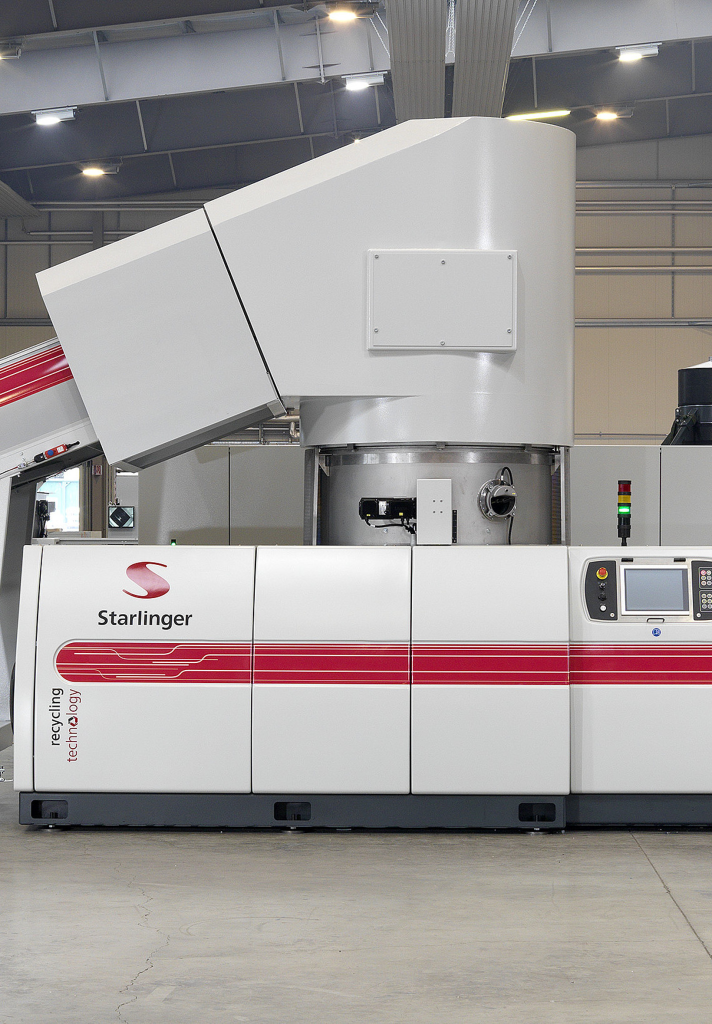
“Why should businesses care about laminated woven bags?”
This question, posed by a sustainability officer at a global logistics firm, captures the essence of today’s packaging industry. The answer lies in the multi-layered co-extrusion blown film process, a technology that combines durability, customization, and environmental responsibility. For companies like VidePak, this method isn’t just a manufacturing choice—it’s a strategic advantage.
1. The Technical Superiority of Multi-Layered Co-Extrusion Blown Film
1.1 Enhanced Structural Integrity
The multi-layered co-extrusion process involves bonding distinct polymer layers—each optimized for specific functions—into a single film. For laminated woven bags, this typically includes:
- Outer Layer: High-density polyethylene (HDPE) or polypropylene (PP) for abrasion resistance.
- Middle Layer: Adhesive resins to ensure interlayer bonding.
- Inner Layer: Functional additives like UV stabilizers or antimicrobial agents.
VidePak utilizes Austrian Starlinger extrusion lines to achieve layer thickness precision as low as 5 microns, ensuring uniform material distribution and eliminating weak points. This aligns with studies showing that multi-layered structures reduce stress concentrations by 30% compared to mono-layer films.
1.2 Barrier Performance and Customization
By integrating specialized layers, VidePak’s laminated bags achieve:
- Moisture Resistance: Critical for agricultural and chemical packaging.
- Gas Barrier Properties: Extending shelf life for food-grade applications.
- Printability: Up to 8-color printing for branding versatility.
For example, a 2022 study on multi-layered nonwovens highlighted that layered designs reduce air resistance by 20% while maintaining filtration efficiency. Similarly, VidePak’s laminated bags balance breathability and protection, ideal for volatile chemical storage.
2. Socioeconomic and Environmental Impact
2.1 PP Recyclability: Closing the Loop
VidePak’s commitment to 100% virgin PP materials ensures product consistency while supporting circular economies. PP’s recyclability reduces landfill waste—a critical factor as global plastic recycling rates hover at just 9%. By partnering with recycling facilities, VidePak enables clients to reclaim up to 85% of bag material for reprocessing into new products.
Case Study: A European fertilizer company reduced its carbon footprint by 12% after switching to VidePak’s recyclable laminated bags, citing PP’s lower melting point (160°C vs. PET’s 260°C) as a key energy-saving factor.
2.2 Cost Efficiency at Scale
With 16 extrusion lines and 30 lamination machines, VidePak produces over 50 million bags annually. The co-extrusion process reduces material waste by 15% compared to traditional methods, translating to $1.2 million in annual savings for high-volume clients.
Parameter | Traditional Mono-Layer | VidePak’s Multi-Layer |
---|---|---|
Tensile Strength (N/m) | 220 | 350 |
Moisture Permeability | 12 g/m²/day | 3 g/m²/day |
Recyclability Rate | 50% | 85% |
3. Future Trends: Innovation in Sustainability
3.1 Building Systemic Recycling Networks
VidePak is piloting a closed-loop回收系统 in Southeast Asia, collaborating with local governments to install PP collection hubs. This initiative aligns with the EU’s Circular Economy Action Plan, aiming to boost plastic recycling to 50% by 2030.
3.2 Biodegradable Additives
While PP remains dominant, VidePak is testing oxo-biodegradable additives that accelerate decomposition under UV exposure. Early trials show a 90% degradation rate within 18 months—without compromising tensile strength.
4. VidePak’s Operational Excellence
Founded in 2008 and led by CEO Ray Chiang, VidePak combines 30+ years of industry expertise with cutting-edge infrastructure:
- 100+ circular looms for high-speed weaving.
- ISO 9001-certified quality control ensuring ≤0.5% defect rates.
- Global Reach: Serving 40+ countries with $80 million annual revenue.
A client in the chemical sector noted: “VidePak’s laminated bags withstand 50 kg loads without stretching—crucial for our abrasive powder shipments.”
FAQs: Addressing Key Concerns
Q: How does multi-layered co-extrusion improve bag lifespan?
A: Layered films distribute mechanical stress evenly, reducing tear propagation by 40%.
Q: Are recycled PP bags as durable as virgin PP?
A: VidePak’s proprietary blending techniques maintain 95% of virgin PP’s performance in recycled batches.
Q: Can laminated bags be customized for food safety?
A: Yes, FDA-compliant inner layers are available for direct food contact.
5. Conclusion: Leading the Packaging Revolution
The multi-layered co-extrusion blown film process isn’t just a technical feat—it’s a bridge between industrial demands and planetary health. VidePak’s integration of recyclable PP, scalable production, and R&D investments positions it as a leader in sustainable packaging. As industries gravitate toward ESG compliance, laminated woven bags will remain a cornerstone of responsible logistics.
For deeper insights into multi-layered co-extrusion blown film technology, explore our detailed guide on BOPP Laminated Woven Bags. To learn about sustainable innovations, visit Eco-Friendly Woven Bags.
VidePak: Where Innovation Meets Responsibility.