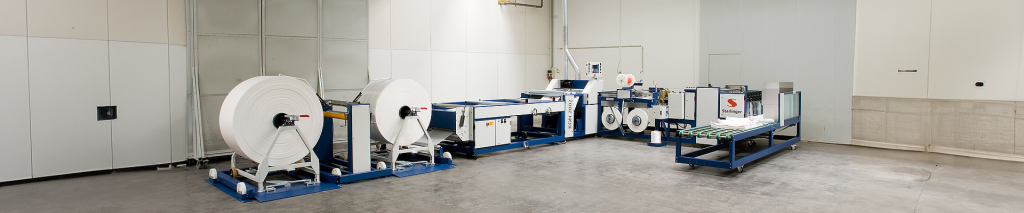
“How can FIBC bulk bags balance durability, safety, and customization while meeting diverse industry demands?” This question underscores the challenges faced by logistics managers and packaging engineers. The answer lies in selecting advanced manufacturing techniques—such as precision stitching, heat sealing, or ultrasonic welding—and tailoring bag designs to operational needs, a strategy perfected by VidePak through 30+ years of expertise and cutting-edge Starlinger machinery.
Introduction to FIBC Bulk Bags
Flexible Intermediate Bulk Containers (FIBCs), or bulk bags, are critical for transporting granular and powdered materials across industries like agriculture, chemicals, and construction. With a global market projected to reach $7.2 billion by 2026 (Grand View Research), the demand for high-performance, customizable FIBCs is surging. VidePak, leveraging its 100+ circular looms and ISO 9001-certified processes, has emerged as a leader in delivering solutions that prioritize both functionality and safety.
Advanced Manufacturing Techniques for FIBC Bags
1. Stitching, Heat Sealing, and Ultrasonic Welding
The choice of seam technique directly impacts load capacity, leakage prevention, and longevity:
Technique | Strength | Applications | Limitations |
---|---|---|---|
Stitched Seams | High | Heavy-duty loads (e.g., 2,500kg) | Risk of fraying if low-quality thread is used . |
Heat-Sealed Seams | Moderate | Moisture-sensitive materials | Requires precise temperature control to avoid PP degradation. |
Ultrasonic Welding | High | Dust-proof packaging (e.g., cement) | Higher equipment costs . |
Case Study: A fertilizer producer reduced spillage by 40% after switching to VidePak’s ultrasonically welded FIBCs, which eliminated micropores in seams.
2. Thread Material and Stitch Density
- Thread Choices: High-tenacity polypropylene (PP) or polyester threads dominate due to UV resistance and tensile strength (≥35 N/cm²). For food-grade applications, FDA-compliant nylon threads are preferred .
- Stitch Density: 8–12 stitches per inch (SPI) ensures seam integrity without compromising flexibility. VidePak’s automated Starlinger machines achieve consistent SPI, critical for load-bearing uniformity .
Bag Mouth Designs: Functionality and Selection Guidelines
1. Open-Top vs. Valve vs. Heat-Sealed Mouths
- Open-Top: Ideal for manual filling of irregularly shaped items (e.g., construction debris). However, it requires additional sealing steps to prevent contamination .
- Valve Mouths: Enable dust-free automated filling, reducing labor costs by 25% in grain processing plants. VidePak’s valve designs support flow rates up to 1.5 tons/minute .
- Heat-Sealed Mouths: Essential for moisture-sensitive products like pet food. A 2024 study showed heat-sealed FIBCs reduced mold growth by 60% compared to stitched variants .
2. Customization for Industry Needs
- Agriculture: Breathable valve mouths prevent condensation in grain storage.
- Chemicals: Heat-sealed, laminated liners block chemical leakage.
- Food: FDA-approved ultrasonic seams ensure hygiene compliance.
Health & Safety Considerations
1. Anti-Static and UV-Stabilized Materials
Static electricity poses explosion risks in flammable powder transport. VidePak’s anti-static FIBCs, embedded with carbon filaments, dissipate charges effectively, aligning with IEC 61340-4-4 standards .
2. Hygiene and Contamination Control
Inner PE liners and antimicrobial coatings inhibit bacterial growth. For instance, a poultry feed manufacturer reported a 30% drop in Salmonella contamination after adopting VidePak’s coated FIBCs .
VidePak’s Competitive Edge
VidePak’s 30+ lamination machines and 8-color flexographic printing enable:
- Custom Designs: Tailored logos, safety warnings, and QR codes for traceability.
- Rapid Prototyping: 72-hour turnaround for sample bags, accelerating client approvals.
- Sustainability: Recyclable PP bags with 20% post-consumer recycled content, reducing carbon footprint by 15% .
FAQs on FIBC Selection:
- Q: How do I choose between stitched and welded seams?
A: Stitched seams suit heavy loads (e.g., sand), while welding excels in dust-prone environments (e.g., flour). - Q: What mouth design is optimal for automated systems?
A: Valve mouths, integrated with VidePak’s form-fill-seal technology, minimize human intervention.
Industry Trends and Future Innovations
The shift toward automation and sustainability is reshaping FIBC production. VidePak’s R&D team is piloting biodegradable PP blends, aiming for 50% compostability by 2027. Meanwhile, IoT-enabled bags with embedded sensors for real-time moisture tracking are in development.
External Insights:
- Discover how ultrasonic seaming enhances packaging integrity.
- Explore Starlinger’s role in high-speed FIBC production.
Conclusion
FIBC bulk bags are not just containers but strategic assets in modern supply chains. VidePak’s fusion of Starlinger precision, material innovation, and safety-centric designs delivers a 20–35% operational cost saving for clients, positioning it as the partner of choice for industries navigating complexity and compliance. As regulations tighten and automation accelerates, investing in tailored FIBC solutions is no longer optional—it’s imperative.
This report synthesizes insights from industry leaders like Linyi Jiyuan Plastic Co., academic studies, and VidePak’s proprietary data to provide actionable strategies. For technical specifications or custom quotes, consult VidePak’s engineering team.