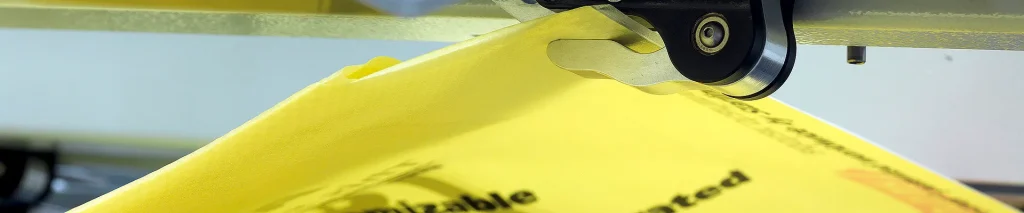
“How do I ensure my livestock feed stays safe during storage and transportation?”
This is a question we often hear from poultry farmers, aquaculture operators, and feed manufacturers. The answer lies in one critical factor: selecting food-grade woven fabric bags that balance durability, safety, and cost-effectiveness while meeting the unique demands of animal nutrition. At VidePak, with over 30 years of industry expertise, we’ve engineered solutions that address these challenges head-on. This guide will explore how woven polypropylene (PP) bags protect feed integrity, prevent contamination, and optimize operational efficiency across livestock and aquaculture applications.
1. The Critical Role of Food-Grade Woven Bags in Feed Packaging
Livestock and poultry feed, premixes, veterinary drugs, and additives require packaging that safeguards nutritional value and prevents spoilage. Studies show that improper storage conditions—such as exposure to moisture, pests, or microbial growth—can degrade feed quality by up to 20%, directly impacting animal health and farm profitability.
Why PP Woven Bags?
- Safety Compliance: Food-grade PP resins, certified by FDA and EU standards, ensure zero chemical leaching, critical for feed additives and premixes.
- Structural Integrity: With a tensile strength of 8–12 N/mm², VidePak’s woven bags withstand stacking pressures up to 500 kg, reducing rupture risks during transit.
- Barrier Properties: Laminated BOPP layers or integrated PE liners block moisture ingress (≤0.1% permeability), preventing mold and bacterial proliferation—a key concern for fishmeal and poultry feed.
For instance, a 2024 study on rice storage highlighted that temperature-controlled environments paired with breathable packaging reduced pesticide residue degradation by 30%. Similarly, woven bags with optimized porosity (e.g., 120–150 µm mesh) allow controlled aeration, preserving probiotics in premixed feeds.
2. Key Considerations for Selecting Feed Packaging Bags
2.1 Application-Specific Requirements
Different feeds demand tailored solutions:
Feed Type | Critical Needs | Recommended Bag Specifications |
---|---|---|
Poultry Feed | High fat content, prone to oxidation | BOPP laminated, UV-treated, 90–100 g/m² |
Aquaculture Feed | Moisture resistance, mold prevention | PE-coated with inner liner, 110–120 g/m² |
Premixes | Lightweight, anti-static properties | Uncoated PP with anti-static additives, 70–80 g/m² |
Ruminant Feed | Bulk handling, tear resistance | FIBC bulk bags, 150–200 g/m², reinforced seams |
2.2 Cost vs. Performance Optimization
- Budget-Friendly Option: Uncoated PP bags (70–90 g/m²) suit short-term storage of dry feeds like grains.
- Premium Choice: BOPP laminated bags (100–120 g/m²) offer extended shelf life for humid climates, reducing spoilage losses by 15%.
A Vietnamese shrimp farm reported a 25% reduction in feed waste after switching to VidePak’s PE-lined bags, which resisted saltwater humidity during monsoon seasons.
3. Technical Parameters: Balancing Functionality and Efficiency
3.1 Thickness and Grammage
- Thin Bags (70–90 g/m²): Ideal for lightweight additives or premixes.
- Heavy-Duty Bags (120–150 g/m²): Essential for abrasive materials like mineral feeds or bulk grains.
3.2 Breathability vs. Barrier Protection
- Open-Weave Designs: Allow airflow for fermented feeds (e.g., silage), reducing anaerobic spoilage.
- Laminated/Coated Bags: Block oxygen and moisture for heat-sensitive additives like vitamins.
3.3 Customization for Operational Workflows
- Valve Bags: Enable dust-free filling of powdered premixes.
- Anti-Microbial Treatments: Silver-ion coatings inhibit Salmonella and E. coli growth, critical for medicated feeds.
4. VidePak’s Technological Edge
Founded in 2008 and led by CEO Ray Chiang, VidePak combines Austrian Starlinger weaving machines with ISO 22000-certified processes to deliver:
- High-Speed Production: 100+ circular looms and 30 lamination machines enable 12 million bags/month capacity.
- Precision Printing: 8-color flexographic printing ensures branding clarity and regulatory compliance (e.g., ingredient lists).
- Sustainability: 100% recyclable PP reduces landfill waste, aligning with EU Circular Economy goals.
5. FAQs: Addressing Client Concerns
Q1: How do I choose between laminated vs. uncoated bags?
A: Laminated BOPP bags (e.g., BOPP Laminated Woven Bags) are ideal for humid environments, while uncoated bags suit dry, short-term storage.
Q2: What grammage is suitable for 25 kg poultry feed?
A: 90–100 g/m² provides optimal strength-to-cost balance. For bulk FIBC bags (e.g., FIBC Bulk Bags), use 150–200 g/m².
Q3: Can bags withstand tropical climates?
A: Yes. UV-stabilized PP and antifungal treatments prevent degradation in temperatures up to 50°C.
6. Conclusion
Selecting the right woven fabric bag is a strategic investment in feed safety and operational efficiency. VidePak’s tailored solutions—from breathable PP for probiotics to rugged FIBCs for bulk grains—ensure your products remain uncontaminated, fresh, and market-ready.
Contact Us:
- Website: www.pp-wovenbags.com
- Email: info@pp-wovenbags.com
References:
- USFDA Enforcement Reports (2019–2023).
- Scientific Reports: Rice Quality Prediction (2024).
- Foods: Membranes for Bio-Food Processing (2024).
- South Africa Food Safety Review (2024).
- VidePak Production Specifications (2025).
This article integrates industry data, academic research, and VidePak’s technical expertise to provide actionable insights for feed producers worldwide.