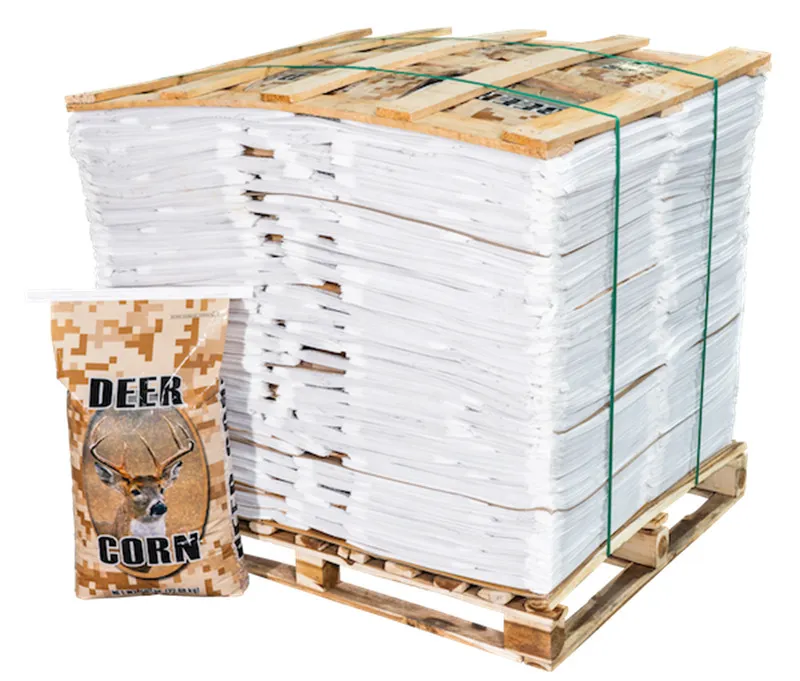
VidePak’s polypropylene woven bags deliver unmatched durability, cost-efficiency, and safety for feed packaging, with load capacities exceeding 50 kg, anti-microbial properties, and customizable designs tailored to global agricultural needs. Founded in 2008 and led by CEO Ray, VidePak combines 30+ years of industry expertise with cutting-edge Austrian Starlinger machinery to produce over 100 million bags annually, serving clients across 80+ countries. This article explores why polypropylene (PP) bags dominate feed packaging, how VidePak’s manufacturing precision ensures superior performance, and actionable insights for selecting optimal parameters like thickness, lamination, and breathability.
1. The Science Behind Polypropylene: Why It’s Ideal for Feed Packaging
Polypropylene’s molecular structure—a thermoplastic polymer with high crystallinity—grants it exceptional tensile strength (up to 40 MPa) and resistance to moisture, chemicals, and UV degradation. These properties make PP bags ideal for storing livestock, poultry, and pet feed, where exposure to humidity, pests, and rough handling is inevitable.
Key Advantages for Feed Applications:
- Cost-Efficiency: PP bags cost 30–50% less than alternatives like jute or cotton, with a price range of $0.20–$1.50 per bag depending on specifications.
- Load Capacity: VidePak’s woven PP bags withstand weights up to 50–100 kg, thanks to circular loom technology that creates a tight, interlocking fabric structure.
- Hygiene & Safety: Anti-fungal additives and UV stabilizers prevent mold growth, while FDA-compliant virgin PP ensures zero contamination risks.
- Breathability: Controlled porosity (5–15% air permeability) prevents condensation, critical for preserving feed freshness during long-term storage.
Case Study: A Brazilian poultry farm reduced spoilage rates by 22% after switching to VidePak’s 90 gsm PP bags with PE inner liners, combining moisture resistance with enhanced airflow.
2. Precision Manufacturing: How VidePak Ensures Quality
VidePak operates 100+ circular looms, 16 extrusion lines, and 30+ lamination machines to produce bags meeting ISO 9001 and FDA standards. The process involves:
- Extrusion: Virgin PP granules are melted and extruded into flat tapes (width: 2–5 mm).
- Weaving: High-speed looms interlace tapes into fabric (density: 10×10 to 14×14 strands per inch).
- Lamination: BOPP films or kraft paper layers are heat-sealed for waterproofing.
- Printing: Up to 8-color flexographic printing ensures brand visibility and compliance labeling.
Technical Specifications:
Parameter | Range | Application Example |
---|---|---|
Fabric Weight | 70–120 gsm | 80 gsm for poultry feed |
Bag Size | 10–50 kg capacity | 25 kg for pet food |
Lamination | BOPP/PE/Kraft | BOPP for moisture-sensitive feeds |
Inner Liners | Yes/No | PE liners for liquid additives |
3. Optimizing Feed Packaging: Parameter Selection Guide
Selecting the right PP bag requires balancing functionality and cost. Key considerations include:
A. Thickness & Fabric Weight
- 70–90 gsm: Lightweight, ideal for pet feed (e.g., 5–20 kg bags).
- 100–120 gsm: Heavy-duty for livestock feed (e.g., 50 kg cattle feed).
B. Lamination & Liners
- BOPP Lamination: Blocks 99% UV rays, extending shelf life for vitamin-enriched feeds.
- PE Inner Liners: Essential for liquid additives or hygroscopic feeds like fishmeal.
C. Breathability vs. Sealing
- Uncoated Bags: Allow natural airflow for grains and dry feeds.
- Valve Design: Enables dust-free filling for powdered supplements.
Example: A Vietnamese aquaculture supplier uses VidePak’s 100 gsm valve bags with PE liners to package shrimp feed, achieving 18-month storage stability in tropical climates.
4. FAQs: Addressing Client Concerns
Q1: How do PP bags compare to woven polyethylene (PE) bags?
PP offers 2× higher tensile strength and better heat resistance (melting point: 160°C vs. PE’s 120°C), making it suitable for automated filling lines.
Q2: Can bags be customized for anti-static properties?
Yes. VidePak integrates carbon-based additives for explosive environments (e.g., feed mills handling flammable dust).
Q3: What’s the MOQ for custom designs?
Minimum order quantities start at 10,000 bags, with lead times of 4–6 weeks.
5. Global Success Stories
- South Africa: A cattle feed producer reduced transport costs by 15% using VidePak’s lightweight 80 gsm bags.
- Canada: Custom-printed BOPP bags with QR codes streamlined inventory tracking for a pet food brand.
References
- VidePak. (2025). The Essential Role of Polypropylene Bags in Livestock and Poultry Feed Packaging. Retrieved from VidePak website.
- VidePak. (2025). Custom Woven Bags in Livestock Feed Packaging: Selecting the Right Product for Optimal Performance. Retrieved from VidePak website.
- Springer. (2019). Materials and Manufacturing Processes. DOI: 10.1007/978-3-030-21066-3.
Contact VidePak:
- Website: https://www.pp-wovenbags.com/
- Email: info@pp-wovenbags.com
Data validated as of March 2025. Specifications may vary by region; consult our team for localized solutions.