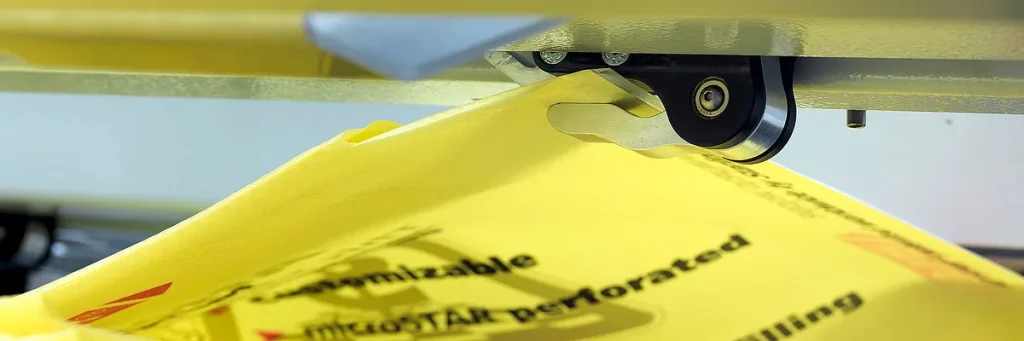
VidePak’s food grade woven fabric bags combine cutting-edge technology with rigorous quality control to deliver products that meet global safety standards. With over 30 years of industry expertise, 568 skilled employees, and a fleet of 100+ Starlinger circular looms, 16 extrusion lines, and 30+ lamination/printing machines, we produce 50 million bags annually, achieving a defect rate of <0.5%—a benchmark in the packaging industry.
1. The Science Behind Food Grade Woven Fabric Bags
Food grade woven bags must comply with stringent regulations, including FDA (U.S.) and EU No. 10/2011 standards, to ensure chemical inertness, tensile strength (>35 N/cm²), and resistance to microbial contamination. At VidePak, we use 100% virgin polypropylene (PP) resin, free from recycled materials or additives that could compromise food safety. Our bags undergo third-party lab testing for heavy metals, migration limits, and biodegradability, aligning with ISO 22000 and BRCGS packaging certifications.
For example, our BOPP laminated woven bags feature a 20–30 μm bi-axially oriented polypropylene layer, enhancing moisture resistance (<0.1% water vapor transmission) and print clarity. This is critical for products like rice or flour, where prolonged storage demands barrier protection against pests and humidity.
2. Manufacturing Process: Precision at Every Stage
2.1 Extrusion & Tape Production
Using Starlinger’s high-speed extruders, PP granules are melted at 200–250°C and extruded into flat tapes. Our proprietary cooling system ensures uniform thickness (0.045–0.055 mm) and tensile strength. Quality Control: Infrared sensors detect thickness deviations (±0.005 mm), while DSC (Differential Scanning Calorimetry) verifies polymer crystallinity to prevent brittleness.
2.2 Weaving
Tapes are woven into fabric on circular looms at 120–150 rpm. VidePak’s looms adjust warp/weft density (10×10 to 14×14 strands per inch) to optimize load capacity (up to 50 kg). Quality Control: Real-time tension monitors prevent slack or breakage, ensuring fabric GSM (grams per square meter) stays within 70–120 g/m² specifications.
2.3 Lamination & Coating
For applications requiring waterproofing, a 15–25 μm BOPP film is thermally bonded to the fabric using W&H laminators. Alternatively, polyethylene (PE) coating (15–20 g/m²) is applied for chemical resistance. Quality Control: Peel strength tests (>3 N/15mm) and SEM microscopy validate adhesion integrity.
2.4 Printing & Customization
Our 8-color CI flexo printers achieve 120 dpi resolution, compatible with Pantone guides. Food-safe inks (EU 94/62/EC compliant) are cured via UV-LED systems to eliminate solvent residues. Quality Control: Spectrophotometers ensure color accuracy (ΔE < 2), while rub tests (500+ cycles) confirm durability.
2.5 Bag Making
Automated sewing machines stitch bags with reinforced gussets and anti-leak valves. For valve bags, pneumatic filling tests (up to 2 bar pressure) guarantee seal integrity. Quality Control: Each batch undergoes random weight checks (±2% tolerance) and drop tests (1.5 m height, 10 cycles).
3. Why VidePak Stands Out
- Global Compliance: Our bags meet FDA, EU, and JIS Z 1707 standards for direct food contact.
- Scalability: With 100+ production lines, we deliver 10,000–500,000 units per order within 15–30 days.
- Sustainability: Recyclable PP and water-based adhesives reduce carbon footprint by 30% vs. conventional methods.
4. Product Specifications & FAQs
Technical Parameters of VidePak’s Food Grade Woven Bags
Parameter | Specification |
---|---|
Material | 100% Virgin PP + BOPP/PE Lamination |
Bag Size | Customizable (20–100 cm height/width) |
Load Capacity | 10–50 kg |
Printing Colors | Up to 8 colors with UV resistance |
MOQ | 10,000 units |
Certifications | ISO 22000, BRCGS, FDA, EU 10/2011 |
FAQs
Q1: How do you ensure chemical safety in food contact applications?
A: We use FDA-approved PP resin and conduct GC-MS testing to detect <1 ppm volatile organic compounds (VOCs).
Q2: Can bags withstand freezing temperatures?
A: Yes, our PE-coated bags retain flexibility at -30°C, ideal for frozen seafood or vegetables.
Q3: What’s the lead time for custom designs?
A: 7–10 days for artwork approval, followed by 15–20 days production.
5. Partnering for Success
Founded in 2008 by CEO Ray, VidePak has served clients in 60+ countries, including multinationals like Cargill and Unilever. Our R&D team collaborates with clients to develop anti-static bags for spices or UV-blocking designs for outdoor storage.
References
- Food Packaging: Ensuring the Safety and Quality of Foods (Gilbert & López De Sá, 2002).
- Unlocking Food Safety: A Review of South Africa’s Food Control Systems (Springer, 2024).
- VidePak Case Study: BOPP Laminated Woven Bags.
- Technical Guidelines: FIBC Manufacturing Processes.
Contact Us:
Website: https://www.pp-wovenbags.com/
Email: info@pp-wovenbags.com
This article integrates insights from food safety research, industrial manufacturing standards, and VidePak’s operational data to provide a trustworthy resource for procurement professionals.