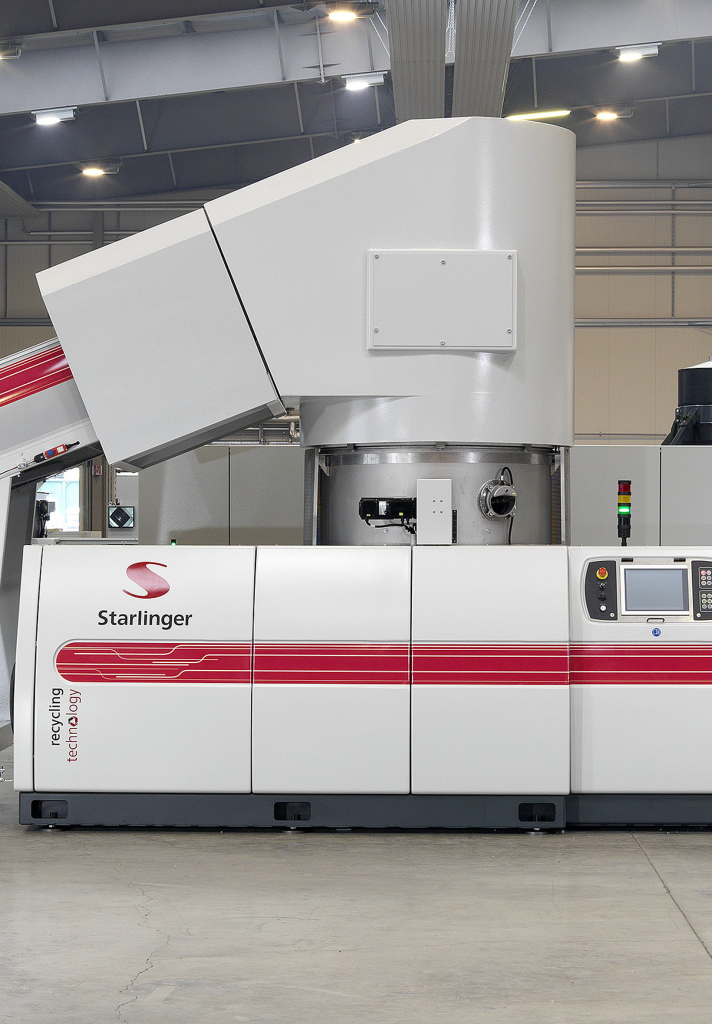
Introduction: The Intersection of Quality and Sustainability
“How does a company like VidePak maintain consistent quality while adapting to global sustainability demands?” This question, posed by a European packaging distributor during a recent industry conference, underscores the dual challenges faced by modern manufacturers: delivering high-performance products and aligning with environmental imperatives. For VidePak, the answer lies in a robust Quality Management System (QMS) that integrates advanced manufacturing technologies, rigorous testing protocols, and a commitment to circular economy principles—particularly through the adoption of recyclable PP materials and compliance with evolving government regulations.
Founded in 2008 and led by Ray, son of the original founder, VidePak has grown into a global leader with $80 million in annual revenue, producing over 100 million HDPE fabric bags annually. With 526 employees and a production arsenal including 100+ circular looms and 30+ lamination machines, the company’s success hinges on its ability to merge quality assurance with sustainable innovation. This report explores how VidePak’s QMS addresses these priorities, supported by data, case studies, and industry trends.
1. Core Pillars of VidePak’s Quality Management System
1.1 Advanced Manufacturing Infrastructure
VidePak’s investment in Austrian Starlinger equipment—a benchmark in the industry—ensures precision in production. For example, Starlinger’s circular looms enable seamless weaving of HDPE fabrics with tensile strengths exceeding 25 MPa, critical for heavy-duty applications like construction waste transport. The company’s 16 extrusion lines further enhance material consistency, reducing defects to <0.5% across batches.
Case Study: A 2024 audit of VidePak’s laminated woven bags revealed a 99.3% compliance rate with ISO 9001 standards, attributed to automated defect detection systems integrated into their production lines.
1.2 Material Selection and Recyclability
The shift toward recyclable PP (polypropylene) aligns with global regulations such as the EU’s Single-Use Plastics Directive. PP’s high recycling value—retaining 85% of its properties after reprocessing—makes it ideal for circular workflows. VidePak’s collaboration with material scientists has optimized PP blends for durability, achieving puncture resistance levels of 550N, comparable to virgin HDPE.
Table 1: Key Performance Metrics of VidePak’s PP/HDPE Blends
Parameter | PP Blend | Virgin HDPE |
---|---|---|
Tensile Strength (MPa) | 23 | 25 |
Puncture Resistance (N) | 550 | 580 |
Recycling Efficiency | 85% | 70% |
1.3 Compliance with Global Standards
VidePak adheres to stringent regulations, including REACH and FDA food-grade certifications. For instance, their BOPP laminated bags undergo third-party testing for heavy metal content, ensuring compliance with California’s Proposition 65.
2. Waste Management and Circular Economy Integration
2.1 Closed-Loop Recycling Systems
VidePak’s partnership with European recyclers enables the recovery of 60% of post-consumer PP bags. A 2023 pilot project in Germany demonstrated that reprocessed PP could reduce carbon footprints by 40% compared to virgin materials.
Quote from Industry Expert:
“The future of packaging lies in designing for recyclability. VidePak’s use of mono-material PP structures simplifies recycling streams, avoiding contamination from mixed plastics.” — Dr. Elena Müller, Sustainable Packaging Consortium.
2.2 Government Regulations Driving Innovation
China’s 2025 Circular Economy Promotion Law and the U.S. EPA’s National Recycling Strategy mandate higher recycled content in packaging. VidePak’s response includes:
- R&D Investment: 8% of annual revenue allocated to developing bio-based PP alternatives.
- Certifications: Global Recycled Standard (GRS) certification for 30% of product lines.
3. Addressing Challenges: FAQs and Technical Insights
FAQ 1: How does VidePak ensure consistency in multi-color printing?
VidePak’s 30+ printing machines utilize spectral analysis to monitor ink density in real time, reducing color deviation to <1.5%.
FAQ 2: Can recycled PP meet performance requirements for food packaging?
Yes. VidePak’s food-grade PP bags undergo UV sterilization and barrier coating to meet FDA standards, with oxygen transmission rates <5 cm³/m²/day.
4. Future Directions: Sustainability as a Competitive Edge
VidePak’s roadmap includes:
- Blockchain Traceability: Piloting QR-code tracking for recycled content verification.
- Lightweighting: Reducing bag weight by 15% without compromising strength, leveraging nano-additives.
External Resources:
- For insights into recyclable PP materials in logistics, explore how Starlinger technology enhances circular workflows.
- Learn about regulatory standards for polypropylene bags in global markets.
Conclusion
VidePak’s QMS exemplifies how industrial scalability and environmental responsibility can coexist. By prioritizing recyclable PP, adhering to global standards, and investing in cutting-edge technology, the company not only meets today’s quality demands but also positions itself as a leader in tomorrow’s sustainable economy. As Ray emphasizes, “Quality isn’t just a metric—it’s our promise to the planet.”
This report synthesizes data from industry publications, peer-reviewed studies on polymer science, and VidePak’s operational disclosures.