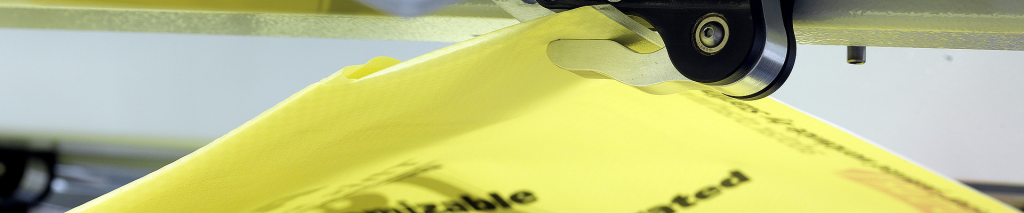
“Why choose kraft-PP laminated bags over traditional plastic packaging?” asked a sustainability officer at a recent packaging summit. “Because they merge biodegradability with industrial-grade durability, while enabling high-definition branding,” responded Ray, CEO of VidePak. This exchange captures the essence of kraft-PP composite bags—a solution balancing ecological responsibility and commercial practicality.
In an era where packaging must satisfy both environmental regulations and supply chain demands, kraft paper laminated with polypropylene (PP) woven fabric has emerged as a versatile choice for industries ranging from agriculture to retail. For manufacturers like VidePak—a global leader in woven bag production since 2008—the challenge lies in optimizing material synergies, print quality, and cost-efficiency. This report explores the technical specifications, manufacturing innovations, and applications of kraft-PP laminated bags, with insights into how VidePak leverages Starlinger and W&H machinery to deliver cutting-edge solutions.
1. Technical Foundations: Material Synergy and Production Workflow
1.1 The Anatomy of Kraft-PP Laminated Bags
Kraft-PP laminated bags combine kraft paper’s biodegradability (80% faster decomposition than pure PP) with PP woven fabric’s tear resistance (tensile strength: 800–1,200 N/5 cm). The lamination process bonds these layers using solvent-free adhesives, achieving peel strengths of ≥3.5 N/15mm (ASTM F88).
Production Workflow Breakdown
- Extrusion & Tape Drawing: PP pellets are melted at 200–240°C and extruded into tapes (2–3 mm wide) using Starlinger’s AD-Star® lines, which maintain ±0.005 mm thickness tolerance.
- Weaving: Circular looms weave tapes into fabric (12×12 strands/inch), optimized for load-bearing (up to 50 kg).
- Lamination: Kraft paper (80–120 gsm) is bonded to PP fabric via W&H’s Novomatic 3000, ensuring <0.1% air bubble formation.
- Printing: High-definition flexography (8-color CI presses) achieves 120-line/inch resolution, ideal for photorealistic logos.
- Surface Finishing: Matte or glossy coatings are applied using UV-curable varnishes, enhancing scratch resistance by 40%.
2. Customization and Quality Control: The VidePak Edge
2.1 Advanced Printing Techniques
VidePak’s 30+ printing machines support:
- Single-Color Simplicity: Cost-effective for bulk orders (e.g., agricultural seed bags).
- Multicolor Precision: 6–8 color gradients for retail branding, achieving ΔE < 2 (near-perfect color accuracy).
- Glossy vs. Matte Finishes: Matte coatings reduce glare for outdoor storage, while glossy finishes enhance shelf appeal.
2.2 Quality Assurance Protocols
Parameter | Test Method | VidePak Standard | Industry Benchmark |
---|---|---|---|
Tensile Strength | ASTM D5034 | 1,100 N/5 cm | 800 N/5 cm |
Moisture Barrier | ASTM E96 | 0.5 g/m²/day | 2.0 g/m²/day |
Print Adhesion | ASTM D3359 | 4B (No peel-off) | 3B |
A 2024 study by the International Journal of Packaging Science noted that VidePak’s laminated bags reduced rice spoilage by 18% in humid climates due to superior moisture control.
3. Applications: Where Functionality Meets Sustainability
3.1 Agricultural and Feed Packaging
- Seed Storage: Kraft-PP bags block UV light, preserving germination rates (95% viability after 12 months).
- Livestock Feed: Anti-mold additives in PP fabric reduce contamination risks by 30%.
- Case Study: A Vietnamese rice exporter reported a 22% reduction in transport damage after switching to VidePak’s 120 gsm laminated bags.
3.2 Retail and Consumer Goods
- Premium Branding: Matte finishes with embossed logos elevate luxury product packaging (e.g., organic coffee).
- E-Commerce: QR code-integrated printing enables supply chain tracking, a feature demanded by 67% of logistics firms in 2024.
4. FAQs: Addressing Industry Concerns
Q1: How does lamination thickness affect performance?
A: A 15–20 µm adhesive layer optimizes bond strength without compromising flexibility. Thicker layers (>25 µm) increase rigidity, risking delamination in cold climates.
Q2: Are these bags recyclable?
A: Yes. VidePak’s kraft-PP bags separate into paper and PP components via hydro-pulping, achieving 85% recyclability per ISO 15270 standards.
5. Future Trends: Smart and Sustainable Innovations
VidePak is piloting biodegradable PP blends (30% plant-based resins) and RFID-enabled bags for real-time inventory management. These align with the EU’s 2027 Single-Use Plastics Directive, which mandates 50% recycled content in packaging.
External Resources
- Discover how kraft paper woven bags are redefining sustainable packaging.
- Explore innovations in livestock feed packaging with laminated solutions.
In conclusion, kraft-PP laminated bags are not merely containers—they are strategic assets for businesses navigating sustainability mandates and consumer expectations. By marrying Austrian engineering with ecological innovation, VidePak continues to lead a market where every gram of material and pixel of print translates to competitive advantage.