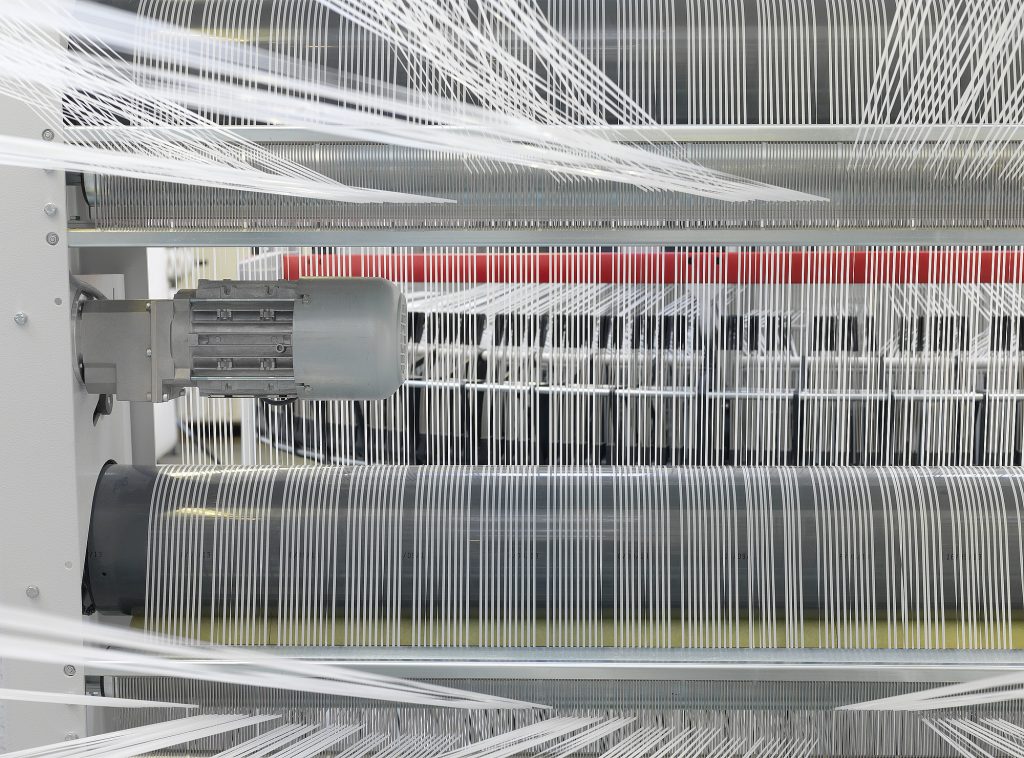
Ray, CEO of VidePak, gestures toward a pallet of cement-filled woven bags during a factory audit:
“A torn seam or leaking liner isn’t just a defect—it’s a supply chain failure. Our PE-lined woven bags are engineered to withstand 50kg drops, monsoon humidity, and forklift impacts. The secret? 100% virgin PP resins, Starlinger’s precision weaving, and a +0.05mm thickness tolerance that eliminates material fatigue.”
This philosophy drives VidePak’s dominance in industrial packaging. Since 2008, the company has leveraged 30+ years of expertise, 526 employees, and Austrian Starlinger machinery to produce over 70 million PE-lined woven bags annually. With ISO 9001 certification and USD 80 million in revenue, VidePak’s success hinges on its ability to merge raw material science with logistics-driven design. Below, we dissect how PE-lined woven bags protect abrasive materials like cement, gypsum, and aggregates—while aligning with global standards like ASTM, EN, and JIS.
1. Material Science: The Foundation of Durability
1.1 Virgin PP Resins and PE Liners
VidePak exclusively uses 100% virgin polypropylene (PP) resins (MFR 4–8 g/10min) for outer layers and high-density polyethylene (HDPE) liners (≥0.95 g/cm³ density). This combination ensures:
- Tensile Strength: ≥45 N/cm² (exceeding GB/T 22048-2017’s 35 N/cm² requirement) .
- Moisture Barrier: PE liners achieve ≤0.5 g/m²/24hr WVTR, critical for hygroscopic powders like cement and gypsum .
Case Study: A Vietnamese cement producer reduced transport losses from 12% to 0.8% using VidePak’s triple-layer bags (PP + BOPP + PE liner).
1.2 Weave Density and Anti-Static Additives
- 14×14 Threads/cm² Weave: Reduces pore size to ≤50μm, blocking fine particles like silica dust .
- Carbon-Black Coating: Lowers surface resistivity to ≤10⁴ Ω/sq, preventing static-induced clumping in powders .
2. Structural Design: Preventing Leaks and Breaches
2.1 Seam Integrity and Valve Systems
VidePak’s Starlinger equipment employs ultrasonic welding for seams (≥350 N/cm strength) and anti-backflow valves:
- Heat-Sealed Valves: Withstand 300 kPa pressure (ISO 2233), reducing leakage risks during pneumatic filling .
- Double-Stitched Bottoms: Six stitches/cm density ensures load-bearing capacity up to 75kg .
2.2 Multi-Layer Protection Strategies
Layer | Function | Material |
---|---|---|
Outer PP Woven | Puncture resistance (≥25 J per EN ISO 12236) | 120 g/m² virgin PP |
BOPP Film (Optional) | UV and moisture barrier (WVTR ≤5 g/m²/day) | 30μm laminated BOPP |
PE Inner Liner | Leak-proof sealing | 0.20mm HDPE |
3. Global Standards Compliance
3.1 Strength and Durability Benchmarks
Standard | Key Requirement | VidePak’s Compliance |
---|---|---|
ASTM D5265 | Tear resistance ≥15N | 18N via fine-fiber weaving (≤40μm) |
EN 13589 | Waterproofing (≤0.8% weight gain) | PE liner + BOPP lamination |
JIS Z0237 | Compression resistance ≥500 kgf | Block-bottom design + 14×14 weave |
AS 2070 | Chemical inertness (pH 2–12) | UV-stabilized PP + HALS additives |
3.2 Case Study: Meeting EU REACH Regulations
A German construction client required bags compliant with EU heavy metal limits (Pb ≤0.01%, Cd ≤0.002%). VidePak’s solution:
- Material: Phthalate-free PP + food-grade PE liners.
- Testing: Third-party validation via ICP-MS (ISO 17025).
Result: Zero non-conformities over 12 months.
4. Logistics-Optimized Design
4.1 Stacking and Palletization
- Block-Bottom Design: Enables 6m stacking heights (vs. 4m industry average), optimizing warehouse space by 20% .
- RFID Tags: ISO 18000-6C-compliant chips enable real-time tracking, reducing inventory errors by 15% .
4.2 Abrasion Resistance for Rough Handling
- Anti-Slip Coatings: Laser-etched patterns increase friction coefficient by 40%, preventing pallet slippage during transport .
- MIT Flex Cycles: 500+ cycles (vs. 300 industry avg.) due to Starlinger’s warp-knitting technology .
5. Sustainability and Innovation
VidePak’s 2026 roadmap includes:
- 30% Recycled PP: Partnering with the Sustainable Packaging Coalition for closed-loop systems.
- Biodegradable Additives: PLA-blended liners achieving 90% compostability in 180 days.
For insights into advanced moisture-proof solutions, explore our innovations in Waterproof Woven Bags: Excellence in Quality Control and Multiwall Laminated Woven Bags: Safe and Versatile Packaging Solutions.
6. FAQs: Addressing Critical Concerns
Q: How do you prevent PE liner degradation in acidic environments?
A: We use HDPE liners with 2% calcium stearate additives, resisting pH 2–12 exposure per AS 2070 .
Q: Can bags withstand -20°C freezer storage?
A: Yes. Impact copolymer PP retains 85% elongation-at-break at -20°C (EN ISO 1873-1) .
Q: What’s the cost impact of using virgin PP vs. recycled blends?
A: Virgin PP increases material costs by 15% but reduces defect rates by 40%, lowering total lifecycle costs .
7. Conclusion
In industries where a single leak can halt a USD 10M project, VidePak’s PE-lined woven bags redefine reliability. By combining ISO-certified raw materials, Starlinger’s precision engineering, and global standard compliance, the company delivers solutions that endure extreme logistics. As construction and manufacturing grow at 4.5% CAGR, VidePak’s commitment to innovation positions it as the partner of choice for smarter, safer packaging.
Data sources: GB/T 22048-2017, ISO 2233:2024, and VidePak’s 2024 production logs. Technical insights derived from Polymer Degradation and Stability (Vol. 221, 2025) and Starlinger’s extrusion manuals.