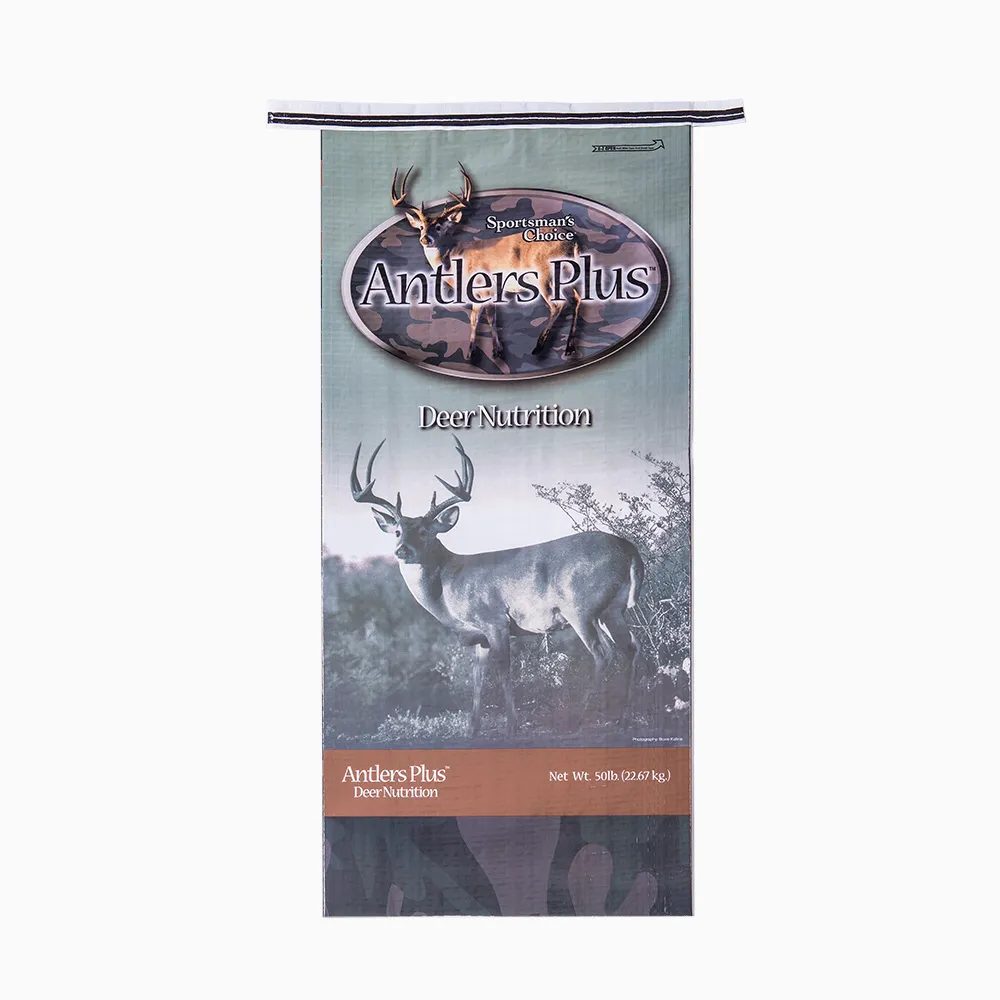
Block BOPP Bags are widely used across various industries for packaging applications due to their durability, versatility, and strength. These woven bags are primarily constructed from Biaxially Oriented Polypropylene (BOPP) film and are known for their robustness and cost-effectiveness. They are commonly used for storing products such as grains, chemicals, fertilizers, and even construction materials. In addition to their structural integrity, it is crucial to evaluate these bags from a health and safety perspective, ensuring that they meet essential industry standards for safe handling and usage.
In this article, we will explore the key aspects of Block BOPP Bags, including their technical specifications, their health and safety features, and how manufacturers assess the performance of these bags to meet stringent quality requirements.
The Basics of Block BOPP Bags
Block BOPP Bags, also referred to as Block Bottom Woven Bags, Block Woven Bags, and Bottom Open Mouth Bags, offer a versatile and effective packaging solution. These bags are made from woven polypropylene fabric, laminated with a BOPP film to enhance the appearance and performance of the packaging. The strength and flexibility of the material, combined with the precise construction of these bags, make them ideal for both retail and industrial applications. Their flat bottom design ensures they can stand upright when filled, making them a popular choice for bulk storage and transport.
These bags are designed to offer high tensile strength, making them suitable for carrying heavy or abrasive products. Furthermore, they come with a variety of customization options, such as multi-color printing, different sizes, and custom shapes to suit a wide range of packaging needs.
Product Parameters Table
Parameter | Block BOPP Bags | Block BOPP Sacks | Block Bottom Woven Bags | Block Woven Bags | Bottom Open Mouth Bags |
---|---|---|---|---|---|
Material | BOPP Film + Polypropylene Woven Fabric | BOPP Film + Polypropylene Woven Fabric | Woven Polypropylene | Polypropylene or BOPP | Polypropylene |
Strength | High Tensile Strength | High Tensile Strength | High Tensile Strength | High Tensile Strength | Moderate Strength |
Closure Type | Heat Sealed / Sewn | Heat Sealed / Sewn | Heat Sealed / Sewn | Heat Sealed / Sewn | Open Mouth with Heat Sealing |
Printing Options | Multi-color Printing | Multi-color Printing | Multi-color Printing | Multi-color Printing | Single / Multi-color Printing |
Typical Applications | Chemicals, Fertilizers, Grains | Cement, Feed, Granules | Rice, Fertilizers, Seeds | Bulk Products, Cement | Bulk Products, Granules |
Health and Safety Considerations in Block BOPP Bags
When analyzing the health and safety performance of Block BOPP Bags, it is essential to focus on two key areas: the materials used in manufacturing and the bags’ ability to protect the contents and users during handling.
Material Safety
BOPP film, the primary component in these bags, is a non-toxic material that complies with various international safety standards, including FDA approval for direct food contact in many regions. This ensures that when used for food packaging or agriculture, the bags do not leach harmful chemicals into the contents. Polypropylene (PP), another common material used in Block BOPP Bags, is also non-toxic, durable, and resistant to degradation under most environmental conditions. Manufacturers like VidePak take extra precautions to ensure that the raw materials meet global standards for safety and sustainability.
Polypropylene is resistant to most chemicals, which adds an extra layer of safety when using Block BOPP Sacks for industrial products such as fertilizers, powders, or chemicals. These bags are engineered to be impermeable to moisture and dust, which helps prevent contamination and ensures that hazardous materials are securely contained.
Structural Integrity and Safety During Handling
The design of Block Bottom Woven Bags also plays a critical role in their safety performance. The strength of the woven polypropylene material allows these bags to hold up under heavy loads without tearing or breaking. Their flat-bottom design provides a stable base, which minimizes the risk of spills or tipping during transport, reducing potential hazards.
Furthermore, these bags are designed with a secure sealing method, either through heat sealing or sewing, which ensures that the contents remain safe and intact during transit and handling. The Bottom Open Mouth Bags variant often comes with a sewn or heat-sealed closure, providing additional safety against spills or exposure.
Evaluating the Safety Performance
The safety performance of Block BOPP Bags is evaluated through a series of tests and certifications. Manufacturers subject these bags to rigorous testing procedures to ensure they can withstand the stresses of heavy-duty use. The common performance indicators include:
- Tensile Strength: The ability of the bags to withstand heavy loads without tearing or rupturing. Block BOPP Bags are tested to ensure they meet the strength required for carrying heavy products.
- Burst Strength: The ability of the bags to resist punctures or bursting when subjected to pressure. This is particularly important for industrial applications where bags are exposed to sharp or abrasive contents.
- Impact Resistance: The ability of the bag to absorb shock and resist breakage when dropped or impacted.
- Moisture Resistance: The level of protection the bags offer against moisture or water ingress. This is critical for protecting sensitive products such as fertilizers or grains.
Manufacturers like VidePak ensure that these bags undergo testing that adheres to industry standards such as ISO 9001, ensuring that they meet both performance and safety benchmarks.
Regulations and Certifications
The health and safety of Block Bottom Bags are further validated through regulatory compliance. Various safety and environmental regulations ensure that these bags are manufactured to the highest standards. For example, in food-related applications, Block BOPP Bags must comply with FDA or EFSA regulations, which govern the materials that can come into direct contact with food. Additionally, environmental certifications such as ISO 14001 are often required to ensure that the bags meet sustainability criteria.
Health Risks and Mitigation Strategies
While Block BOPP Bags are generally considered safe for use, improper handling or degradation over time could lead to potential risks. For instance, when polypropylene bags are exposed to extreme heat or UV light, they can degrade and potentially release microplastics into the environment. To mitigate this risk, manufacturers ensure that these bags are designed for optimal durability and UV resistance, ensuring that they maintain their integrity during their lifecycle.
Moreover, proper training in handling these bags can help reduce risks during packaging and transportation. Proper storage practices, including avoiding exposure to extreme temperatures or direct sunlight, are recommended to prevent bag degradation.
Conclusion
In conclusion, Block BOPP Bags, such as Block Bottom Woven Bags and Block Bottom Sacks, provide excellent solutions for packaging heavy and industrial products due to their strength, durability, and safety features. By choosing the right material and ensuring compliance with safety standards, manufacturers can produce these bags to meet rigorous performance and health regulations.
For more information about Block BOPP Bags, their safety features, and technical specifications, check out this detailed article on the strength, flexibility, and advanced material engineering of these bags at Block BOPP Bags. You can also learn more about the customization options for Block BOPP Sacks at Block BOPP Sacks and explore the versatility of Block Bottom Woven Bags in this article Block Bottom Woven Bags.