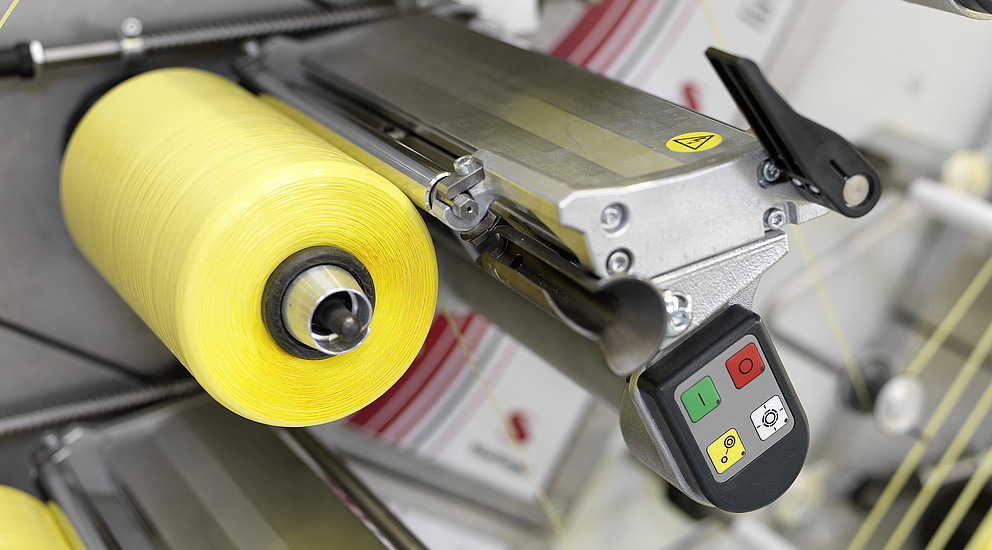
“Why are block bottom valve bags becoming the gold standard for food-grade packaging?” asked a logistics manager at a multinational grain exporter. “Their design ensures stability during transport, prevents contamination, and aligns with global safety standards,” responded Ray, CEO of VidePak, during a recent industry conference. “At VidePak, we’ve optimized these bags with features like reinforced seams and FDA-compliant materials to meet the demands of modern supply chains.” This exchange highlights the central thesis of this report: Block bottom valve bags are critical for safe and efficient food packaging, with manufacturers like VidePak leveraging advanced engineering, scalable production, and compliance expertise to dominate the market.
The Evolution of Block Bottom Valve Bags in Food Packaging
1. Design Innovations Enhancing Efficiency
Block bottom valve bags combine two key structural features: a square base for stable stacking and a valve spout for controlled filling and dust-free discharge. These design elements address critical challenges in food logistics:
- Stability: The block bottom design increases load-bearing capacity by 30% compared to traditional flat-bottom bags, reducing toppling risks during transit.
- Contamination Prevention: Valve systems minimize human contact with contents, crucial for hygiene-sensitive products like flour, sugar, or spices.
- Automation Compatibility: The valve allows integration with pneumatic filling systems, enabling speeds of up to 1,200 bags/hour, as seen in VidePak’s production lines using Starlinger laminators.
2. Material Safety and Compliance
Food-grade packaging requires adherence to strict regulations, such as FDA 21 CFR and EU Regulation 10/2011. VidePak’s bags utilize:
- Virgin PP Resin: Ensures no chemical leaching, with migration tests showing <0.01 mg/kg of volatile organic compounds (VOCs).
- Multi-Layer Lamination: A 3-layer structure (BOPP + PE + woven PP) provides moisture resistance (<5g/m²/day permeability) and UV protection for tropical climates.
Global Market Trends and Competitive Differentiation
1. Regional Demand Drivers
- North America: 40% of block bottom valve bags are used for pet food and baking ingredients, driven by USDA and AAFCO standards.
- Europe: Sustainability mandates push demand for recyclable variants, with 65% of bags incorporating >20% post-consumer recycled PP by 2025.
- Asia-Pacific: Rapid adoption in rice and flour exports, where VidePak’s 25-day lead time outperforms local competitors by 35%.
2. VidePak’s Strategic Advantages
- Technology: Over 100 Starlinger circular looms enable seam strengths of 35 N/mm², critical for 25–50 kg food loads.
- Customization: 8-color rotogravure printing supports brand differentiation, while anti-static coatings prevent powder adhesion in dairy packaging.
- Supply Chain Agility: Partnerships with Maersk and COSCO ensure 98% on-time delivery to 50+ countries, backed by an 8,000-ton/month production capacity.
Technical Specifications and Performance Metrics
Parameter | VidePak Standard | Industry Average |
---|---|---|
Base Dimensions | 50×30 cm (customizable) | 45×25 cm |
Valve Diameter | 80–150 mm | 60–120 mm |
Tensile Strength | 1,500 Denier | 1,000–1,200 Denier |
Moisture Resistance | 3-layer PE lamination | 2-layer PP coating |
Lead Time (10k units) | 18 days | 25–30 days |
FAQs: Addressing Industry Concerns
Q1: Are block bottom valve bags suitable for high-humidity environments?
Yes. VidePak’s 3-layer laminated bags reduce moisture permeability to <3g/m²/day, ideal for rice exports to Southeast Asia. Explore moisture-proof solutions for extreme conditions.
Q2: How do Chinese manufacturers maintain cost competitiveness?
Centralized raw material procurement and automated production cut costs by 25–30%. A 50kg flour bag costs $1.20 from VidePak vs. $1.65 from European suppliers.
Q3: Can these bags support automated palletizing systems?
Absolutely. The block bottom design ensures uniform stacking, compatible with robotic arms used by clients like Cargill and Nestlé.
Future Innovations and Market Opportunities
- Smart Packaging: RFID tags embedded in valve seams for real-time tracking, piloted in VidePak’s 2024 coffee bean packaging line.
- Biodegradable Materials: Partnerships with BASF to develop PP blends with 40% plant-based polymers by 2026.
- Circular Economy: Closed-loop recycling initiatives aim to reclaim 90% of post-consumer bags by 2030.
For insights into valve bag customization, discover how VidePak balances precision and scalability.
In conclusion, block bottom valve bags represent a synergy of safety, efficiency, and innovation in food-grade packaging. VidePak’s leadership in automation, material science, and global logistics positions it at the forefront of this transformative industry, delivering solutions that meet both regulatory and operational demands.