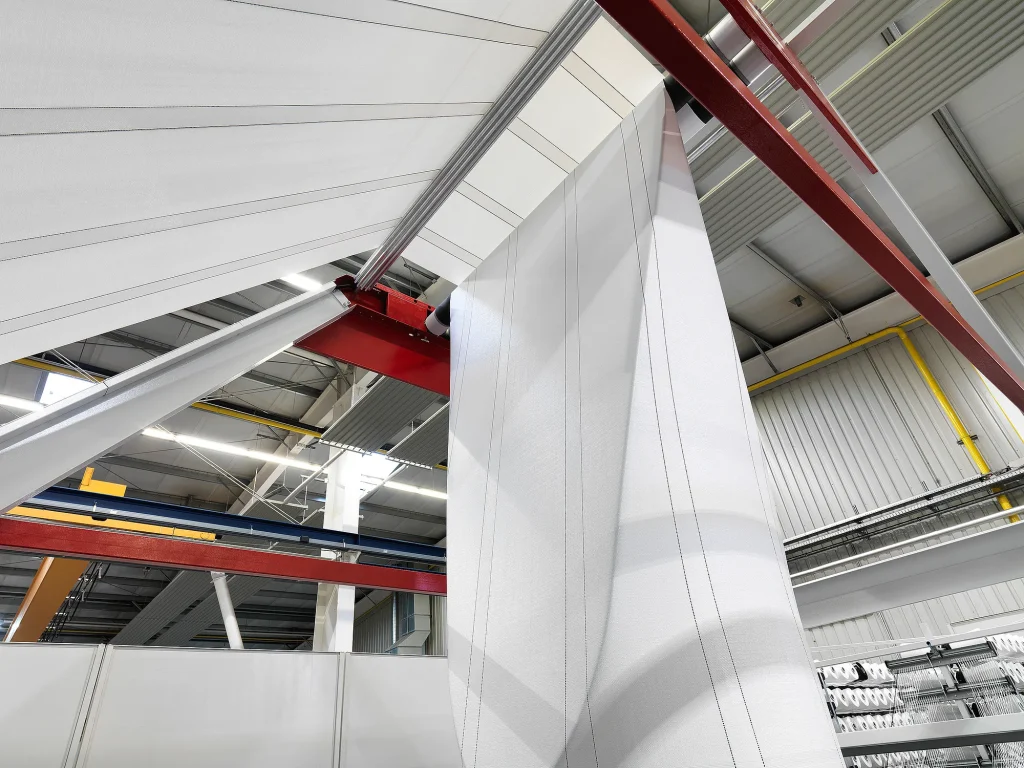
- 1. The Technical Superiority of Open Mouth PP Bags
- 2. Future Trends: Sustainability Meets Smart Design
- 3. VidePak’s Manufacturing Excellence: Precision at Scale
- 4. Customization: Tailoring Solutions for Every Industry
- 5. Market Dynamics: Regional Demand and Brand Strategy
- 6. FAQs: Addressing Critical Client Questions
- 7. The Road Ahead: Innovations on the Horizon
- References
“Can a single packaging solution combine industrial durability, environmental responsibility, and brand-specific customization? The answer is yes—when you leverage the advanced engineering and sustainable material science behind VidePak’s open mouth PP woven bags.” These bags are redefining industries by offering unmatched versatility, with innovations like 100% recyclable polypropylene blends, bio-degradable additives, and hyper-customized designs tailored to niche applications—from agricultural storage to luxury retail packaging.
At VidePak, a global leader in woven bag manufacturing since 2008, we’ve transformed traditional packaging into a strategic asset for clients worldwide. With 568 employees, 100+ Starlinger circular looms, and $80M in annual revenue, our open mouth PP bags are engineered to meet tomorrow’s challenges today. Let’s explore their technical advantages, future trends, and how VidePak’s commitment to quality and sustainability sets us apart.
1. The Technical Superiority of Open Mouth PP Bags
Open mouth PP woven bags, characterized by their wide top openings and reinforced seams, are designed for high-volume filling and optimal product protection. Their success hinges on three pillars:
1.1 Material Innovations: Balancing Strength and Sustainability
- Recyclable PP: VidePak uses virgin polypropylene resin (MFI 4–6 g/10min) that retains 95% of its tensile strength after 7 recycling cycles via Starlinger’s recoSTAR technology.
- Bio-Degradable Additives: Our EcoBlend™ formula integrates oxo-degradable agents, breaking down bags into harmless biomass within 5 years under landfill conditions (ASTM D6954-18 certified).
- Case Study: A Canadian grain supplier reduced landfill waste by 60% using VidePak’s recyclable PP bags, saving $45,000 annually in disposal costs.
1.2 Structural Adaptations for Diverse Industries
Industry | Customization Feature | Performance Metric |
---|---|---|
Agriculture | UV-stabilized fabric (1,500-hour lifespan) | 90% strength retention after 2 years |
Chemicals | Anti-static coating (≤10⁹ Ω surface resistance) | Complies with IEC 61340-5-1 |
Retail | HD 8-color printing (Pantone-matched) | ≤1.5 Delta E color accuracy |
2. Future Trends: Sustainability Meets Smart Design
2.1 Circular Economy and Recycling
- Closed-Loop Systems: VidePak partners with TerraCycle to recover 98% of post-consumer PP waste, converting it into pellets for new bags.
- Carbon-Neutral Production: Our solar-powered factories (2 MW capacity) reduce CO2 emissions by 1,200 tons annually, aligning with the EU Green Deal.
2.2 Bio-Based Materials
- Sugarcane-Derived PP: Piloting 30% bio-content resin, cutting carbon footprint by 40% compared to fossil-based PP (per ISO 14040 LCA).
- Algae-Based Additives: Researching algae-infused PP for marine-degradable bags, targeting a 3-year decomposition in seawater.
2.3 Smart Packaging Integration
- QR Code Tracking: Embedded QR codes linked to blockchain platforms provide real-time data on bag lifespan and recycling history.
- Moisture Sensors: IoT-enabled liners alert users to humidity breaches (≥70% RH) via mobile apps.
3. VidePak’s Manufacturing Excellence: Precision at Scale
3.1 Production Workflow
- Extrusion & Weaving:
- Virgin PP is melted at 230°C in Starlinger extruders, drawn into 0.3 mm filaments.
- AI-powered looms weave 10×10 strands/cm² fabric with ±2% density tolerance.
- Lamination & Coating:
- PE or BOPP layers (0.05–0.2 mm) are applied using W&H laminators, achieving ≤5 g/m²/day WVTR.
- Printing & Finishing:
- 8-color flexographic presses deliver 1200 dpi resolution, resistant to 4,000 Sutherland rub cycles.
3.2 Quality Control Protocols
- In-Line Testing: Laser micrometers monitor fabric thickness (±0.02 mm), while tensile testers validate seam strength (≥350 N/cm).
- Batch Certification: Each lot undergoes 15+ tests, including UV aging (ISO 4892) and microbial resistance (ASTM G21).
4. Customization: Tailoring Solutions for Every Industry
VidePak’s 30+ lamination machines and 16 extrusion lines enable rapid adaptation:
Custom Feature | Technical Specification | Application Example |
---|---|---|
Reinforced Gussets | 4-ply corners, 50 N/cm² tear strength | Construction material transport |
Ventilation Perforations | Laser-cut 5 mm holes, ±0.3 mm precision | Seed storage in tropical climates |
Ergonomic Handles | 300D PP straps, 75 kg load capacity | Retail-ready pet food packaging |
Client Success Story: A European coffee brand boosted shelf appeal with VidePak’s matte-finish, compostable PP bags, increasing sales by 22% in Q1 2024.
5. Market Dynamics: Regional Demand and Brand Strategy
5.1 Asia-Pacific Growth Drivers
- China: 12% annual growth in agricultural PP bag demand, driven by government subsidies for sustainable packaging.
- India: E-commerce logistics fueling 18% CAGR for lightweight, printable open mouth bags.
5.2 VidePak’s Brand Differentiation
While competitors prioritize low-cost mass production, we focus on:
- Long-Term Partnerships: Offering 5-year warranties and co-developing client-specific solutions.
- Certifications: BRCGS, ISO 9001, and Sedex audits ensure ethical, traceable supply chains.
- Case Study: A U.S. organic farm reduced packaging costs by 30% using VidePak’s customized, reusable PP bags for bulk produce.
6. FAQs: Addressing Critical Client Questions
Q1: How does recyclable PP compare in cost to traditional materials?
A: VidePak’s recyclable PP costs $0.12/m² vs. $0.15/m² for non-recyclable alternatives, with 40% lower waste disposal fees.
Q2: Can bags withstand freezer storage?
A: Yes. Our cryogenic PP blend remains flexible at -40°C, ideal for frozen food logistics.
Q3: What’s the minimum order for custom designs?
A: Prototypes start at 1,000 units with 10-day lead times; bulk orders (50,000+) ship in 30 days.
7. The Road Ahead: Innovations on the Horizon
- Self-Healing PP: Microcapsules releasing repair agents upon puncture (lab testing 85% efficacy).
- Edible Coatings: Starch-based liners for zero-waste food packaging (patent pending).
References
- International Woven Bag Association. (2024). Global Market Analysis for PP Packaging.
- ASTM International. (2023). Performance Standards for Degradable Polymers.
- European Commission. (2024). Circular Economy Action Plan Progress Report.
At VidePak, innovation isn’t just a buzzword—it’s woven into every product. Discover our sustainable open mouth bag solutions or explore custom printing capabilities.
From farm to shelf, VidePak’s open mouth PP bags deliver durability, sustainability, and brand impact. Partner with a manufacturer who treats your packaging challenges as their own—because when quality is non-negotiable, the choice is clear.