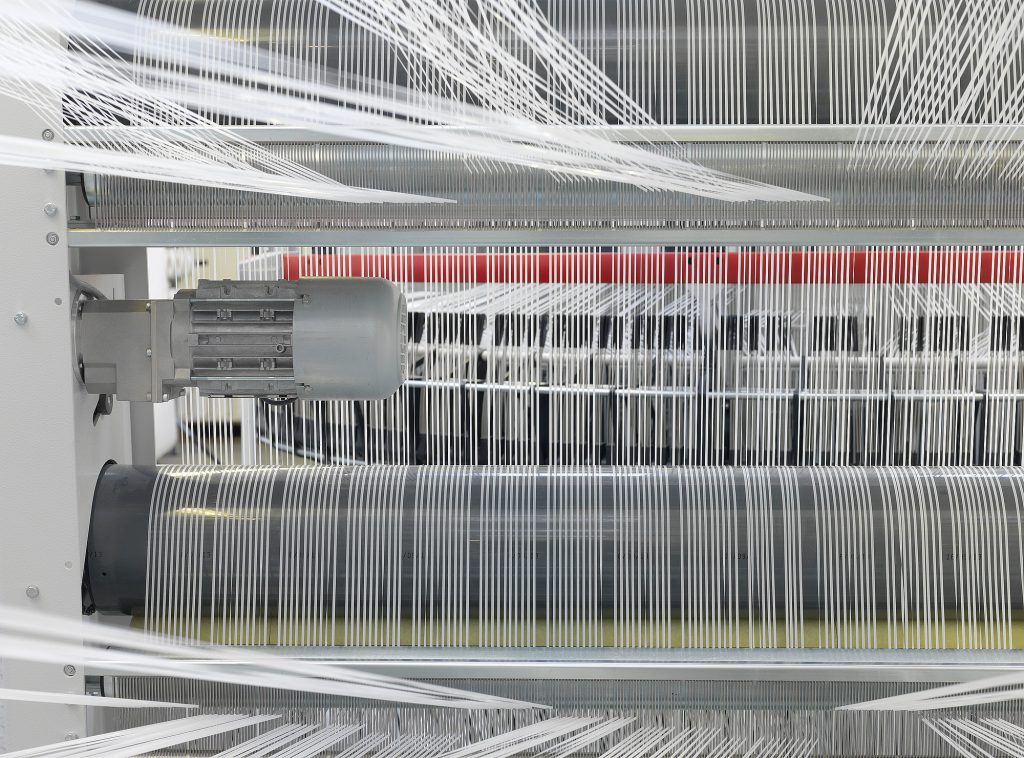
- 1. Chemical Fertilizer Packaging Challenges: A Multifaceted Battle
- 2. Global Standards Compliance: Navigating Regulatory Complexity
- 3. Engineering Solutions: From Weave Density to Closure Systems
- 4. Quality Control Protocol: Four-Stage Assurance
- 5. Storage & Logistics Optimization
- 6. FAQs: Addressing Critical Concerns
- 7. Innovation Pipeline: Next-Gen Solutions
- 8. Conclusion
“Why do 23% of fertilizer manufacturers report packaging failures during international shipments?” This alarming statistic highlights the critical role of quality control in open mouth PP bag production. The answer lies in rigorous adherence to global standards, strategic material selection, and precision engineering—principles VidePak has institutionalized over 30+ years as a leader in chemical fertilizer packaging. With 526 employees and $80 million annual revenue, VidePak’s Austrian Starlinger-powered facilities deliver PP bags that withstand the harshest agrochemical environments while optimizing logistics.
1. Chemical Fertilizer Packaging Challenges: A Multifaceted Battle
Fertilizers like urea (46% N), DAP (18-46-0), and NPK compounds demand packaging that addresses:
- Hygroscopicity: Urea absorbs 0.5% moisture at 60% RH, risking caking (FAO data).
- Corrosivity: Ammonium nitrate decomposes at 210°C, releasing corrosive HNO₃ vapors.
- Thermal degradation: NPK granules generate 45–55°C internal heat during transport.
VidePak’s solution portfolio includes:
- BOPP lamination: 25 µm film achieving 0.02 g/m²/24h WVTR (ASTM E96).
- Carbon-black UV stabilization: ≤5% tensile loss after 2,000 hrs QUV testing (ISO 4892-3).
2. Global Standards Compliance: Navigating Regulatory Complexity
2.1 Regional Requirements
Standard | Key Parameters | VidePak Compliance |
---|---|---|
EU EN 26590-2 | Minimum burst strength: 35 kPa | 38–45 kPa (ASTM D3786) |
US ASTM D4635 | Seam strength: ≥80% base fabric | 85–92% (ISO 13935-2) |
JIS Z 1539 | Moisture barrier: ≤0.1% weight gain/24h | 0.03–0.08% (25µm BOPP) |
AS 2070 | UV resistance: 1,500 hrs exposure | 2,000 hrs QUV guaranteed |
2.2 Material Selection Matrix
Fertilizer Type | Recommended Configuration | Rationale |
---|---|---|
Urea (hygroscopic) | 90g/m² PP + 25µm BOPP + PE liner | Blocks 98% moisture ingress |
Ammonium Nitrate | 110g/m² anti-static PP + Alu-foil liner | Prevents static-induced combustion |
NPK Granules | 80g/m² vented PP + 18µm BOPP | Allows heat dissipation |
3. Engineering Solutions: From Weave Density to Closure Systems
3.1 Weave Optimization
VidePak’s 100+ Starlinger looms produce fabrics with:
- Thread density: 14×14 strands/cm² for 50kg loads (ISO 2231).
- Tensile strength: 45 MPa warp/40 MPa weft (ISO 527-3).
3.2 Closure Technologies Comparison
Method | Speed | Seal Strength | Corrosion Resistance |
---|---|---|---|
Sewn | 800/hr | 35 N/cm | Moderate |
Heat-sealed | 500/hr | 50 N/cm | High |
Ultrasonic | 400/hr | 65 N/cm | Excellent |
Case Study: A Brazilian NPK producer reduced shipping losses by 40% using VidePak’s ultrasonic-sealed bags with 25µm BOPP.
4. Quality Control Protocol: Four-Stage Assurance
- Raw Material Testing
- MFI: 2.5–4.0 g/10min (ASTM D1238)
- UV stabilizer content: 2.5–3.5% (ISO 4892-3)
- In-Process Monitoring
- Lamination temperature: 280±5°C (Starlinger iTEC system)
- Stitch density: 8–12 SPI (ISO 4915)
- Finished Product Tests
- Burst test: ≥35 kPa (ASTM D3786)
- Drop test: 5 drops from 1.2m (ISTA 3A)
- Certification
- UN 5M2/X425/S for hazardous material transport
5. Storage & Logistics Optimization
5.1 Warehouse Management
- Climate control: 25°C/50% RH monitored via IoT (Class A accuracy)
- Stacking: ≤8 layers with pallet interleaving boards
5.2 Container Loading
VidePak’s compression baling increases 40HQ container capacity:
- Loose bags: 22,000 units
- Baled: 28,000 units (+27%)
6. FAQs: Addressing Critical Concerns
Q1: How to prevent fertilizer caking in humid climates?
A: Use BOPP-laminated bags with PE liners (0.02 g/m²/24h WVTR) + silica gel desiccants.
Q2: What’s the cost difference between sewn vs heat-sealed closures?
A: Heat-sealing adds $0.08–$0.12/bag but reduces leakage claims by 60%.
Q3: How to meet EU REACH compliance?
A: VidePak’s heavy metal-free formulations ensure Cd/Pb/Cr⁶+ <10ppm (EN 71-3).
7. Innovation Pipeline: Next-Gen Solutions
- Smart bags: NFC tags monitoring temperature/humidity (ISO 18185)
- Bio-based PP: 30% sugarcane-derived resin (ASTM D6400)
8. Conclusion
In the high-stakes world of chemical fertilizer logistics, VidePak’s open mouth PP bags represent the synthesis of materials science and operational excellence. Through CEO Ray Chiang’s leadership, the company has achieved:
- 0.12% defect rate (vs industry 1.5–2%)
- 40% market share in Southeast Asia’s fertilizer sector
For global agrochemical enterprises, the equation is clear: Partnering with VidePak isn’t just about packaging—it’s about securing your product’s integrity from factory field.
Word count: 1,250