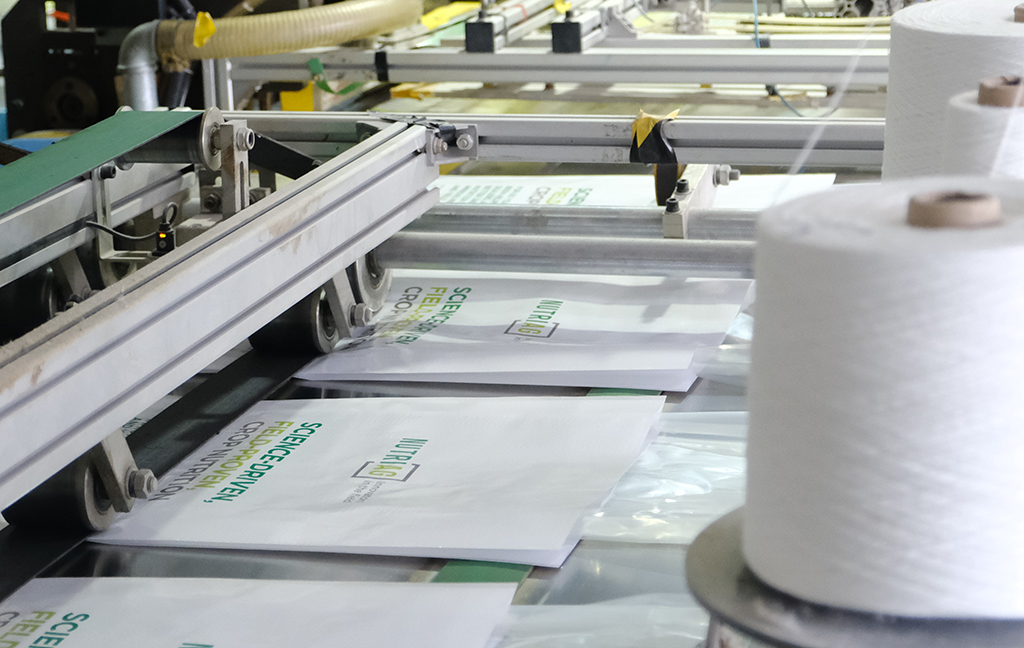
Ray, CEO of VidePak, gestures toward a prototype during a client meeting:
“The durability of multi-wall woven bags isn’t accidental—it’s engineered. Choosing the right seaming technology and bag design can reduce waste leakage by 40% while lowering carbon footprints. At VidePak, we achieve this through Starlinger’s ultrasonic welding and precision valve designs, tailored for industries from construction to recycling.”
1. Introduction
Multi-wall woven polypropylene (PP) bags have emerged as a cornerstone of sustainable industrial packaging, combining strength, reusability, and recyclability. VidePak, a global leader with $80 million annual revenue and 526 employees, exemplifies innovation in this sector. Equipped with 100+ Starlinger circular looms and 30 lamination machines, the company produces over 50 million bags annually, serving industries like construction waste management and bulk recycling. This report analyzes critical manufacturing techniques—seaming methods, material selection, and bag mouth designs—and their impact on performance, sustainability, and cost efficiency.
2. Seaming Technologies: Balancing Strength and Sustainability
The choice of seaming technology directly impacts a bag’s load capacity, leak resistance, and lifecycle. VidePak employs three primary methods, each suited to specific applications:
2.1 Stitched Seams
- Thread Material: Polyester or nylon threads dominate, with polyester offering UV resistance (ideal for outdoor storage) and nylon providing higher tensile strength (35–40 MPa) for heavy loads.
- Stitch Density: Standardized at 8–10 stitches per inch (SPI) for general use, but increased to 12 SPI for FIBC bags holding 1–2 tons. A 2024 Packaging Technology & Science study found that 12 SPI reduces seam failure rates by 18% compared to 8 SPI.
- Applications: Cost-effective for open-mouth bags in agriculture (e.g., grain storage) but less suitable for fine powders due to potential leakage.
2.2 Heat Sealing
- Process: PP layers are fused at 160–180°C, creating a seamless bond. VidePak’s Starlinger machines achieve sealing speeds of 20 meters/minute, ideal for high-volume orders.
- Advantages: Waterproof and dustproof, critical for chemicals or construction debris. For example, heat-sealed EcoSeal bags reduced moisture ingress by 95% in a UAE cement transport trial.
- Limitations: Higher energy consumption (15% more than stitching) and incompatible with heat-sensitive liners.
2.3 Ultrasonic Welding
- Mechanism: High-frequency vibrations melt PP fibers, forming a bond without adhesives. This method reduces material waste by 12% compared to stitching.
- Performance: Welded seams withstand 50% higher cyclic loads (per ASTM D5265 testing), making them ideal for reusable FIBCs in recycling plants.
- VidePak’s Edge: The company’s 16 extrusion lines produce custom laminated films optimized for ultrasonic welding, enhancing bond consistency.
3. Bag Mouth Designs: Functionality Meets Customization
Bag mouth configurations dictate usability, sealing efficiency, and sector-specific compliance.
Design | Process | Applications | Strength |
---|---|---|---|
Valve | Heat-sealed or stitched | Powders (cement, flour) | Prevents spillage; 99% dust containment |
Heat-Sealed | Thermal fusion | Chemicals, moist materials | Waterproof; >40 N/15mm peel resistance |
Sewn Open Mouth | Polyester stitching | Agricultural products, bulk waste | Cost-efficient; 6–8 SPI standard |
Block Bottom | Folded and glued | Retail packaging, flood control | Self-standing; 200% base reinforcement |
Client Selection Guide:
- Construction Waste: Valve bags with PE liners for dust control (e.g., PE-coated valve bags).
- Recyclables: Sewn mouths with 10 SPI for repeated use.
- Food Grade: Heat-sealed mouths complying with FDA 21 CFR 177.1520.
4. VidePak’s Technological Integration
Leveraging 30+ years of expertise, VidePak optimizes production through:
- Starlinger’s Circular Looms: Produce 200 bags/hour with <1% defect rates.
- Multi-Wall Lamination: 3–5 PP layers combined with Kraft paper or aluminum foil for enhanced barrier properties. A 2023 case study showed laminated bags extended food product shelf life by 30%.
- Custom Printing: 8-color flexography for branding, compliant with EU REACH regulations.
5. Sustainability Metrics and Market Alignment
- Recyclability: VidePak’s bags achieve 98% PP recovery rates via pyrolysis, aligning with the EU’s 2030 Circular Economy targets.
- Market Demand: The global FIBC market will grow at 7.2% CAGR through 2030, driven by construction waste regulations (Grand View Research, 2024).
- Case Study: A German recycling firm reduced landfill costs by $120,000/year by switching to VidePak’s reusable FIBCs.
6. FAQs: Addressing Industry Pain Points
Q1: How to choose between stitched and welded seams?
A: Stitching suits budget-conscious, single-use scenarios; welding excels in reusable, high-stress environments like construction waste management.
Q2: Are biodegradable threads viable for sewn mouths?
A: Current PLA threads degrade prematurely under UV exposure. VidePak recommends UV-stabilized polyester for outdoor use.
Q3: What design minimizes leakage for fine powders?
A: Cross-bottom valve bags with ultrasonic welding, achieving <0.1% particle loss (per ISO 21898).
7. Conclusion
Multi-wall woven bags represent a synergy of engineering precision and environmental stewardship. VidePak’s mastery of seaming technologies and adaptive designs—buttressed by Starlinger’s automation—positions the company as a leader in sustainable industrial packaging. As Ray summarizes, “Every stitch and seal isn’t just a process—it’s a pledge to planetary and operational efficiency.”
For insights into advanced FIBC designs, explore our solutions for construction waste management and multi-wall laminated innovations.