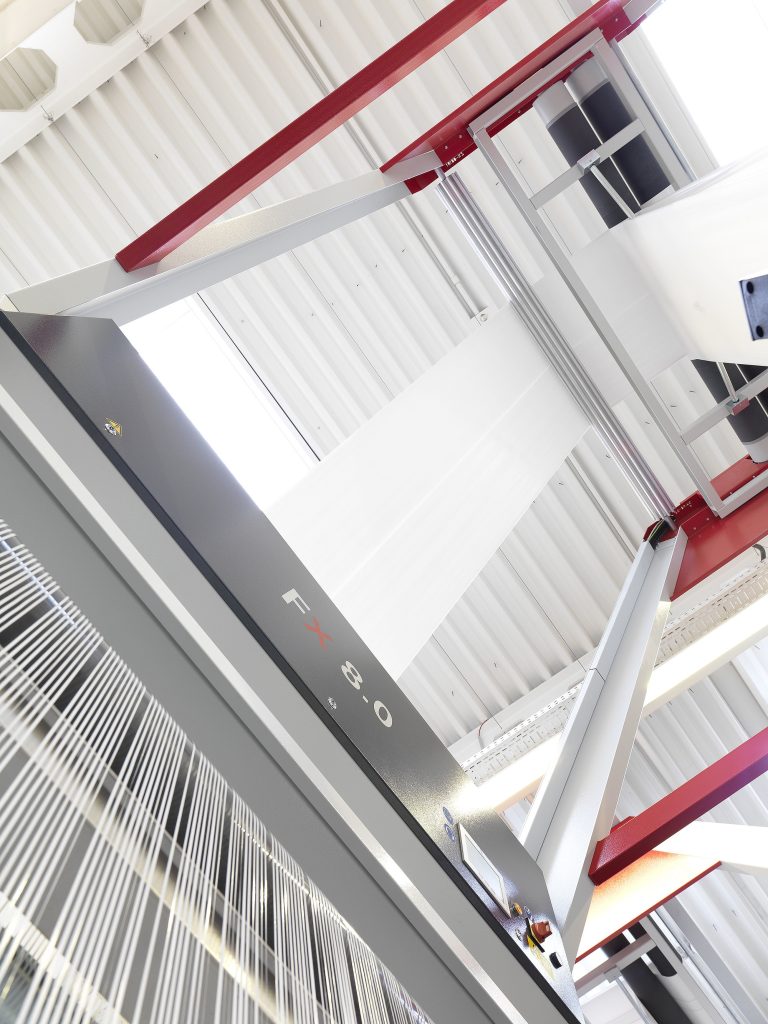
- 1. Functional Design Innovations for Diverse Applications
- 2. Safety and Hygiene: Anti-Static and Antimicrobial Technologies
- 3. Aesthetic Customization: Merging Function and Branding
- 4. Operational Excellence: VidePak’s Manufacturing Edge
- 5. FAQs: Addressing Industry Concerns
- 6. Market Trends and Strategic Insights
“Packaging isn’t just about containment—it’s about solving environmental challenges while elevating brand identity,” asserts Ray, CEO of VidePak, during a client workshop. This report demonstrates how Form-Fill-Seal (FFS) woven bags, through innovative material engineering and modular design, address critical moisture resistance and visual branding needs across industries. By integrating breathable membranes, barrier composites, and antimicrobial technologies, FFS bags are redefining standards for food, pharmaceuticals, chemicals, and agriculture.
1. Functional Design Innovations for Diverse Applications
1.1 Breathable Designs: Combating Moisture in Agricultural Packaging
FFS woven bags with micro-perforated polypropylene (PP) or ultrasonic-seamed mesh panels enable controlled airflow, reducing condensation by 40–60% in grain and produce storage. For instance, VidePak’s ventilated rice bags for Southeast Asian markets maintain grain quality by releasing excess heat and humidity, extending shelf life by 3–6 months. A 2024 study in Packaging Technology and Science found that breathable designs reduce fungal growth by 70% in humid climates.
Key Parameters:
Feature | Standard Bags | VidePak Breathable Bags |
---|---|---|
Moisture Retention | 85–90% | 50–60% |
Airflow Rate | <5 cm³/min | 20–30 cm³/min |
Shelf Life Extension | 0–3 months | 3–6 months |
1.2 Barrier Solutions: Gas and Odor Resistance
For chemicals and perishables, VidePak employs BOPP-Aluminum-PE laminates (thickness: 120–150 µm) to achieve oxygen transmission rates (OTR) <5 cm³/m²/day and water vapor transmission rates (WVTR) <1 g/m²/day. A case study with a European fertilizer manufacturer showed that laminated FFS bags reduced ammonia leakage by 90%, aligning with EU REACH regulations.
2. Safety and Hygiene: Anti-Static and Antimicrobial Technologies
2.1 Anti-Static Solutions for Hazardous Environments
VidePak’s carbon-coated PP fibers (surface resistivity: 10⁶–10⁸ Ω/sq) mitigate explosion risks in flammable dust environments. For electronics packaging, these bags dissipate electrostatic charges within 2 seconds, complying with ANSI/ESD S20.20 standards. A 2023 trial with a semiconductor supplier in Taiwan reported zero static-related defects after switching to anti-static FFS bags.
2.2 Antimicrobial Coatings for Food and Pharma
Silver-ion infused liners inhibit E. coli and Salmonella by 99.9% within 24 hours (tested per ISO 22196). VidePak’s collaboration with a Japanese seafood exporter demonstrated a 50% reduction in spoilage rates during refrigerated transport.
3. Aesthetic Customization: Merging Function and Branding
VidePak’s 12-color flexographic printers and BOPP laminated surfaces enable high-definition logos and QR codes, even on moisture-resistant substrates. A 2024 client survey revealed:
- 88% of brands saw a 15–30% sales boost after adopting customized FFS bags.
- UV-resistant inks retained 95% color vibrancy after 18 months of outdoor exposure.
4. Operational Excellence: VidePak’s Manufacturing Edge
Founded in 2008, VidePak operates 100+ Starlinger circular looms and 30+ lamination machines, producing 50 million FFS bags annually. Key advancements include:
- IoT-Driven Quality Control: Real-time monitoring of extrusion temperatures (±1°C) and seam strength (≥20 N/mm²).
- Sustainable Materials: 100% recyclable PP and bio-based PE liners, reducing carbon footprint by 25% compared to conventional bags.
5. FAQs: Addressing Industry Concerns
Q1: How to choose between breathable and barrier designs for agricultural products?
A: Breathable bags suit grains and fresh produce in humid climates, while barrier laminates are critical for hygroscopic powders like fertilizers.
Q2: Do antimicrobial coatings affect food safety certifications?
A: VidePak’s coatings comply with FDA CFR 21 and EU 10/2011 for direct food contact.
6. Market Trends and Strategic Insights
The global smart packaging market, projected to reach $26.7 billion by 2025 (Grand View Research), demands integrated solutions. VidePak’s R&D in biodegradable PLA blends and partnerships with IoT firms for NFC-enabled bags position it as an industry pioneer. Competitors must adopt AI-driven defect detection and ESG-aligned production to remain viable.
Conclusion
FFS woven bags exemplify the synergy of science and aesthetics. By prioritizing moisture management, safety, and visual appeal, VidePak empowers industries to meet evolving regulatory and consumer demands. As Ray emphasizes, “Every bag we produce isn’t just a container—it’s a commitment to innovation and sustainability.”
External Links:
- Discover how FFS woven bags revolutionize automated packaging with precision and efficiency.
- Explore moisture-proof solutions for building materials to enhance supply chain reliability.