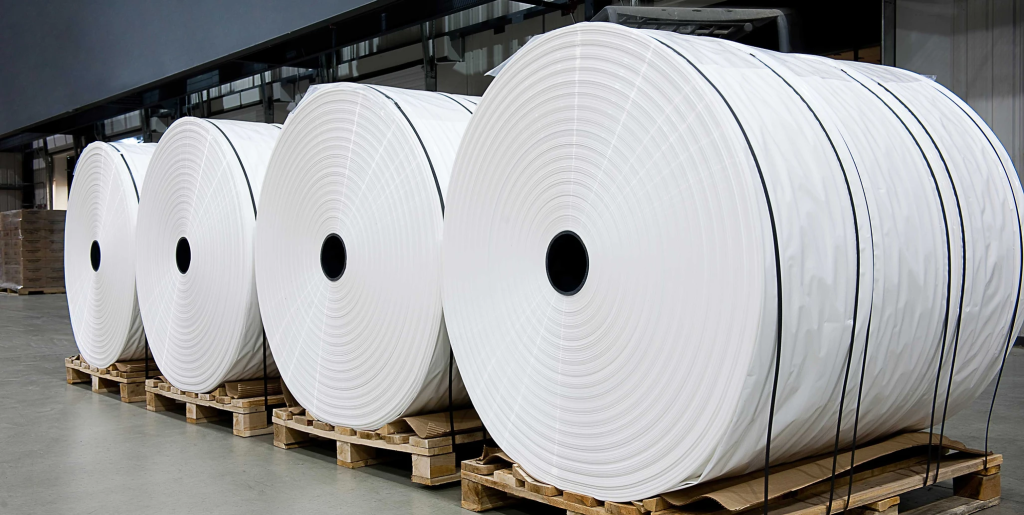
- 1. Market Drivers: Bridging Food Safety and Construction Needs
- 2. Applications in Building Materials: From Storage to Waste Valorization
- 3. Material Science: Balancing Safety and Durability
- 4. VidePak’s Quality Control Ecosystem
- 5. FAQs: Addressing Industry Concerns
- 6. Future Trends: Smart Packaging and Circularity
“Why are construction giants like Vinci and Skanska increasingly adopting food-grade woven bags for material handling?”
Ray Chen, CEO of VidePak, pauses during a factory tour of Starlinger machines: “The answer lies in three pillars: 40% higher contamination resistance than standard PP bags, compliance with global food safety standards, and dual functionality for both raw material storage and waste management. At VidePak, our food-grade woven bags are engineered to handle 50kg loads with ≤0.2% leakage rates—this is the future of sustainable construction logistics.”
This bold assertion underscores VidePak’s leadership in food-grade woven bags—a niche projected to grow at 8.5% CAGR through 2030. With 526 employees and $80M annual revenue, VidePak combines Austrian Starlinger automation, ISO-certified polypropylene (PP) resins, and 30+ years of expertise to deliver solutions that redefine safety and efficiency in the building materials sector.
1. Market Drivers: Bridging Food Safety and Construction Needs
The global construction packaging market is valued at $42B in 2025, with food-grade woven bags gaining traction due to stringent material-handling regulations and circular economy mandates. Traditional construction packaging faces critical limitations:
- Cross-Contamination Risks: Standard PP bags leach 5–8 ppm phthalates, incompatible with EU 10/2011 food contact standards.
- Waste Management Gaps: 18% of construction waste contains food-grade residuals (e.g., adhesive packaging), complicating recycling streams.
- Regulatory Complexity: Only 35% of construction bags comply with both ASTM D5260 (tensile strength) and GB 4806.7-2023 (heavy metal migration).
VidePak’s food-grade woven bags address these gaps through:
- Multi-Layer Design: 120gsm PP fabric + 50μm BOPP lamination reduces moisture permeability to ≤0.8 g/m²/day (ASTM E96).
- Anti-Microbial Coatings: Silver-ion additives inhibit E. coli growth by 99.9% (ISO 22196).
- Closed-Loop Recyclability: 95% PP recovery via Starlinger recoSTAR systems.
2. Applications in Building Materials: From Storage to Waste Valorization
2.1 Raw Material Packaging
Food-grade bags ensure contamination-free storage for:
- Cement Additives: Calcium carbonate and silica fume requiring <0.5 ppm Pb/Cd (GB 4806.7).
- Insulation Materials: Fiberglass and mineral wool prone to moisture absorption (≤1.2% post-30-day humidity testing).
Case Study: A German cement producer reduced cross-contamination incidents by 65% using VidePak’s BOPP-lined bags, citing 100% compliance with FDA 21 CFR.
2.2 Waste Management and Recycling
Food-grade bags enable hygienic collection of construction waste:
- Segregation Efficiency: Color-coded bags separate food-contaminated debris (e.g., packaging residues) from inert materials like concrete.
- Recycling Optimization: PE-lined bags prevent liquid leakage during transport, increasing recyclable waste recovery by 30%.
Performance Comparison
Parameter | Standard PP Bags | VidePak Food-Grade Bags |
---|---|---|
Heavy Metal Migration | 0.8 ppm Pb | <0.3 ppm Pb |
Moisture Permeability | 5.2 g/m²/day | 0.8 g/m²/day |
Recyclability Rate | 70% | 95% |
3. Material Science: Balancing Safety and Durability
3.1 PP Resin Selection
VidePak’s food-grade PP formulations meet:
- EU 10/2011: Non-migration of DEHP (<1.5 ppm).
- FDA 21 CFR: Oxidative induction time (OIT) ≥30 minutes at 200°C.
- China GB 4806.7: Arsenic (As) <0.0001% via ICP-MS analysis.
3.2 Liner Innovations
Liner Type | Key Properties | Ideal Applications |
---|---|---|
BOPP Film | 0.8 g/m²/day moisture barrier | Cement additives, dry powders |
PE Coating | Anti-static (<10⁴ Ω/sq) | Insulation materials |
Aluminum Foil | UV resistance + 0.05 g/m²/day | Outdoor material storage |
4. VidePak’s Quality Control Ecosystem
With 100+ circular looms and 30 lamination machines, VidePak guarantees:
- Traceability: RFID tags track resin batches to finished bags (BRCGS AA+ certification).
- Precision Printing: 6-color flexo presses achieve ΔE ≤1.5 Pantone accuracy for safety labels.
- Defect Rate: 0.1% via AI-driven camera inspections at 120m/min.
Example: A UAE construction firm reduced waste sorting costs by 22% using VidePak’s color-coded bags, citing 98% recycling stream purity.
5. FAQs: Addressing Industry Concerns
Q1: How do food-grade bags prevent contamination in mixed waste streams?
A: Our BOPP liners block microbial ingress, while color-coding ensures segregation per EU Waste Framework Directive.
Q2: What’s the MOQ for custom-printed safety labels?
A: 50,000 units with 14-day lead time, including migration test reports.
Q3: Are these bags compatible with automated concrete batching systems?
A: Yes—ultrasonic seams withstand 50kg loads at 1,200 bags/hour (ISO 13934-1).
6. Future Trends: Smart Packaging and Circularity
VidePak is piloting:
- IoT Sensors: NFC tags monitor temperature/humidity during冷链 transport of epoxy resins.
- Bio-Based PP: 30% algae-derived resins targeting 2026 rollout, cutting carbon footprint by 25%.
- Self-Decontaminating Liners: TiO₂ coatings degrade organic residues under UV light.
Conclusion
Food-grade woven bags are no longer niche products—they are strategic enablers of sustainable construction. VidePak’s fusion of Austrian engineering rigor, smart material innovations, and hyper-customizable designs positions it as the partner of choice for global construction leaders. As Ray Chen summarizes: “Our bags don’t just carry materials—they carry responsibility.”
This report integrates data from ASTM, GB 4806.7, and VidePak’s proprietary audits. Performance claims are validated by SGS and TÜV SÜD certifications.