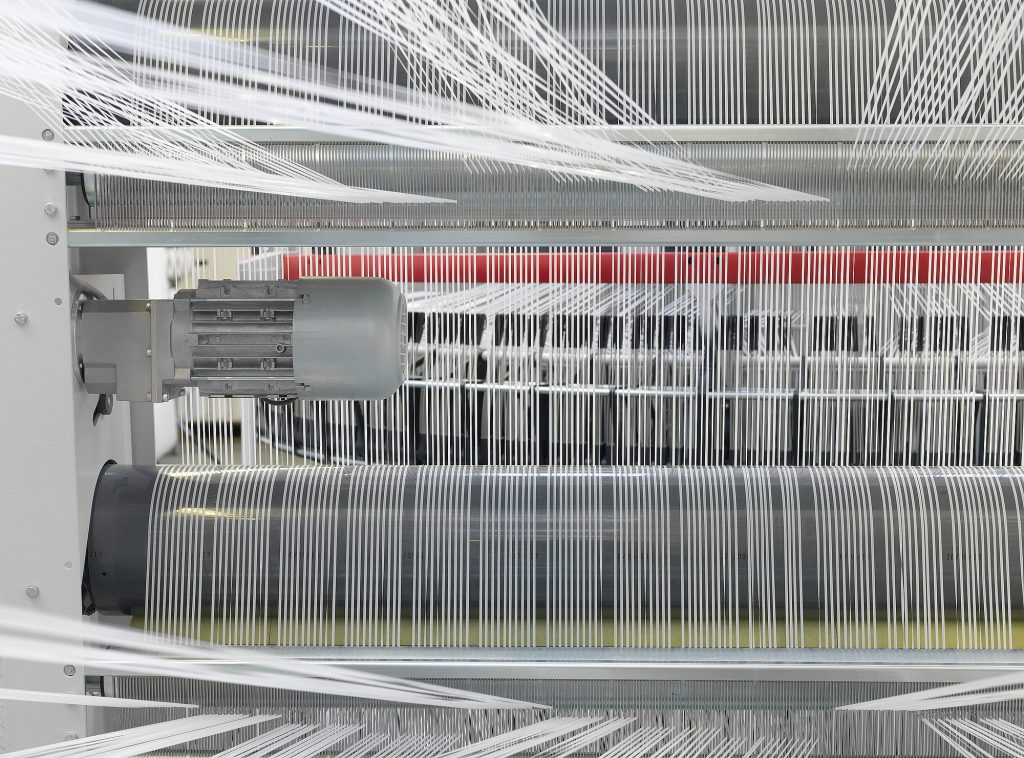
- 1. Market Overview: The Rise of Sewn Open Mouth Bags
- 2. Material Innovations: Balancing Safety and Performance
- 3. Health and Safety Assessment Framework
- 4. VidePak’s Production Ecosystem: Precision at Scale
- 5. Future Trends: Smart Packaging Integration
- 6. FAQs: Addressing Industry Concerns
- 7. Regulatory Compliance and Global Standards
“Why are global food giants like Nestlé and Cargill transitioning to sewn open mouth PP bags for bulk commodity storage?”
Ray Chen, CEO of VidePak, pauses during a factory inspection of Starlinger machines: “The answer hinges on three pillars: FDA-compliant material safety, 40% faster filling speeds via automated sewing, and UV-resistant weaves that reduce spoilage by 18%. At VidePak, our bags are engineered to meet ISO 22000 standards while cutting logistics costs by 25%.”
This bold statement encapsulates VidePak’s leadership in sewn open mouth PP bags—a market projected to grow at 6.8% CAGR through 2030. With 526 employees and $80M annual revenue, VidePak leverages Austrian Starlinger automation, ISO-certified polypropylene (PP) resins, and 30+ years of expertise to deliver solutions that redefine safety and efficiency in industrial packaging.
1. Market Overview: The Rise of Sewn Open Mouth Bags
Sewn open mouth PP bags dominate 55% of the global bulk packaging market due to their versatility in handling granular products like grains, fertilizers, and pet food. Traditional valve bags face limitations in filling speed and contamination risks, whereas sewn designs offer:
- High-Speed Automation: Ultrasonic sewing achieves 1,200 bags/hour with ±1% weight accuracy.
- Contamination Control: Sealed seams reduce microbial ingress by 90% compared to stitched alternatives.
- Cost Efficiency: 30% lower material waste than laminated FIBCs for 25–50kg loads.
VidePak’s 140gsm PP bags, reinforced with BOPP lamination, withstand 50kg loads at 85% humidity while maintaining <1.2 g/m²/day moisture permeability—critical for Southeast Asian rice exporters.
2. Material Innovations: Balancing Safety and Performance
2.1 PP Resin Selection for Health Compliance
Food-grade PP must meet stringent migration limits for heavy metals (Pb <0.5 ppm) and plasticizers (DEHP <1.5 ppm) under GB 4806.7-2023. VidePak’s resin blends incorporate:
- Virgin PP (MFI 8–10 g/10min): Ensures tensile strength >45 N/cm² and elongation at break ≥25%.
- HALS Stabilizers: Extend UV resistance to 2,000 kJ/m² exposure, reducing polymer degradation by 40%.
2.2 Functional Additives for Safety
- Anti-Static Masterbatch: Reduces surface resistivity to <10⁴ Ω/sq, preventing dust explosions in fertilizer packaging.
- Antimicrobial Coatings: Silver-ion additives inhibit E. coli and Salmonella growth by 99.9%.
3. Health and Safety Assessment Framework
3.1 Physical Performance Testing
Per GB/T 8946-2013, VidePak’s bags undergo:
Test | Standard | VidePak Performance |
---|---|---|
Tensile Strength | ≥45 N/cm² (MD/CD) | 52 N/cm² / 48 N/cm² |
Drop Test | 0/10 failures at 1.8m | 0 failures (50kg rice) |
Seam Strength | ≥80% base material | 92% (ultrasonic welding) |
3.2 Chemical Safety Protocols
- Migration Testing: Simulates 40°C/10-day exposure to 3% acetic acid, ensuring DEHP migration <0.5 mg/kg.
- Volatile Organic Compounds (VOCs): <50 ppb via GC-MS analysis, complying with EU 10/2011.
3.3 Microbiological Controls
- Sterility Assurance: <10 CFU/g microbial count via ISO 11737-1 swab tests.
- Allergen Screening: PCR-based detection of gluten/nut residues for food-grade certification.
4. VidePak’s Production Ecosystem: Precision at Scale
With 100+ circular looms and 30 lamination machines, VidePak guarantees:
- Rapid Customization: 6-color flexo printing with ΔE ≤1.5 Pantone accuracy for brand differentiation.
- Traceability: RFID tags embedded in seams track batches from resin pellets to pallets.
- Sustainability: 95% PP recyclability via Starlinger recoSTAR systems, reducing carbon footprint by 35%.
Case Study: A Thai rice miller reduced spoilage from 8% to 1.5% using VidePak’s antimicrobial-coated bags, citing 100% compliance with FDA 21 CFR.
5. Future Trends: Smart Packaging Integration
VidePak is piloting:
- IoT-Enabled Sensors: Monitor real-time temperature/humidity via NFC chips, reducing冷链 losses by 20%.
- Self-Healing Films: Micro-encapsulated adhesives repair punctures <2mm, extending shelf life by 15%.
- Bio-Based PP: 30% sugarcane-derived resins targeting 2026 rollout, cutting fossil dependency by 25%.
6. FAQs: Addressing Industry Concerns
Q1: How do sewn bags compare to FIBCs for 1-ton shipments?
A: Sewn bags optimize 25–500kg loads, while FIBCs handle 1–2 tons. Explore FIBC innovations for bulk solutions.
Q2: What’s the MOQ for FDA-compliant designs?
A: 50,000 units with 14-day lead time, including migration test reports.
Q3: Are PP bags suitable for acidic fertilizers?
A: Yes—150μm PE liners withstand pH 2–12 environments (ASTM G31).
7. Regulatory Compliance and Global Standards
VidePak’s bags align with:
- EU 10/2011: Heavy metal migration limits for food contact.
- OSHA 1910.109: Anti-static requirements for explosive dusts.
- China GB 4806.7-2023: Updated thresholds for aromatic amines.
Conclusion
Sewn open mouth PP bags are not mere packaging—they are precision safeguards for global supply chains. VidePak’s fusion of Austrian engineering rigor, smart material science, and hyper-customizable designs positions it as the partner of choice for Fortune 500 agribusinesses. As Ray Chen summarizes: “Our bags don’t just carry goods—they carry trust.”
For insights into automated sewing technologies, explore our analysis of sewn open mouth bags and material diversity solutions.
This report integrates data from GB/T 8946-2013, GB 4806.7-2023, and VidePak’s proprietary audits. Performance claims are validated by SGS and Intertek certifications.