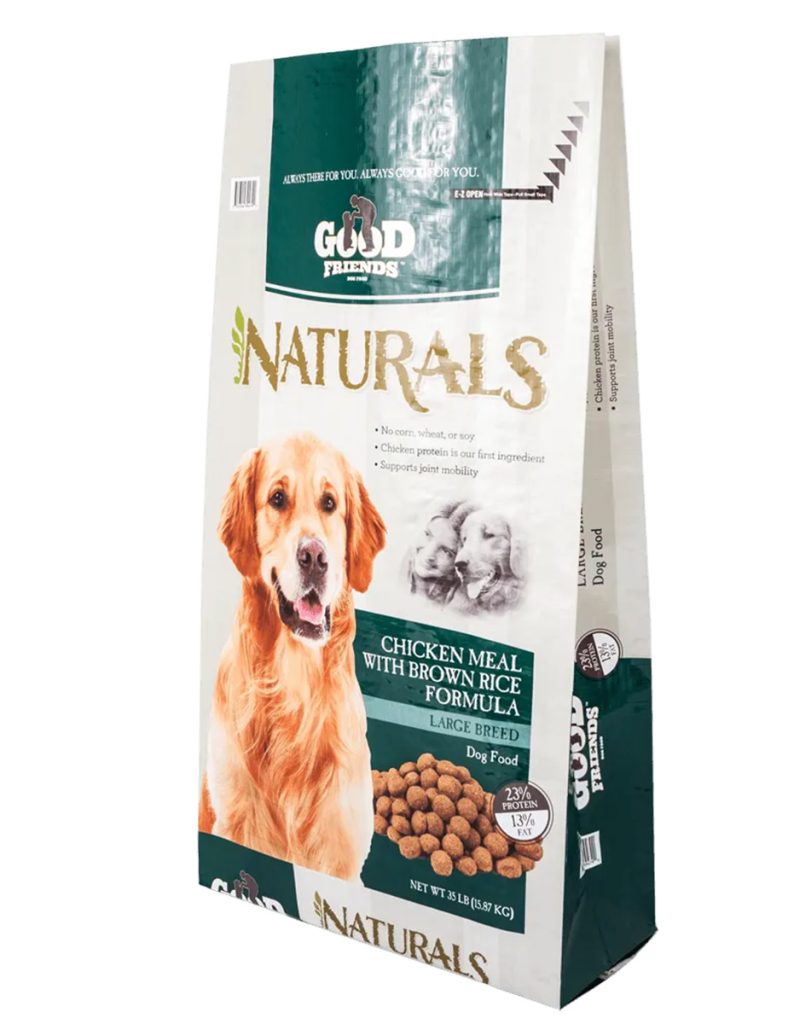
Polypropylene bags, also known as PP bags or polypropylene sacks, are widely used in various industries due to their strength, durability, and cost-effectiveness. These bags play a significant role in the packaging of different products, including agricultural items, chemicals, and construction materials. However, the quality of these bags largely depends on the raw materials used and the manufacturing process. This article explores the importance of quality control in the production of polypropylene woven bags, specifically focusing on the quality inspection of the raw materials such as PP and PE granules.
Importance of Quality Control in Polypropylene Bags
Quality assurance is essential for ensuring the durability, strength, and overall performance of polypropylene bags. To achieve high-quality PP woven bags, it is crucial to pay close attention to every stage of production—from the selection of raw materials to the final inspection of the finished product. The quality of polypropylene sacks depends on several factors, such as the appearance, density, melt flow index (MFI), tensile strength, and chemical resistance of the raw materials.
The raw material used in the production of polypropylene woven bags is polypropylene granules. These granules undergo a series of quality checks before they are processed into bags. It is vital that these quality control checks are strictly adhered to, as the properties of the final product, including its resistance to wear, tear, and UV damage, depend on the quality of the raw materials.
Raw Material Quality: PP and PE Granules
Polypropylene and polyethylene (PE) are two key materials used in the production of woven bags. While polypropylene is the primary material for most woven bags, PE is often used in combination with PP in applications requiring added moisture protection, such as in PE woven bags.
Key Parameters for Quality Inspection of PP and PE Granules
To ensure the production of high-quality woven bags, manufacturers need to conduct rigorous tests on the raw materials before processing. The following parameters are essential for assessing the quality of PP and PE granules:
Parameter | Description | Accepted Values |
---|---|---|
Appearance | Visual inspection of the granules for impurities or defects. | Uniform, no discoloration or foreign materials. |
Melt Flow Index (MFI) | Measures the ease of flow of the material when melted, indicating its processing behavior. | 1 to 10 g/10 min (PP) depending on grade. |
Density | Determines the material’s density, affecting its strength and durability. | 0.90 to 0.92 g/cm³ (PP) for standard grades. |
Tensile Strength | Indicates the maximum stress the material can withstand without breaking. | 30 to 40 MPa (PP). |
Elongation at Break | Measures how much the material can stretch before breaking, affecting flexibility. | 5-30% (PP). |
Heat Resistance | Evaluates the material’s ability to withstand high temperatures without deforming. | HDT above 100°C (PP). |
Chemical Resistance | Assesses the material’s resistance to chemicals, particularly in applications such as agricultural packaging. | Excellent resistance to alkalis and weak acids. |
UV Resistance | Determines the material’s ability to resist UV degradation, important for outdoor applications. | UV stabilizer incorporated for longer shelf life. |
Each of these parameters plays a crucial role in determining the overall performance and durability of the finished polypropylene bags. Testing the granules before production ensures that only the best materials are used in the manufacturing process.
PP Bags Production Process
The production of polypropylene bags involves several stages, from the extrusion of PP granules to the weaving and finishing of the bags. Below is a detailed overview of the PP bags production process:
- Extrusion: The first step involves melting the polypropylene granules and extruding them into flat films or tapes. This is typically done using an extrusion machine. The properties of the extruded film are influenced by the quality of the PP granules, so it’s important that the raw materials pass all quality tests before this stage.
- Weaving: After extrusion, the films are woven into a fabric using looms. The weave density and type depend on the intended use of the bags. Woven fabric is produced by interlacing the polypropylene films, forming a strong and flexible material suitable for various applications.
- Lamination (if applicable): In some cases, the woven fabric is laminated with a layer of PE film to provide additional strength or moisture resistance. This is especially common in PE woven bags, which are used for products that require extra protection from moisture.
- Printing: Custom designs or logos can be printed on the woven bags using flexographic or rotogravure printing techniques. This stage adds value to the bags, allowing for brand recognition or product identification.
- Finishing: The final stage includes the cutting and sewing of the woven fabric into the desired bag shape. This may also involve adding features such as handles, valve openings, or gussets depending on the customer’s specifications.
Throughout these stages, quality control checks are performed to ensure that the bags meet the required standards. In addition to the raw material tests mentioned earlier, these checks include testing for size, weight, strength, and appearance.
Testing and Quality Control in Woven Bag Manufacturing
After the polypropylene sacks or PE woven bags are produced, they undergo a series of tests to ensure that they meet industry standards and customer requirements. Some of the common tests include:
- Tensile Strength Test: This test measures the bag’s ability to withstand the forces applied during handling, storage, and transportation. The bag should not tear or break under normal conditions.
- Bursting Strength Test: This test determines the bag’s resistance to pressure. Bags used for heavy-duty applications need to withstand high internal pressures without bursting.
- UV Resistance Test: For polypropylene bags used outdoors, UV resistance is crucial. These bags must be able to resist degradation from exposure to sunlight, especially for applications like agricultural packaging.
- Moisture Resistance Test: For PE woven bags or bags with PE liners, moisture resistance is tested to ensure that the contents are protected from humidity or water.
- Size and Weight Inspection: To meet customer specifications, the size and weight of the bags are checked to ensure that they fall within the acceptable range.
- Seal Strength Test: For bags with heat-sealed openings, the strength of the seal is critical to prevent leaks and contamination.
Benefits of High-Quality Polypropylene Bags
Investing in high-quality polypropylene woven bags has several benefits for manufacturers and end users alike. These benefits include:
- Durability: High-quality PP woven bags are designed to withstand harsh conditions, including extreme weather, rough handling, and exposure to UV rays.
- Cost Efficiency: Although high-quality bags may have a higher initial cost, they offer better performance and longer lifespans, reducing the need for frequent replacements.
- Customizability: With customizable options available, polypropylene bags can be tailored to specific needs, whether for branding, capacity, or functionality.
- Sustainability: Many polypropylene bags are recyclable, making them an environmentally friendly option for packaging solutions.
Conclusion
Quality control in the production of polypropylene bags is crucial to ensure that the final product meets the necessary performance standards. From the quality inspection of raw PP and PE granules to the rigorous testing of finished woven bags, every stage of production must be closely monitored to achieve the desired results. For manufacturers, maintaining high standards of quality not only ensures product reliability but also enhances their reputation in the marketplace.
For more information on polypropylene bags and their various applications, visit our detailed pages on Polypropylene Bags, Polypropylene Sacks, and PP Bags.