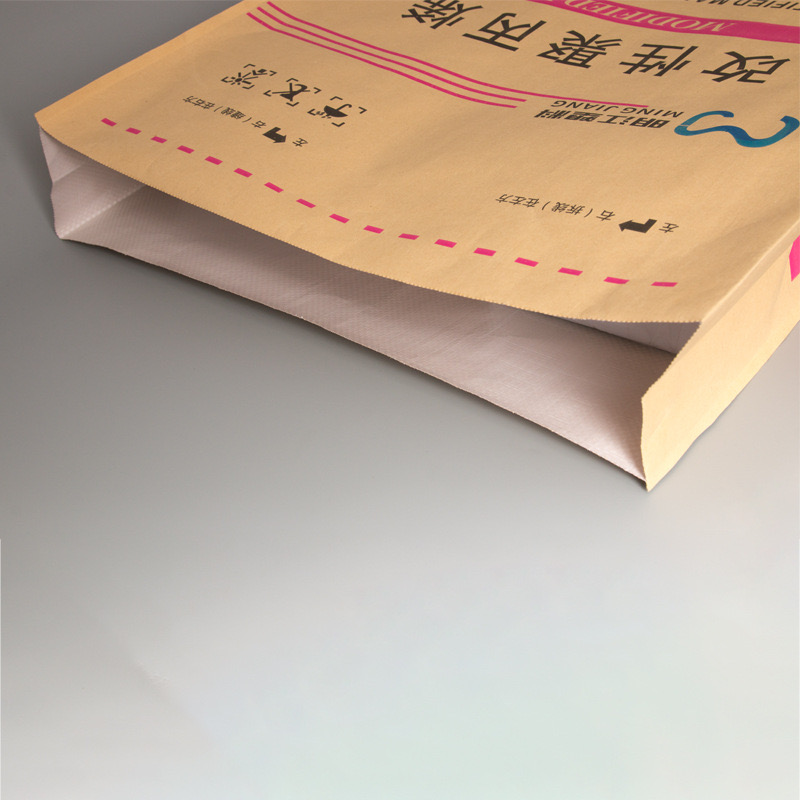
Food packaging has stringent standards to ensure the safety and quality of products that come in direct contact with consumables. When it comes to packaging food ingredients and products, using Food Grade Woven Fabric Bags is an effective and sustainable choice. However, ensuring that these bags meet the required safety and health standards involves paying attention to various factors, including materials selection, manufacturing processes, packaging, and transportation. In this guide, we will explore the steps required to ensure food-grade standards are met for Food Grade Woven Sacks, Food Grade PP Bags, and other woven fabric bags used in the food industry. Additionally, we will examine the different materials used for woven bags, comparing PP, HDPE, PE, and Aluminum foil for their unique qualities and functions.
Key Considerations for Food Grade Woven Fabric Bags
When selecting or manufacturing Food Grade Woven Fabric Bags, it is important to follow the appropriate regulations and guidelines to ensure that the bags remain safe for food packaging. This includes selecting the right raw materials, adhering to quality control measures during production, and ensuring safe storage and transport.
1. Materials Selection
The materials used in Food Grade Polypropylene Bags are critical to their safety and effectiveness. Polypropylene (PP) is the most commonly used material for food-grade woven bags. However, ensuring that the PP is non-toxic and free of harmful chemicals is essential. Manufacturers must ensure that the material complies with global standards, such as those set by the FDA (Food and Drug Administration) in the US, EFSA (European Food Safety Authority) in Europe, and other relevant regulatory bodies worldwide.
For optimal safety and durability, it is advisable to use Food Grade Poly Bags made from virgin polypropylene. This ensures that the bags are free from contaminants that may compromise food safety.
2. Production Processes
The production process of Food Grade Woven Bags must adhere to strict hygiene and safety standards. The following steps are key to ensuring compliance with food safety regulations:
- Cleanliness: All production equipment should be regularly sanitized to prevent contamination during the manufacturing process. Production facilities should follow Good Manufacturing Practices (GMP).
- Quality Control: During production, regular checks must be performed to test the strength, durability, and safety of the woven fabric. Testing methods include tensile strength tests, burst strength tests, and checks for chemical residues.
- Non-Toxic Inks: In cases where printing is required on the woven fabric bags, non-toxic inks must be used to ensure that no harmful substances leach into the food.
3. Packaging and Storage
Once manufactured, Food Grade Polypropylene Bags should be properly packaged to maintain their integrity during storage and transportation. The bags must be kept in a clean, dry environment and stored in a way that avoids contamination. Furthermore, care should be taken to avoid exposure to harsh chemicals, extreme temperatures, or any other environmental factors that could degrade the quality of the bags.
4. Transportation
Transporting Food Grade Poly Bags also requires specific attention. Bags should be transported in containers that are clean and sealed to prevent contamination. Any exposure to moisture, dirt, or other harmful substances during transit should be avoided. Additionally, the transportation process should ensure that the bags arrive at their destination in a timely manner without any damage.
For a more detailed exploration of the quality control and production standards for Food Grade Woven Fabric Bags, check out this article on industrial woven packaging bags aligning with policies and ESG standards.
Materials for Woven Bags: A Comparison
The material used in manufacturing woven bags greatly impacts their functionality, durability, and suitability for different applications. Here, we compare PP, HDPE, PE, and Aluminum foil for use in woven bags:
Material | Properties | Common Applications | Advantages | Disadvantages |
---|---|---|---|---|
Polypropylene (PP) | Lightweight, strong, resistant to moisture, heat, and chemicals | Food packaging, industrial packaging | Non-toxic, durable, recyclable, cost-effective | Sensitive to UV degradation, not as puncture-resistant |
High-Density Polyethylene (HDPE) | Strong, highly resistant to chemicals and abrasion, UV resistant | Chemical and agricultural packaging | Very strong, puncture-resistant, cost-effective | Can be brittle at lower temperatures |
Polyethylene (PE) | Soft, flexible, waterproof, heat sealable | Food packaging, retail packaging | Excellent moisture barrier, easy to process | Less durable than PP or HDPE, susceptible to tearing |
Aluminum Foil | Reflective, excellent moisture barrier, airtight | Packaging for products sensitive to moisture or light (e.g., coffee, snacks) | Superior barrier properties, protects from UV light, air-tight | Expensive, less recyclable than plastic |
1. Polypropylene (PP)
PP is the most widely used material in Food Grade Poly Bags. It offers an excellent balance between strength, flexibility, and cost. PP bags are resistant to moisture and chemical contamination, making them a reliable choice for packaging food products. Additionally, PP bags can be recycled, making them an eco-friendly option.
2. High-Density Polyethylene (HDPE)
HDPE is commonly used for industrial applications, where strength and resistance to punctures are needed. It is often used in packaging chemicals, fertilizers, and agricultural products. Although HDPE is strong, it is more brittle than PP, particularly under cold temperatures, which can be a limiting factor for certain food applications.
3. Polyethylene (PE)
PE is an excellent choice for packaging products that require a flexible, moisture-resistant barrier. It is commonly used in packaging fresh produce, bakery goods, and other food items. However, PE bags are not as durable as PP or HDPE, which limits their application in more heavy-duty food packaging scenarios.
4. Aluminum Foil
Aluminum foil is primarily used for high-performance packaging that needs to protect the contents from moisture, light, and oxygen. It is often used in packaging items such as coffee, nuts, and snacks. However, aluminum foil is more expensive than plastic materials and is less recyclable, which could limit its use in large-scale, environmentally conscious food packaging applications.
For a deeper dive into the innovations and benefits of using Food Grade PP Bags in various applications, take a look at The Versatility and Benefits of FIBCs.
Conclusion
Ensuring that Food Grade Woven Fabric Bags meet the necessary food safety standards requires attention to detail at every step, from material selection to production processes, packaging, and transportation. By using Food Grade Polypropylene Bags made from virgin PP and following strict safety guidelines, manufacturers can ensure that their woven fabric bags are safe, durable, and compliant with all necessary regulations. Additionally, selecting the appropriate material—whether it’s PP, HDPE, PE, or Aluminum foil—based on the specific needs of the packaging application is crucial for achieving optimal performance and food safety. By carefully considering all of these factors, businesses can confidently use Food Grade Woven Sacks and Food Grade Poly Bags in food packaging while maintaining high safety and quality standards.