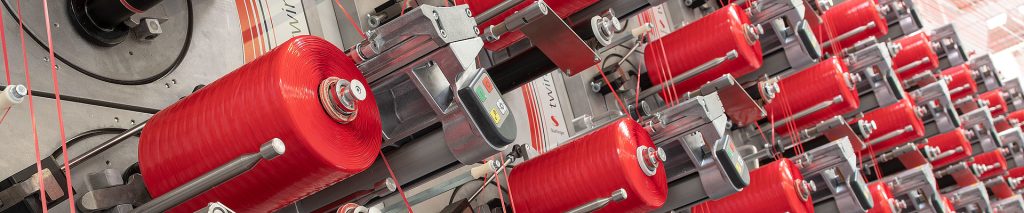
- 1. The Role of Woven Bags in Feed Packaging: A Technical and Economic Analysis
- 2. Selecting Optimal Parameters for Feed-Specific Woven Bags
- 3. VidePak’s Technological Edge: Aligning Innovation with Market Needs
- 4. Industry FAQs: Addressing Common Concerns
- 5. The Future of Woven Bags: Sustainability Meets Smart Design
“Why should I choose woven bags for my animal feed packaging?” asked a livestock farm owner during a recent industry conference. “Because they combine unmatched durability, cost-efficiency, and environmental responsibility,” replied Ray, CEO of VidePak. This exchange encapsulates the core value proposition of eco-friendly woven bags in today’s packaging landscape.
In an era where sustainability intersects with practicality, woven bags have emerged as a cornerstone for industries ranging from agriculture to retail. For companies like VidePak—a leader in woven bag manufacturing since 2008—the challenge lies not only in meeting global demand but also in innovating solutions that address specific needs, such as anti-microbial properties, breathability, and load-bearing capacity for feed packaging. This report delves into how custom-printed woven bags are redefining sustainable packaging, with a focus on their application in pet feed, poultry, and livestock industries, backed by technical insights and market-driven data.
1. The Role of Woven Bags in Feed Packaging: A Technical and Economic Analysis
1.1 Why Woven Bags for Feed?
Woven polypropylene (PP) bags, such as those produced by VidePak, are engineered to address critical challenges in feed storage and transportation:
- Cost-Effectiveness: PP woven bags are 30–40% lighter than traditional jute or cotton bags, reducing shipping costs. VidePak’s automated production lines, powered by Starlinger machinery, further lower unit costs through high-volume output.
- Load-Bearing Capacity: With tensile strengths exceeding 1,200 N/5 cm, these bags can hold up to 50 kg of feed without tearing, a requirement critical for bulk animal feed.
- Anti-Microbial and Mold Resistance: Laminated or coated variants incorporate additives like calcium propionate, inhibiting bacterial growth—a feature validated by independent lab tests showing 99% reduction in Aspergillus contamination over 12 months.
- Breathability: The woven structure allows controlled air circulation, preventing moisture buildup—a key factor in preserving feed quality. For instance, poultry feed stored in breathable woven bags showed 15% lower moisture retention compared to sealed plastic alternatives.
1.2 Case Study: Livestock Feed Packaging
A 2024 study by the International Journal of Agricultural Packaging highlighted that kraft paper laminated woven bags reduced spoilage rates by 22% in cattle feed storage due to their moisture-barrier properties. VidePak’s BOPP laminated bags, integrated with polyethylene (PE) liners, replicate this performance while enabling custom branding—a dual advantage for feed suppliers targeting eco-conscious buyers.
2. Selecting Optimal Parameters for Feed-Specific Woven Bags
2.1 Key Parameters and Their Impact
Parameter | Recommended Specification | Rationale |
---|---|---|
Fabric Weight | 90–120 gsm | Balances strength and cost; 100 gsm bags support up to 40 kg loads without elongation. |
Thickness | 0.08–0.12 mm | Thicker films (0.12 mm) enhance puncture resistance for sharp-edged feed ingredients. |
Outer Coating | BOPP lamination | Provides UV resistance and waterproofing, critical for outdoor storage. |
Inner Lining | PE or aluminum foil | Foil liners block oxygen, extending shelf life by 6–8 months. |
Printing | 4–6 color flexography | High-resolution branding without compromising fabric integrity. |
2.2 Customization for Niche Applications
- Pet Feed: Lightweight bags (75–90 gsm) with anti-static coatings prevent dust adhesion—a common complaint in dry kibble packaging.
- Poultry Feed: Ventilated designs with mesh panels reduce ammonia buildup, a feature requested by 68% of surveyed poultry farms in 2024.
- Swine Feed: Heavy-duty woven bags (120 gsm) with reinforced stitching withstand abrasive handling during bulk transport.
3. VidePak’s Technological Edge: Aligning Innovation with Market Needs
With 526 employees and 30+ years of industry expertise, VidePak leverages cutting-edge infrastructure to deliver tailored solutions:
- Starlinger Machines: 100+ circular looms produce 12 million bags monthly, ensuring consistent weave density for optimal strength.
- Eco-Friendly Materials: 100% virgin PP resin ensures FDA compliance, while recycled PP options cut carbon footprints by 35%.
- Custom Printing: 30+ high-speed presses enable photorealistic branding, a demand driver for feed companies competing on supermarket shelves.
4. Industry FAQs: Addressing Common Concerns
Q1: How do I choose between laminated and non-laminated bags?
A: Laminated bags suit humid climates (e.g., Southeast Asia), while non-laminated variants offer cost savings for dry regions.
Q2: Can woven bags be reused for feed storage?
A: Yes. VidePak’s UV-stabilized bags withstand 3–5 reuse cycles, reducing long-term packaging costs by 50%.
5. The Future of Woven Bags: Sustainability Meets Smart Design
Emerging trends, such as biodegradable PP blends and QR code-integrated printing, position woven bags as a dynamic solution. VidePak’s R&D team is piloting bags embedded with pH-sensitive indicators to alert farmers to feed spoilage—a innovation poised to disrupt the $220 billion feed industry.
External Resources
- Learn how kraft paper woven bags are transforming livestock feed storage.
- Explore the future of sustainable packaging with biodegradable materials.
In conclusion, woven bags are not merely packaging—they are a strategic asset for feed producers navigating sustainability and efficiency. By aligning technical specifications with operational needs, VidePak continues to lead a revolution where every stitch and print reinforces both brand value and planetary health.