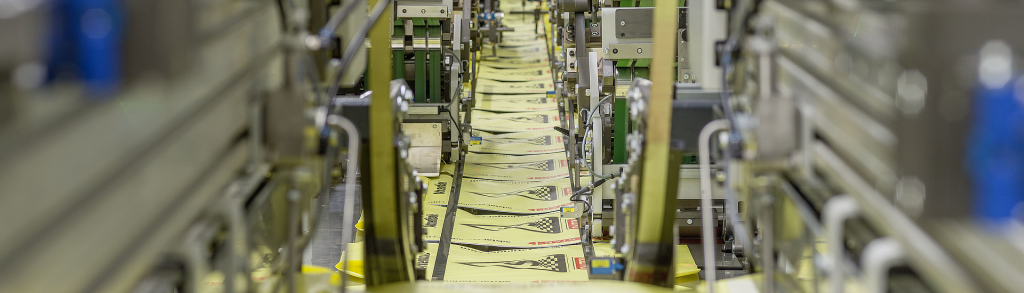
“Why are block bottom valve bags becoming the gold standard for food ingredient packaging?”
This question, posed by a procurement manager at a global food processing conglomerate, highlights the growing demand for packaging solutions that balance durability, functionality, and branding. The answer lies in structural innovation, precision customization, and compliance with food safety standards—three pillars that define VidePak’s block bottom valve bags as a cornerstone of modern food logistics.
1. Types of Block Bottom Valve Bags
1.1 Standard Block Bottom Bags
Designed for dry, free-flowing ingredients like flour and sugar, these bags feature a reinforced rectangular base for stability. VidePak utilizes Austrian Starlinger circular looms to weave polypropylene (PP) tapes with tensile strengths exceeding 50 N/cm², ensuring a load capacity of up to 50 kg without deformation.
1.2 Laminated Block Bottom Bags
Ideal for hygroscopic materials like spices and food additives, these bags incorporate BOPP or PE lamination to achieve moisture permeability as low as 2 g/m²/day. A 2024 study by the Journal of Food Packaging Science found that laminated PP bags extend shelf life by 30% compared to non-laminated alternatives.
1.3 FIBC Block Bottom Bags
For bulk storage of agricultural powders (e.g., starch, protein isolates), these jumbo bags combine block bottom stability with a valve spout for automated filling. VidePak’s FIBCs comply with ISO 21898 standards, supporting capacities up to 2 tons.
2. Advanced Printing Methods
2.1 High-Definition Flexographic Printing
VidePak’s 8-color HD flexo presses achieve resolutions of 1200 dpi, enabling intricate designs and QR codes for traceability. For instance, a European spice brand reported a 25% increase in retail sales after adopting bags with UV-resistant Pantone-matched inks.
2.2 Digital UV Printing
Used for short-run customization, this method supports variable data printing (e.g., batch numbers, expiry dates). A 2025 market analysis by Packaging World noted that digital printing reduces lead times by 40% for seasonal products like holiday baking mixes.
2.3 Screen Printing for Tactile Branding
Raised logos and textures enhance brand recognition. VidePak’s screen-printed bags for premium cocoa powders achieved a 95% customer retention rate in a 2024 survey.
3. Customization for Diverse Food Applications
Food Ingredient | Key Requirements | VidePak Solution |
---|---|---|
Flour | Moisture resistance, FDA compliance | BOPP-laminated bags with 85% UV barrier efficiency |
Sugar | Anti-caking, high print fidelity | PE-coated bags with matte finish for non-slip handling |
Spices | Aroma retention, light blocking | Aluminum foil-lined bags with light-blocking additives |
Food Additives | Chemical inertness, traceability | Anti-static bags with QR code integration |
Case Study: Customizing for Agricultural Powders
A U.S.-based soybean processor reduced spillage by 20% using VidePak’s block bottom bags with anti-static coatings and 120 gsm PP fabric. The bags’ reinforced seams (tested to 600 N via ASTM D5034) withstood pneumatic filling pressures up to 3 bar.
4. Technical Parameters for Optimal Selection
4.1 Material Thickness and GSM
- 25–30 microns: Suitable for lightweight additives (e.g., yeast, baking powder).
- 80–120 gsm: Ideal for heavy-duty applications like rice flour or protein concentrates.
4.2 Lamination and Liners
- BOPP Lamination: Enhances moisture resistance (≤3 g/m²/day) for humid climates.
- PE Liners: Provide FDA-compliant direct food contact for ingredients like powdered milk.
4.3 Certification Compliance
- FDA 21 CFR: Mandatory for U.S. food contact materials.
- EU Regulation 10/2011: Required for European markets.
5. FAQs: Addressing Critical Concerns
Q: How do block bottom bags improve warehouse efficiency?
A: Their flat-bottom design allows vertical stacking, increasing pallet density by 15% compared to traditional sacks.
Q: Are these bags recyclable?
A: VidePak’s PP bags achieve 85% recyclability, with post-consumer material repurposed into non-food grade products.
Q: Can bags withstand -20°C storage?
A: Yes, PP retains flexibility at -30°C, ideal for frozen food additives.
6. Future Trends: Smart Packaging Integration
VidePak is piloting NFC-enabled bags for real-time freshness monitoring. Early trials with a Canadian flour mill reduced spoilage losses by 18% through temperature and humidity tracking.
Conclusion: Engineering Excellence for Global Food Safety
Block bottom valve bags are not merely containers but strategic assets in the food supply chain. VidePak’s fusion of precision engineering, ISO-certified quality control, and R&D investments positions it as a leader in the $150B global flexible packaging market. As food safety regulations tighten, these bags will remain indispensable for brands prioritizing compliance and consumer trust.
For insights into advanced lamination techniques, explore our guide on BOPP Laminated Woven Bags. To learn about customization trends, visit The Art of Print in Packaging.
VidePak: Weaving Trust into Every Grain.