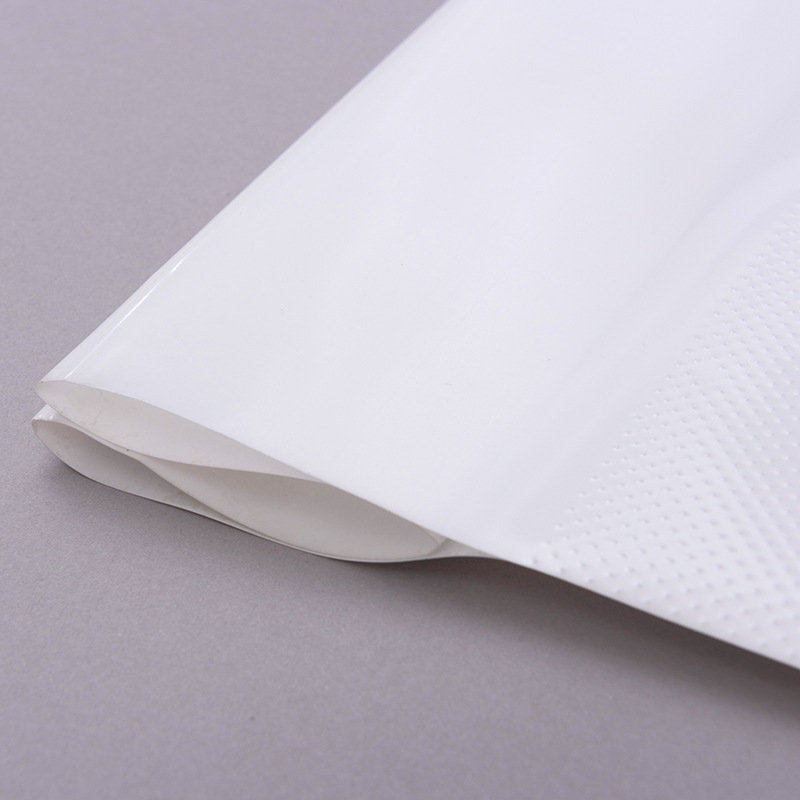
Understanding the Types and Structures of Multiwall Paper Bags
Multiwall Paper Bags and Multiwall Paper Sacks are highly versatile packaging solutions widely used across industries such as agriculture, construction, and chemicals. These bags are known for their durability, flexibility, and environmental friendliness. Manufacturers, including VidePak, employ advanced automation technologies to ensure consistency and efficiency in production.
Multiwall Paper Bags can be broadly categorized into several types based on design and application needs:
- Open-Mouth Bags: Designed for easy filling and ideal for powders and grains.
- Valve Bags: Include a self-closing valve that minimizes spillage during filling.
- Pinch-Bottom Bags: Provide excellent sealing and are commonly used for food-grade applications.
- SOS Bags (Square Bottom Bags): Highly stable, offering superior stacking capability.
- Block Bottom Bags: Combine features of flat and pinch-bottom designs, widely used for industrial applications.
The structure of Multiwall Paper Bags typically consists of multiple layers, each contributing to strength, protection, or branding:
- Outer Layer: Often kraft paper for durability and printable surface.
- Middle Layer(s): Additional kraft or recycled paper for strength.
- Inner Layer: May include polyethylene (PE) or polypropylene (PP) liners for moisture resistance.
Lamination Layers in Multiwall Paper Bags
Lamination plays a crucial role in enhancing the functional properties of Multiwall Paper Bags. VidePak’s Kraft Paper Woven Bags and Kraft Paper PP Bags integrate lamination layers for increased strength and water resistance.
Common types of lamination layers include:
Lamination Type | Material | Purpose |
---|---|---|
BOPP Lamination | Biaxially Oriented PP | High print quality, water resistance |
PE Coating | Polyethylene | Enhanced water and grease resistance |
Aluminum Foil | Laminated Foil | Barrier against light and moisture |
Fabric Lamination | PP Woven Fabric | Improved strength and tear resistance |
The choice of lamination depends on the end-use requirements. For instance, BOPP lamination is ideal for products that need high-quality printing, while PE coating is suited for applications requiring moisture protection.
For more on Multiwall Paper Bags Manufacturers, see this detailed guide.
The Role of Advanced Machinery in Manufacturing Multiwall Paper Bags
VidePak utilizes cutting-edge equipment sourced from renowned manufacturers such as Austria’s Starlinger and Germany’s W&H. These machines feature high automation levels and precision engineering, enabling production at speeds exceeding 200 bags per minute. Multi-machine integration further boosts efficiency, minimizing downtime and ensuring consistent quality.
The Influence of Drawing Processes on Durability and Flexibility
One of the most critical factors influencing the performance of Kraft Paper Woven Bags and Kraft Paper PP Bags is the drawing process. Drawing refers to the stretching of PP or PE fibers during the manufacturing of woven fabrics. This process has a profound impact on the bag’s properties:
Key Effects of the Drawing Process
- Enhanced Tensile Strength: The drawn fibers in the woven fabric provide high tensile strength, enabling the bags to withstand heavy loads without tearing. This makes them suitable for bulk packaging of commodities such as grains and cement.
- Improved Flexibility: Properly drawn fibers allow the fabric to maintain flexibility, crucial for handling and transport. The balance between stiffness and pliability ensures ease of use while retaining strength.
- Increased Resistance to Environmental Factors: By enhancing the structural integrity of the fabric, the drawing process improves resistance to environmental stresses, such as moisture, UV exposure, and temperature fluctuations.
Advanced Drawing Technology at VidePak
VidePak employs state-of-the-art drawing machines that ensure consistent fiber quality. These systems are integrated with high-speed looms, extrusion lines, and lamination units, all sourced from Starlinger and W&H. Automation allows for precise control of parameters such as stretch ratios and temperature, ensuring uniformity and maximizing material performance.
The impact of drawing on product performance is particularly evident in applications requiring high durability. For example:
Property | Before Drawing | After Drawing |
---|---|---|
Tensile Strength (MPa) | 50-70 | 100-130 |
Elongation at Break (%) | 15-20 | 5-10 |
Water Resistance | Moderate | High |
For more insights on Multiwall Paper Bags, explore this comprehensive overview.
Ensuring Quality Through Advanced Testing
At VidePak, every Multiwall Paper Bag undergoes stringent quality checks to validate its durability and functionality. Testing includes:
- Load Tests: To verify the weight-bearing capacity.
- Environmental Simulations: To assess performance under varying humidity and temperature conditions.
- Seal Integrity: Ensuring lamination layers are flawlessly bonded.
Conclusion
The versatility and reliability of Multiwall Paper Bags lie in their thoughtful design, advanced materials, and cutting-edge manufacturing processes. With robust lamination structures and the precise application of drawing technologies, VidePak delivers exceptional packaging solutions tailored to diverse industrial needs. By leveraging automation and the expertise of Starlinger and W&H, VidePak continues to set benchmarks for quality and innovation in the packaging industry.