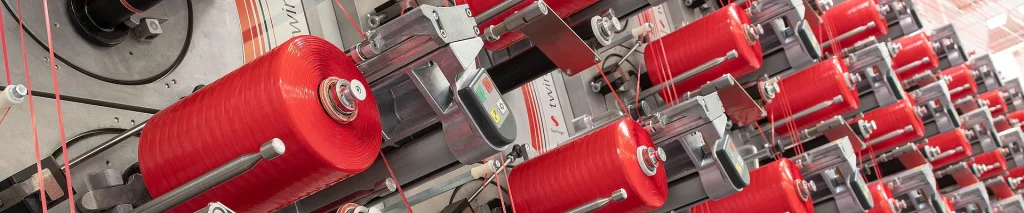
In the packaging industry, Paper Valve Woven Bags have emerged as a versatile and reliable solution, particularly in sectors requiring durable, moisture-resistant packaging. These bags, which blend the strength of woven polypropylene with the aesthetic and barrier properties of paper, cater to the packaging needs of industries such as agriculture, food, and construction. However, achieving consistent quality in Valve Woven Bags can be challenging due to various quality control parameters. At VidePak, we prioritize rigorous testing and quality assurance to ensure that each bag meets industry standards and customer expectations. Paper Valve Woven Bags offer significant value to our clients, combining resilience, customizable features, and enhanced protection.
Overview of Paper Valve Woven Bags Quality Requirements
The durability of Paper Valve Woven Sacks is heavily influenced by multiple factors, including material selection, manufacturing process, and finishing techniques. Below, we explore some common quality challenges in the production of Kraft Valve Woven Bags and detail VidePak’s approach to maintaining superior standards.
Common Quality Issues in Valve Woven Bags and Their Impact
- Thickness Variability: Thickness inconsistency can affect bag strength and capacity. Variations in thickness may lead to puncture risks, especially when handling sharp or abrasive contents.
- Uneven Cutting and Frayed Edges: Rough or uneven edges on Valve PP Bags not only compromise the bag’s appearance but may also increase the risk of tearing.
- Color Inconsistencies: Color uniformity is critical for brand recognition and quality perception. Poor color matching can lead to dissatisfaction in highly competitive markets.
- Inaccurate Weight and Tolerance Control: Weight consistency directly influences the bag’s performance and storage capacity. Deviations from weight specifications impact product reliability.
- Low Tensile Strength and Elongation: Bags lacking adequate tensile strength and elongation properties are prone to ruptures under load, leading to potential content leakage and product wastage.
- Insufficient Impact Resistance: This parameter is crucial for bags used in transport, where they may be subjected to various impacts. Low impact resistance affects bag reliability and increases handling risk.
- Poor UV Resistance and Aging Performance: UV resistance is necessary for bags exposed to sunlight during storage or transportation. Bags with low UV protection degrade faster and are prone to brittleness.
- Environmental Compliance: Meeting environmental standards is increasingly important for sustainability-conscious clients. This includes the use of non-toxic, recyclable, and biodegradable materials.
VidePak’s Comprehensive Quality Control Measures
At VidePak, we implement a series of precise quality control measures for each of these potential issues to ensure the Valve Woven Bags consistently meet our high standards. These checks are performed across the production process to guarantee end products that are safe, durable, and efficient for a variety of applications.
Quality Parameter | Description | Testing Method |
---|---|---|
Thickness Tolerance | Ensures uniform thickness to prevent punctures or splits. | Measured with micrometers. |
Edge Smoothness | Verifies the neatness of cut edges to prevent fraying. | Visual and tactile inspection. |
Color Consistency | Confirms uniform color for branding and aesthetic appeal. | Spectrophotometer testing. |
Weight Control | Guarantees accurate weight per customer specifications. | Precision scales. |
Tensile Strength and Elongation | Determines the ability of bags to withstand weight and stretching. | Tensile testing machine. |
Impact Resistance | Measures bag resistance to handling impacts during transport. | Drop and compression tests. |
UV Resistance | Assesses durability under sunlight exposure. | Accelerated UV aging tests. |
Environmental Compliance | Ensures materials are safe, recyclable, and non-toxic. | Chemical analysis and certifications. |
Key Quality Testing Parameters Explained
- Thickness Tolerance: Consistent bag thickness is crucial for ensuring structural integrity, especially in Paper Valve Woven Sacks used in construction and agriculture. At VidePak, thickness is measured with precision instruments to maintain strict tolerance levels, ensuring optimal protection and resilience.
- Edge Smoothness and Fray Detection: The bag edges are inspected to prevent fraying. Clean edges are essential to avoid unnecessary wear and tear, which can lead to premature product failure. Automated cutting systems at VidePak enable clean, precise cuts that meet stringent quality standards.
- Color Consistency: Visual consistency across Valve Woven Bags is maintained through color-matching techniques using advanced spectrophotometers. This ensures that every batch meets customer-specific branding requirements, delivering consistent and professional results.
- Weight and Tolerance Control: The weight of each Valve PP Bag is carefully controlled to guarantee product reliability. Variations in weight can impact the bag’s capacity and storage efficiency. By maintaining exact weight specifications, VidePak ensures reliable and efficient packing solutions.
- Tensile Strength and Elongation: Paper Valve Woven Bags need to resist forces that could cause tearing or stretching under load. Testing for tensile strength and elongation helps to ensure that each bag can handle the intended weight without deformation. This test is particularly important for bags used in high-stress applications like bulk material handling.
- Impact Resistance: VidePak’s impact resistance testing evaluates the bag’s durability during transport, where it may encounter bumps or drops. We conduct drop and compression tests to simulate real-world handling scenarios, ensuring that each bag meets industry standards for resilience.
- UV Resistance and Aging: Exposure to sunlight can significantly degrade polypropylene materials. Our UV resistance tests simulate extended sun exposure to assess bag durability. This test is crucial for bags stored outdoors, as it ensures a longer lifespan and reduced brittleness over time.
- Environmental Compliance: VidePak prioritizes eco-friendly practices by using recyclable and non-toxic materials. Environmental compliance testing guarantees that our bags meet sustainability standards without compromising quality. For clients concerned about sustainability, our bags are designed to minimize environmental impact.
Why Quality Control Matters in Kraft Valve Woven Bags
High-quality Kraft Valve Woven Bags offer essential protection against environmental factors such as moisture, sunlight, and physical impacts. By investing in rigorous quality control, VidePak ensures that these bags meet the unique needs of various industries. In applications ranging from food storage to industrial packaging, these bags offer the durability and reliability needed to protect valuable contents.
Benefits of Rigorous Testing for Our Customers
- Enhanced Durability: Strict quality control testing guarantees long-lasting bags that can withstand challenging conditions, reducing replacement costs for our clients.
- Improved Brand Image: Consistent color and quality reinforce brand identity, promoting a reliable image among end consumers.
- Cost Efficiency: Quality products minimize the risk of product damage, reducing losses due to spoilage or leakage during transportation.
- Environmental Responsibility: VidePak’s commitment to eco-friendly materials means that customers can rely on bags that not only perform well but also support environmental sustainability goals.
Conclusion
VidePak’s Paper Valve Woven Bags are manufactured with attention to every detail, ensuring they exceed expectations for durability, aesthetics, and environmental responsibility. Through a combination of innovative technology and rigorous quality control measures, our bags meet the diverse requirements of global markets, including agriculture, construction, and food industries. Each Valve Woven Bag undergoes a stringent quality testing process, offering VidePak’s clients confidence in every bag’s performance and sustainability.
Our dedication to quality and customer satisfaction is evident in the extensive testing procedures applied across our product line. With more than 30 years of industry experience, VidePak continues to set the benchmark in woven bag manufacturing, providing reliable and customizable packaging solutions that cater to evolving market demands.