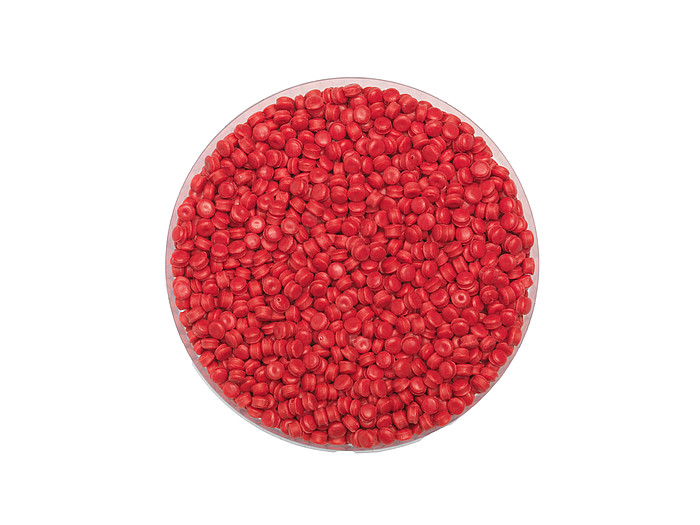
A Dialogue with Industry Leaders
Ray, CEO of VidePak: “At VidePak, our laminated woven bags are not just products—they’re precision-engineered solutions. By integrating Starlinger’s cutting-edge co-extrusion technology and rigorous quality protocols, we ensure every bag meets global standards for durability, sustainability, and performance.”
Dr. Laura Simmons, Materials Engineer: “The multi-layered co-extrusion process is transformative. It allows manufacturers like VidePak to tailor barrier properties, enhance recyclability, and address diverse industrial demands—all while optimizing production efficiency.”
This conversation highlights the core themes of this report: advanced manufacturing techniques and quality-driven innovation, both critical for VidePak’s leadership in the $42 billion global woven packaging market.
1. The Manufacturing Process: A Step-by-Step Breakdown
Laminated woven bags combine polypropylene (PP) layers with functional coatings (e.g., BOPP, PE) to achieve moisture resistance, UV protection, and tensile strength. VidePak’s production line, powered by Austrian Starlinger and W&H machinery, exemplifies industrial excellence.
1.1 Extrusion: The Foundation of Strength
The process begins with extruding virgin PP resin into flat tapes. VidePak’s 16 extrusion lines operate at temperatures of 200–240°C, ensuring optimal polymer flow and homogeneity.
- Quality Control: Melt flow index (MFI) tests (ASTM D1238) verify resin consistency, with tolerances maintained at ±0.5 g/10 min.
- Starlinger’s Role: The company’s extrusion systems feature real-time thickness monitoring, reducing material waste by 12% compared to conventional systems.
1.2 Tape Drawing and Weaving: Precision in Structure
Tapes are stretched to align polymer molecules, enhancing tensile strength (up to 8 N/tex). VidePak’s 100+ circular looms weave these tapes into fabric at speeds of 150–200 rpm.
- Key Metric: Fabric density (12×12 to 14×14 threads/inch) is calibrated for target applications (e.g., 14×14 for heavy-duty construction bags).
Table 1: Critical Production Parameters
Process Stage | Parameter | Standard |
---|---|---|
Extrusion | Melt Temperature | 220°C ±5°C |
Tape Drawing | Draw Ratio | 1:6 to 1:8 |
Weaving | Loom Speed | 180 rpm |
Lamination | Adhesion Strength | ≥4.0 N/mm² (ASTM D903) |
1.3 Lamination and Coating: Barrier Enhancement
VidePak’s 30 lamination machines apply BOPP or PE layers via Starlinger’s multi-layer co-extrusion. This step is critical for:
- Moisture Resistance: BOPP coatings reduce water vapor transmission to ≤5 g/m²/day.
- Customization: Multi-layer structures (e.g., PP/PE/Aluminum) are engineered for specific industries, such as food-grade packaging with FDA-compliant barriers.
1.4 Printing and Bag Formation: Branding Meets Function
High-definition flexographic printers apply logos, safety labels, or regulatory symbols. VidePak’s 30 printing machines support 10-color printing with registration accuracy of ±0.1 mm.
- Case Study: A client in the agricultural sector reported a 30% increase in brand recognition after switching to VidePak’s digitally printed valve bags.
2. Quality Assurance: Engineering Perfection at Every Stage
VidePak’s ISO 9001-certified quality framework spans raw material selection to final inspection.
2.1 In-Line Monitoring and Testing
- Extrusion: Infrared sensors detect thickness deviations (>±0.02 mm triggers auto-adjustment).
- Weaving: Automated optical inspection (AOI) systems flag fabric defects (e.g., misweaves) at 200 frames/second.
- Lamination: Peel tests (ASTM D903) ensure interlayer adhesion exceeds 4.0 N/mm².
2.2 Sustainability Metrics
- Recyclability: VidePak’s mono-material PP bags achieve 95% recyclability, aligning with the EU’s Circular Economy Action Plan.
- Waste Reduction: Production scraps are repurposed into non-woven fabrics, diverting 1,200+ tons/year from landfills.
3. Market Positioning and Technological Edge
With annual revenues of $80 million, VidePak serves 50+ countries, leveraging its Starlinger-powered infrastructure to outperform competitors.
3.1 Case Study: Pharmaceutical Packaging
A European pharmaceutical manufacturer reduced product spoilage by 18% using VidePak’s BOPP-laminated bags, citing superior oxygen barrier properties (≤0.1 cc/m²/day).
3.2 Global Trends and Innovations
- Smart Packaging: RFID-enabled bags for supply chain tracking (piloted in VidePak’s 2024 product line).
- Bio-Based PP: Partnerships with biopolymer startups aim to reduce carbon footprint by 25% by 2026.
4. Frequently Asked Questions (FAQs)
Q1: How does co-extrusion enhance barrier properties?
Answer: Co-extrusion allows simultaneous application of PP, PE, and functional layers, creating a seamless barrier against moisture, gases, and contaminants.
Q2: What certifications ensure product safety?
Answer: VidePak’s bags meet FDA (US), EU 10/2011 (food contact), and ISO 22000 standards.
Q3: Can customized printing withstand harsh environments?
Answer: Yes. UV-resistant inks and over-lamination ensure print durability even in tropical climates.
5. Future Directions: Sustainability and Automation
- Closed-Loop Recycling: VidePak plans to launch a take-back program for post-consumer bags in 2025.
- AI-Driven Production: Predictive maintenance algorithms for Starlinger machines aim to reduce downtime by 20%.
Final Insight
As Ray emphasizes, “Our investment in Starlinger’s technology isn’t just about efficiency—it’s about redefining what’s possible in sustainable packaging.” By merging advanced co-extrusion with circular economy principles, VidePak is poised to lead the next wave of industrial innovation.
External Resources:
- Discover how multi-layer laminated bags solve complex packaging challenges.
- Explore precision printing techniques for brand differentiation.
This report synthesizes technical insights, industry benchmarks, and VidePak’s operational data to provide a roadmap for excellence in laminated woven bag production.