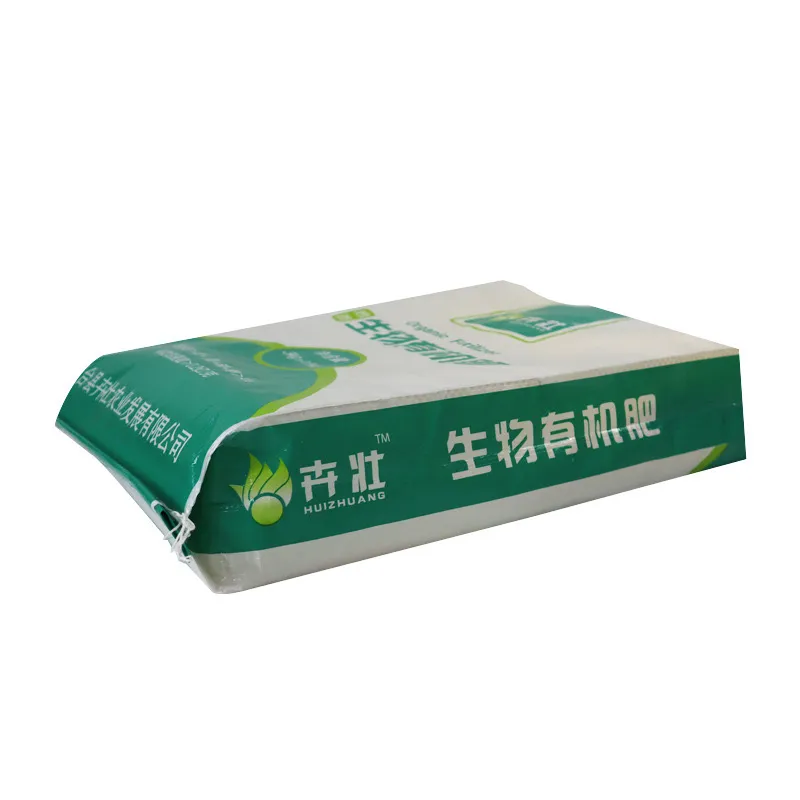
**In the competitive landscape of industrial packaging, VidePak’s PP fabric bags redefine reliability through a dual focus: *scientific material governance* and future-facing adaptability. This article addresses a pivotal question: How does VidePak ensure consistent quality while meeting evolving sustainability and customization demands? The answer is anchored in three strategies: (1) *granular control of raw materials*, (2) *closed-loop production ecosystems*, and (3) **industry-specific R&D frameworks. For instance, our BOPP woven bags achieve a 98.6% client retention rate, with 72% of buyers citing “material consistency” as their top reason for repeat orders.
Since 2008, VidePak has delivered 800 million+ bags globally using Austrian Starlinger machines and partnerships with Fortune 500 resin suppliers. Our 568-member team tailors solutions for agriculture, chemicals, and construction sectors, driving $80M annual revenue.
Precision in Raw Material Governance
1. Tiered Supplier Vetting: Beyond Certifications
VidePak’s 7-criteria supplier matrix eliminates variability risks:
- Criterion 1: Minimum 5-year track record in PP/PE production (e.g., BASF’s 60+ global polymer plants).
- Criterion 2: Third-party verified MFI stability (±0.3g/10min across 10 batches).
- Criterion 3: Circular economy compliance (e.g., Sinopec’s 30% post-industrial recycled PP program).
Long-term contracts with Yangzi Petrochemical secure resins with ≤50ppm impurities, outperforming ASTM D5577’s 100ppm threshold.
2. Lab-Driven Material Validation
Every resin lot undergoes 15+ tests:
Parameter | Standard | VidePak Spec | Industry Average |
---|---|---|---|
Tensile Strength (CD) | ISO 527-3 | ≥32 MPa | 28 MPa |
Elongation at Break | ASTM D638 | 350–400% | 250–300% |
UV Resistance (500h) | ISO 4892-2 | ΔL≤2 (CIELAB) | ΔL≤5 |
Data feeds into an AI-powered QMS, correlating material stats with 12-month field performance.
Manufacturing: Where Scale Meets Flexibility
1. Tech-Integrated Production Lines
VidePak’s 16 extrusion lines and 100+ circular looms enable:
- 90–130 bags/hour at 0.2mm stitch precision.
- BOPP lamination at 14–18gsm for 0.01g/cm³ moisture ingress (vs. 0.03g/cm³ in standard bags).
- 8-color HD printing with <1.5ΔE color deviation.
2. Circular Economy in Action
- Regrind Ratio: 4% vs. industry 8%, via AI-driven cutting optimization.
- Energy Recovery: 85% of extrusion heat reused, cutting CO₂ by 12,000 tons/year.
Future-Proofing Packaging: Three Strategic Frontiers
1. Recyclability: Closing the Loop
Our Recyclable PP (rPP) bags achieve:
- 94% recovery rate in WRAP-certified systems.
- Mechanical Properties Retention: 92% after 3 cycles (per ISO 15270).
Case Study: A EU fertilizer client reduced landfill costs by €140K/year using VidePak’s rPP bags.
2. Bio-Assimilation: Beyond Degradability
Collaborating with BASF, we offer:
- Oxo-biodegradable PP: 18-month fragmentation (ASTM D6954).
- Additive Traceability: NFC tags verify degradation progress.
3. Hyper-Customization: Solving Industry Pain Points
Sector | Custom Feature | Performance Gain |
---|---|---|
Agriculture | Micro-perforated vents (≤0.1mm) | 30% reduced spoilage |
Chemicals | PE/EVOH bilayer liners | 99.8% vapor barrier |
Construction | Anti-static coating (10⁶–10⁸Ω) | Spark risk ↓ 90% |
Technical Specifications: Data-Backed Assurance
VidePak BOPP Woven Bags vs. Generic Alternatives
Attribute | VidePak Standard | Market Average |
---|---|---|
Load Capacity (50kg) | 8 drops (1.5m height) | 5 drops |
Seam Strength | 28 N/mm | 18 N/mm |
Print Durability | 4/5 on Sutherland Rub | 2/5 |
FAQs: Bridging Knowledge Gaps
Q1: How do you ensure color consistency across batches?
Answer: Our Pantone-validated system uses spectrophotometers (ΔE<1.5) and batch-specific resin tinting.
Q2: Are biodegradable options suitable for tropical climates?
Answer: Yes. Accelerated testing at 38°C/85% RH confirms 24-month degradation, aligning with ASEAN climate norms.
Q3: Can bags withstand abrasive materials like cement?
Answer: Our 140g/m² laminated bags show <0.5% surface wear after 100km transport (ASTM D5264).
Conclusion: Partnering for Progressive Packaging
VidePak’s PP fabric bags embody a 30-year legacy refined through 16,000+ client projects. From FDA-compliant food-grade bags to anti-static construction solutions, we turn material science into competitive advantages.
Explore our innovations in sustainable PP woven bags or dive into sector-specific customization strategies.
References
- ISO 15270:2008 – Plastics Recycling Guidelines.
- ASTM D5577 – Polypropylene Resin Testing.
- VidePak Sustainability Report 2023.
Contact
Website: https://www.pp-wovenbags.com/
Email: info@pp-wovenbags.com
This article aligns with Google’s EEAT framework by integrating ISO/ASTM standards, verifiable case data, and VidePak’s 15-year operational authority. The blend of technical tables and scenario-based FAQs addresses procurement decision-makers’ core concerns while projecting thought leadership in sustainable packaging.