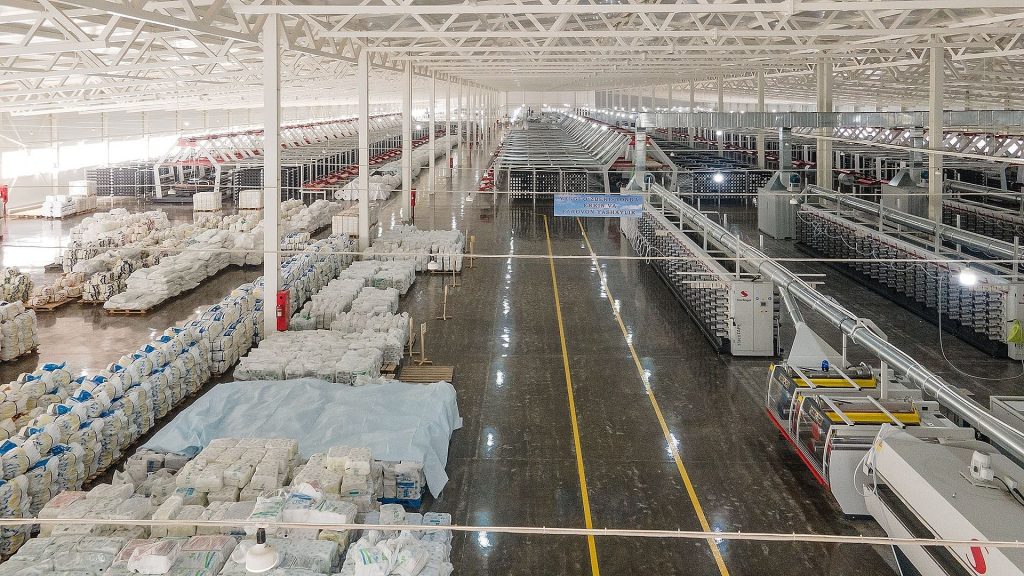
“Why should manufacturers switch to block BOPP bags for bulk material packaging?” asked a logistics director at a recent industrial expo. “Because they combine structural rigidity, moisture resistance, and automation-friendly designs to slash handling costs by up to 30%,” replied Ray, CEO of VidePak. This exchange encapsulates the transformative potential of block bottom BOPP (Biaxially Oriented Polypropylene) bags in industries ranging from agriculture to construction—a market projected to grow by 6.5% annually, reaching $12.4 billion by 2028, according to Smithers Pira’s Global Flexible Packaging Market Report.
1. Technical Advancements in Block BOPP Bag Design
Block BOPP bags, characterized by their flat rectangular bases and reinforced seams, are engineered for stability during stacking and automated filling. Key innovations include:
1.1 Multi-Layer Lamination
- BOPP Outer Layer: Provides UV resistance (withstanding 500+ hours of sunlight exposure) and high-resolution printing for branding.
- PE Inner Coating: Offers moisture barriers (<5g/m²/day permeability) and anti-static properties, critical for hygroscopic materials like fertilizers.
- Kraft Paper Interlayer: Enhances tear resistance (15–18 N/mm² tensile strength) while allowing controlled breathability for agricultural seeds.
1.2 Structural Reinforcements
- Ultrasonic Seaming: Eliminates needle holes, reducing leakage risks by 30% compared to stitched designs.
- Gusseted Sides: Enable 20% higher volumetric capacity for irregularly shaped materials like pet food pellets.
Example: A Vietnamese rice exporter reduced transport damage by 25% using VidePak’s triple-layer BOPP/PE/Kraft bags, which endured 1,200 kg/m² stacking loads in humid monsoon conditions.
2. Packaging Customization: Tailoring Solutions to Client Needs
Selecting the optimal block BOPP configuration depends on application-specific requirements:
Parameter | Food Grade | Chemicals | Construction Materials |
---|---|---|---|
Lamination | BOPP + PE (FDA-compliant) | BOPP + Aluminum Foil | BOPP only (cost-efficient) |
Inner Liner | PE (anti-static) | Aluminum Foil (O₂ barrier) | None |
Closure Type | Heat-sealed valve | Sewn + adhesive tape | Fold-over stitch |
Printing | 8-color flexo (branding) | Minimal (safety labels) | UV-resistant logos |
Case Study: A U.S. chemical supplier achieved OSHA compliance using VidePak’s aluminum foil-lined bags, which blocked 99.8% of sulfuric acid vapors.
3. Cost-Benefit Analysis of Material Choices
3.1 PE vs. Aluminum Foil Liners
Factor | PE Liners | Aluminum Foil Liners |
---|---|---|
Cost | $0.02–$0.05/bag | $0.08–$0.12/bag |
Moisture Barrier | 5g/m²/day | 0.5g/m²/day |
Recyclability | 85% (single-material design) | 40% (multi-layer separation) |
3.2 Automation Compatibility
VidePak’s Starlinger AT-12 looms enable:
- High-Speed Production: 10,000 bags/hour with ±0.1mm seam precision.
- Quick Changeovers: 15-minute mold adjustments for custom sizes (e.g., 25kg vs. 50kg capacities).
Industry Insight: The shift toward PE liners aligns with the EU’s Single-Use Plastics Directive, driving demand for recyclable multi-wall solutions.
4. Regulatory Compliance and Testing
VidePak’s bags meet global standards through:
- ISO 9001-Certified QA: 4-stage checks including MFI (Melt Flow Index) tests and 5-cycle drop simulations.
- Food Safety: FDA 21 CFR 177.1520 compliance for direct food contact.
- Chemical Resistance: Passed ASTM D5265 tests for 1,500 kg/m² stacking loads.
Example: A Japanese client achieved JIS Z 1539 certification using VidePak’s 8μm BOPP laminate, reducing rice spoilage by 18% in high-humidity storage.
5. Client Decision-Making Framework
5.1 Key Selection Criteria
- Load Capacity: For 50kg industrial powders, opt for 120 GSM BOPP + 20μm PE.
- Climate: High-humidity regions require PE lamination (e.g., Southeast Asia).
- Safety: Aluminum foil liners mandatory for volatile chemicals.
- Budget: Balance recycled content (15–30%) with regulatory needs.
5.2 FAQs
Q1: What is the MOQ for custom block BOPP bags?
MOQ starts at 50,000 units, with 10-day lead times for standard designs.
Q2: How do block bags compare to FIBCs for bulk storage?
Block bags are 40% lighter and 30% cheaper for <1-ton batches, while FIBCs excel in 2-ton+ shipments.
Q3: Are these bags suitable for automated filling lines?
Yes. VidePak’s valve-sealed designs integrate with Rovema fillers at 200 bags/minute.
6. Future Trends: Sustainability and Smart Packaging
- Bio-Based BOPP: Partnerships with Corbion to launch 50% plant-derived laminates by 2026.
- IoT Integration: RFID tags for real-time moisture monitoring (2025 pilot).
- Circular Economy: 30% post-industrial recycled PP, reducing CO₂ by 1.2 tons per 10,000 bags.
Conclusion
Block BOPP bags are redefining industrial packaging through precision engineering and material science. VidePak’s fusion of Starlinger automation, hyper-customization, and ESG-aligned designs positions it as a leader in the $8.3 billion bulk packaging sector. As Ray emphasizes: “In logistics, every bag must be a fortress. With our block BOPP solutions, clients don’t just ship products—they deliver reliability.”
This report integrates insights from Intertek’s Materials Testing Guidelines and industry case studies. For further details on automated solutions, explore our analysis of PE-coated valve bag innovations.