Bags
The foundation of high-quality Food Grade Woven Sacks begins with the choice of raw materials. The fabric used in these bags is typically woven from polypropylene (PP), a thermoplastic polymer known for its strength, durability, and resistance to moisture. However, to meet food safety standards, the following considerations must be made during raw material selection:
- Food Grade Polypropylene: Only virgin (new) PP materials should be used in the production of food-grade bags. Recycled polypropylene can contain contaminants and harmful substances, which can compromise the safety of the packed food.
- FDA-Approved Materials: The polypropylene used should be compliant with regulations set forth by food safety authorities, such as the U.S. Food and Drug Administration (FDA) or the European Union’s EFSA standards. This ensures that the material is safe for direct contact with food products.
- Additives and Colorants: Any additives, colorants, or other chemical treatments must also be food-safe. They should not leach toxic substances into the packed food, and their use should be strictly controlled to meet safety standards.
For more information about ensuring the quality and compliance of materials, refer to Food Grade Woven Bags: Optimizing Packaging Efficiency and Quality.
Production Process and Quality Control
Once the appropriate raw materials are selected, the manufacturing process of Food Grade Polypropylene Bags begins. This stage involves several critical processes, such as weaving, lamination, and printing. Each step must be carefully controlled to ensure that the bags meet food safety standards.
- Weaving: The polypropylene yarn is woven into fabric using advanced machinery like circular looms. The quality of the weaving directly impacts the strength, durability, and overall integrity of the woven bag. Any defects in the fabric, such as holes or weak spots, can lead to contamination or breakage, which is especially critical when dealing with food products.
- Lamination and Coating: In many cases, the woven fabric is laminated or coated to enhance its durability and provide additional protection against moisture, dirt, and other contaminants. For food-grade applications, the coating should be non-toxic and should not interfere with the safety of the food. This is particularly important for bags used in packaging sensitive food items.
- Printing: Food-grade woven bags often feature printed designs for branding, labeling, or product identification. When printing on food-grade bags, the inks and dyes used must be non-toxic and compliant with food safety standards. The printing process should also be free from contamination to avoid introducing harmful chemicals.
- Quality Control: Stringent quality control checks should be in place at each stage of production to ensure that the bags meet the required standards. This includes checking the strength of the fabric, inspecting for defects, and testing the bags for their ability to withstand environmental conditions, such as moisture or UV exposure. For Food Grade PP Bags, testing should also verify that there are no harmful chemicals present.
Packaging and Sealing of Food Grade Poly Bags
After production, the next critical phase in ensuring food safety is the proper packaging and sealing of the Food Grade Woven Sacks. These bags must be securely sealed to protect the contents from contaminants, moisture, and other external factors during storage and transportation.
- Sealing Methods: For food-grade applications, the bags must be sealed properly to prevent leakage or contamination. Heat sealing or ultrasonic sealing is commonly used to achieve a secure, tamper-evident closure. These methods ensure that the bags remain airtight and prevent any external contaminants from entering.
- Packaging Hygiene: It is essential that the packaging process takes place in a clean environment. Any exposure to dust, bacteria, or other contaminants during packaging can compromise the safety of the food. Therefore, food-grade bags should be packaged in a sanitized area, and the packaging materials should also meet hygiene standards.
- Labeling: Proper labeling is another critical aspect of food-grade packaging. The labels should include relevant information such as the product’s expiration date, batch number, and any other details required by food safety regulations. These labels must be printed using non-toxic, food-safe inks.
For more details on food-grade packaging, see The Excellence of Mesh PP Bags and VidePak’s Comprehensive Quality Management System.
Transportation and Storage Considerations
Once the Food Grade Polypropylene Bags are produced, sealed, and packaged, they must be transported and stored under conditions that maintain their integrity and protect the packed food from contamination.
- Transportation: Food-grade woven bags should be transported in clean, dry conditions. Trucks, shipping containers, or storage areas should be free from harmful chemicals, odors, or moisture. It is also crucial to prevent physical damage to the bags during transportation, which could compromise their effectiveness.
- Storage: Food-grade bags should be stored in a temperature-controlled environment to prevent any degradation of the packaging material or the food product inside. Additionally, food-grade bags should be kept away from direct sunlight and extreme humidity to prevent them from becoming brittle or degraded.
- Stacking and Handling: The stacking of food-grade bags should be done in a way that minimizes the risk of contamination or physical damage. Bags should be stored off the ground to prevent exposure to moisture or dirt. Careful handling is essential to maintain the quality of the bags and ensure that the food inside remains safe.
Innovations in Food Grade Packaging: Seven-Layer Coextrusion
Recent advancements in packaging technology have introduced innovative solutions for food-grade woven bags. One such innovation is the development of seven-layer co-extruded films. These films offer superior protection against moisture, oxygen, and UV rays, making them ideal for packaging food products with high moisture or shelf-life concerns.
- Enhanced Protection: The multi-layer structure of co-extruded films enhances the bag’s barrier properties, providing additional protection against external contaminants and preserving the quality of the packed food for longer periods.
- Improved Durability: These films are designed to be more durable than traditional single-layer films, offering better resistance to punctures and tears. This makes them a reliable choice for food packaging, especially in applications where the bags will be exposed to rough handling or harsh environmental conditions.
- Sustainability: Seven-layer co-extrusion also offers sustainability benefits. By using advanced technology, these films can be made thinner while maintaining their protective properties, reducing the amount of plastic used in each bag.
For a closer look at the advantages of multi-layer co-extrusion, visit The Benefits and Applications of Breathable Woven Bags in Food Packaging.
Product Specifications Table
Parameter | Food Grade Woven Bags | Food Grade Polypropylene Bags | Food Grade Woven Sacks |
---|---|---|---|
Material Type | Virgin PP | Virgin PP | Virgin PP |
Food Grade Certification | FDA Approved | FDA Approved | FDA Approved |
Thickness | 50 – 120 microns | 50 – 120 microns | 50 – 120 microns |
Barrier Protection | Moisture and Dust Proof | Moisture and Dust Proof | Moisture and Dust Proof |
Printing | Non-toxic Ink | Non-toxic Ink | Non-toxic Ink |
Sealing Method | Heat Seal/Ultrasonic Seal | Heat Seal/Ultrasonic Seal | Heat Seal/Ultrasonic Seal |
Available Coatings | Lamination Option | Lamination Option | Lamination Option |
Customization Options | Size, Color, Print | Size, Color, Print | Size, Color, Print |
In conclusion, ensuring the safety, integrity, and compliance of Food Grade Woven Fabric Bags involves attention to detail across every step of the production and packaging process. By carefully selecting the right materials, employing advanced manufacturing techniques, and adhering to strict quality control protocols, manufacturers can deliver high-quality packaging solutions that meet the food safety standards necessary to protect consumers. Whether it’s through innovative packaging technologies or robust quality assurance systems, the future of food-grade packaging is bright, ensuring that food products are transported and stored safely and efficiently.
For further exploration on food-grade packaging, see the link to Food Grade Woven Sacks.