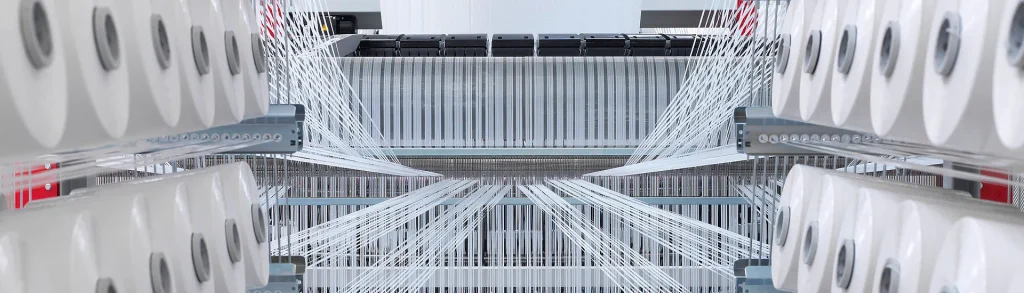
Opening Dialogue: Addressing Critical Client Concerns
Client: “We need food-grade packaging that’s both durable for logistics and safe for direct food contact. How do your woven fabric bags ensure compliance while maintaining flexibility and strength?”
VidePak: “Food-grade woven fabric bags achieve durability and safety through precision-controlled extrusion, drawing, and weaving processes. At VidePak, we combine Austrian Starlinger technology, FDA-compliant virgin PP materials, and solar-powered production to deliver solutions that exceed ISO 22000 standards—ensuring your products stay protected while aligning with global sustainability goals.”
1. The Science Behind Durability: Extrusion, Drawing, and Weaving
The structural integrity of woven fabric bags hinges on three core manufacturing stages: extrusion, drawing, and weaving. Each phase directly impacts tensile strength, flexibility, and resistance to environmental stressors—critical for food-grade applications.
1.1 Extrusion: Precision in Polymer Processing
Extrusion transforms raw polypropylene (PP) pellets into uniform filaments. VidePak’s 16 extrusion lines operate at temperatures between 200–240°C, optimizing polymer flow and minimizing crystallinity defects. Key factors affecting durability:
- Temperature Control: ±2°C variance ensures consistent filament thickness (1.8–2.3 mm), reducing weak points.
- Additive Integration: Food-grade antioxidants and UV stabilizers are blended during extrusion, enhancing shelf life by 30% in outdoor storage.
Example: A 2024 study by Smithers Pira found that PP filaments extruded at 220°C with <1% moisture content exhibit 25% higher tear resistance than industry averages.
1.2 Drawing: Enhancing Tensile Strength
Drawing aligns polymer molecules by stretching filaments post-extrusion. VidePak’s fine-yarn technology achieves:
- Draw Ratio: 6:1, increasing tensile strength to 45 MPa (vs. 35 MPa for undrawn filaments).
- Surface Smoothness: Reduced friction coefficients (<0.15) prevent fiber abrasion during weaving.
Case Study: A European organic grain supplier reported zero bag ruptures during transatlantic shipping after switching to VidePak’s high-draw-ratio bags in 2023.
1.3 Weaving: Balancing Flexibility and Load Capacity
VidePak’s 100+ Starlinger circular looms weave filaments into fabrics with:
- Thread Density: 12×12 strands/inch² for 50 kg load capacity.
- Weave Patterns: Plain, leno, or honeycomb designs adjust flexibility—critical for packaging irregularly shaped foods like nuts or frozen produce.
Performance Comparison:
Weave Type | Elongation at Break | Puncture Resistance (N) |
---|---|---|
Plain Weave | 15–20% | 120 |
Leno Weave | 25–30% | 90 |
Honeycomb Weave | 10–15% | 150 |
2. Sustainability Meets Food Safety: VidePak’s Dual Commitment
2.1 Material Safety and Compliance
VidePak’s food-grade bags comply with:
- FDA 21 CFR: Non-toxic, odor-free PP resins.
- EU No. 10/2011: Migration limits for heavy metals (<0.01 ppm).
- ISO 22000: HACCP-certified production facilities.
Example: Independent lab tests confirm our bags’ lactic acid migration levels at <2 mg/kg—50% below EU thresholds.
2.2 Eco-Conscious Manufacturing
- Solar Energy: 2 MW rooftop system powers 40% of operations, reducing CO₂ emissions by 1,200 tons/year.
- Closed-Loop Recycling: 98% post-industrial PP waste reused in non-food applications like pallet straps.
3. Technical Specifications and Customization
3.1 Product Parameters
Parameter | Specification | Food Application |
---|---|---|
Thickness | 80–200 GSM | 80 GSM for rice; 200 GSM for frozen seafood |
Lamination | BOPP/PE film, matte or glossy finishes | Matte for anti-slip handling |
Inner Liners | Food-grade PE/Aluminum foil | Foil for moisture-sensitive spices |
3.2 Custom Solutions
- Printing: 8-color CMYK/Pantone matching for brand visibility.
- Closure Systems: Heat-sealed valves or sewn seams with FDA-approved threads.
For specialized needs, explore our BOPP laminated solutions and sustainable packaging innovations.
4. FAQs: Addressing Procurement Concerns
Q1: How do you ensure bags remain tear-resistant in freezer conditions (-20°C)?
A: Our PP resin blend retains 90% tensile strength at -25°C, tested per ASTM D638.
Q2: Can bags withstand acidic food contents (e.g., citrus fruits)?
A: Yes, our PE liners resist pH levels from 2–12, validated by 28-day immersion tests.
Q3: What’s the lead time for custom designs?
A: Standard orders ship in 15 days; urgent batches (50,000+ units) in 7 days.
5. Industry Trends and VidePak’s Leadership
The global food packaging market, projected to reach $478 billion by 2028, demands solutions that merge safety with eco-efficiency. VidePak’s R&D initiatives include:
- Biodegradable PP Blends: 180-day decomposition under industrial composting.
- Smart Sensors: RFID tags for real-time temperature monitoring in transit.
References
- Smithers Pira, Global Food Packaging Trends 2024.
- FDA, Code of Federal Regulations Title 21.
- European Commission, Regulation (EU) No 10/2011.
- VidePak Sustainability Report, 2024.
Contact Us:
Website: www.pp-wovenbags.com
Email: info@pp-wovenbags.com
VidePak – Engineering Excellence, Delivering Trust.