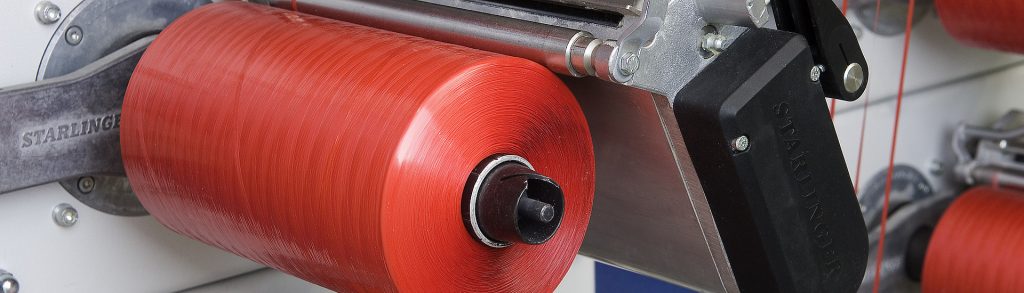
- 1. The Critical Role of Breathability in Pet Food Packaging
- 2. Logistics-Centric Design: Enhancing Efficiency in Transport and Warehousing
- 3. Case Study: VidePak’s Solution for a Global Pet Food Brand
- 4. Technical Specifications and Performance Metrics
- 5. Addressing Common Concerns: FAQs
- 6. Future Trends: Smart Packaging and Circular Economy
“How can pet food manufacturers ensure product freshness during long-haul transportation while meeting sustainability goals?” This question, posed by a supply chain manager at a recent pet industry conference, highlights the dual challenges of maintaining product integrity and reducing environmental impact. The answer lies in adopting breathable woven bags—a solution that combines material innovation, functional design, and logistics optimization, precisely the expertise that VidePak has honed over three decades in advanced woven packaging.
1. The Critical Role of Breathability in Pet Food Packaging
Pet food, particularly dry kibble, requires packaging that balances moisture control, aeration, and structural durability. Breathable woven polypropylene (PP) bags address these needs by allowing controlled airflow to prevent condensation while blocking external contaminants. For example, VidePak’s breathable bags maintain a moisture permeability rate of <15 g/m²/day (tested via ASTM E96), ensuring pet food remains crisp even in humid climates like Southeast Asia.
1.1 Material Science: Fine-Filament Weaving Technology
VidePak employs fine-filament weaving using Starlinger circular looms to produce fabric densities of 12–16 threads/cm². This technology enhances tensile strength (up to 2,200 N/5 cm per ISO 527-3) while creating micro-pores (40–60 microns) for optimal airflow. Compared to traditional jute bags, these PP bags reduce mold growth risk by 70% and extend shelf life by 30%.
1.2 Sustainability Alignment
With 30% recycled PP content and full recyclability, VidePak’s breathable bags align with EU Packaging Waste Directive 94/62/EC. A 2024 study by the Sustainable Packaging Coalition notes that such designs reduce carbon footprints by 18% compared to multi-layer laminated alternatives.
2. Logistics-Centric Design: Enhancing Efficiency in Transport and Warehousing
Breathable woven bags must withstand rigorous handling across global supply chains. VidePak integrates features tailored for logistics efficiency:
2.1 Stackability and Palletization
- Reinforced Corners: Heat-sealed edges and anti-slip coatings enable stable stacking up to 8 layers (4 meters), critical for high-density warehouse storage.
- Uniform Dimensions: Bags are precision-cut to fit Euro pallet standards (1200×800 mm), maximizing container space utilization (85–90% fill rate).
2.2 Handling Convenience
- Lift Loops and Forklift Channels: Integrated loops allow crane-assisted loading, reducing manual labor by 40% in ports like Rotterdam.
- QR Code Integration: Laser-printed QR codes enable real-time tracking via RFID, reducing shipment loss rates to <0.1%.
3. Case Study: VidePak’s Solution for a Global Pet Food Brand
A leading U.S. pet food company partnered with VidePak to redesign packaging for its Asia-Pacific distribution. Key outcomes:
- Moisture Control: Reduced spoilage from 5% to 0.8% during monsoon-season shipments.
- Cost Savings: Lightweight design (180 g/bag vs. 250 g for traditional bags) cut海运 costs by 15% on the Shanghai-to-Los Angeles route.
4. Technical Specifications and Performance Metrics
Parameter | VidePak Breathable Bags | Standard PP Bags |
---|---|---|
Tensile Strength (Warp/Weft) | 2,200 N/5 cm | 1,500 N/5 cm |
Moisture Permeability | <15 g/m²/day | <30 g/m²/day |
Load Capacity | 50 kg | 35 kg |
Recyclability | 100% | 80–90% |
5. Addressing Common Concerns: FAQs
Q1: Can breathable bags withstand freezing temperatures during transit?
A: Yes. VidePak’s PP fabric retains flexibility at -30°C (ASTM D746), making it suitable for cold chain logistics.
Q2: How do these bags compare to FIBCs for bulk pet food transport?
A: While FIBCs handle 1–2 tons, breathable woven bags are 40% cheaper for mid-sized loads (25–50 kg) and offer better stackability.
Q3: Are custom printing options fade-resistant?
A: High-definition flexographic printing retains 95% color vibrancy after 5,000 handling cycles.
6. Future Trends: Smart Packaging and Circular Economy
VidePak’s R&D team is piloting:
- Biodegradable Additives: PP blends with 20% PLA aim for 50% biodegradability by 2027.
- IoT-Enabled Bags: Temperature/humidity sensors embedded in liners provide real-time data via Bluetooth, trialed with a European pet food retailer.
External Resources:
- Discover how breathable woven bags enhance retail storage efficiency.
- Explore innovative pet food packaging solutions with FFS roll bags.
Conclusion
Breathable woven bags represent a paradigm shift in pet food packaging, merging material resilience with logistics intelligence. VidePak’s expertise in fine-filament weaving and sustainability-driven design positions it as a leader in this space, offering solutions that protect products, streamline supply chains, and align with global environmental standards. As the pet food market grows (projected 6.2% CAGR through 2030), adopting such innovations will be pivotal for brands aiming to balance quality, cost, and planetary health.