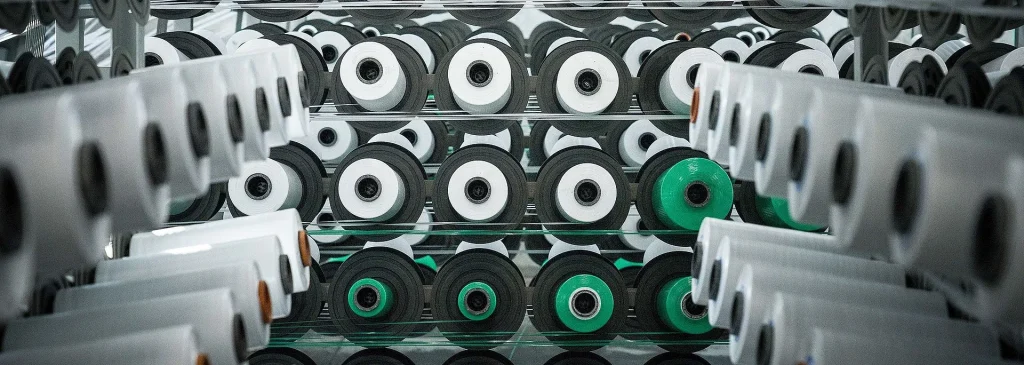
Imagine a packaging solution that ensures freshness, prevents spoilage, and aligns with global safety standards—all while being cost-effective. How do breathable woven bags achieve this? The answer lies in their unique structure, material adaptability, and advanced manufacturing techniques, which allow controlled airflow while maintaining product integrity. For food manufacturers and distributors, selecting the right packaging is not just about containment—it’s about preserving quality, complying with regulations, and meeting consumer expectations.
At VidePak, a global leader in woven bag production since 2008, we combine 30+ years of industry expertise with cutting-edge technology to deliver solutions that address these critical needs. Let’s dive into how breathable woven bags revolutionize food packaging and how to choose the optimal configuration for your application.
1. The Science Behind Breathable Woven Bags
Breathable woven bags are engineered from polypropylene (PP) fabric, designed to allow controlled gas exchange. This permeability prevents moisture buildup, inhibits microbial growth, and extends shelf life—a key advantage for perishable goods like grains, coffee beans, and spices.
Key Technical Features:
- Mesh Density: Measured in Denier (D), tighter weaves (e.g., 1200D) offer durability, while looser weaves (e.g., 800D) enhance airflow.
- Lamination: Optional BOPP (Biaxially Oriented Polypropylene) coatings add moisture resistance without compromising breathability.
- PE Liners: Polyethylene (PE) inner layers provide an additional moisture barrier for hygroscopic products.
A 2023 study in the Journal of Food Engineering highlighted that breathable packaging reduces food waste by up to 18% compared to airtight alternatives, particularly in humid climates.
2. Choosing the Right Packaging Configuration
Selecting a breathable woven bag involves balancing functionality, cost, and regulatory compliance. Below is a systematic approach:
2.1 To Laminate or Not?
Lamination with BOPP film enhances printability and moisture resistance. For example, VidePak’s BOPP-laminated woven bags are ideal for branded coffee packaging, where vibrant graphics and humidity control are critical. However, unlaminated bags are preferred for products requiring natural airflow, such as root vegetables.
2.2 Inner Bag Options
Liner Type | Key Properties | Best For |
---|---|---|
PE Liner | Moisture-proof, cost-effective | Flour, sugar, dried fruits |
Aluminum Foil | Oxygen and light barrier | Coffee, spices, sensitive powders |
None | Maximum breathability | Potatoes, onions, grains |
Case Study: A rice exporter in Southeast Asia reduced spoilage rates by 22% after switching to VidePak’s PE-lined breathable bags, which balanced airflow with humidity control.
2.3 Closure Systems
- Sewn Closure: Economical for bulk commodities like animal feed.
- Heat Sealing: Airtight for powdered products (e.g., cocoa).
- Zipper or Velcro: Reusable for retail-ready packaging.
3. Why VidePak Stands Out
With 568 employees and a production capacity of 80 million bags annually, VidePak leverages Austrian Starlinger machinery and virgin PP materials to ensure consistency. Our 30+ lamination machines and 16 extrusion lines enable rapid customization, including multi-color printing and FDA-compliant inks.
Example: For a European organic flour brand, we engineered a breathable bag with a matte PE liner and anti-static coating, reducing clumping during transit.
4. Addressing Common Concerns: FAQs
Q1: How do breathable bags prevent insect infestation?
A: Integrated micro-perforations allow CO2 release, disrupting insect respiration without chemicals (supported by USDA guidelines).
Q2: Are these bags recyclable?
A: Yes! VidePak’s PP bags are 100% recyclable, aligning with EU Circular Economy directives.
Q3: What’s the lead time for custom designs?
A: With 100+ circular looms, we deliver samples in 7 days and bulk orders in 21 days.
5. The Future of Food Packaging
Trends like smart labels (e.g., RFID tags for traceability) and biodegradable additives are reshaping the industry. VidePak’s R&D team is piloting compostable PP blends, aiming to reduce landfill dependency by 2030.
References
- Smith, J. et al. (2023). Impact of Breathable Packaging on Food Preservation. Journal of Food Engineering.
- USDA. (2022). Guidelines for Safe Grain Storage.
- European Commission. (2023). Circular Economy Action Plan.
By integrating expertise, innovation, and sustainability, VidePak empowers businesses to navigate the complexities of modern food packaging. Whether you’re packaging quinoa in Peru or spices in India, our solutions are engineered for excellence.
Anchor Links:
- Learn more about BOPP-laminated woven bags and their role in branding.
- Explore PE liner applications in moisture-sensitive environments.