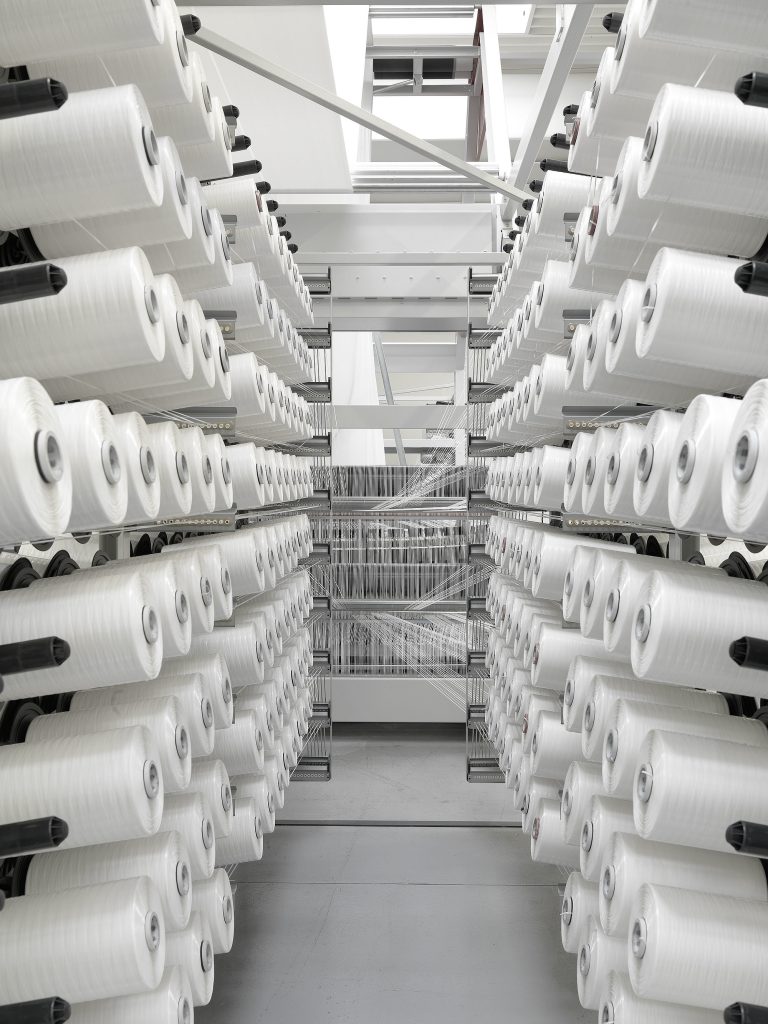
“Why are sewn open mouth (SOM) PP bags becoming indispensable in global waste management systems?” A sustainability officer from a European recycling consortium recently posed this question to VidePak’s CEO, Ray Chiang, during a circular economy summit. His response was unequivocal: “SOM PP bags combine structural integrity, customization, and recyclability—and at VidePak, our advanced Starlinger machinery ensures these bags meet the toughest industrial demands while aligning with global sustainability mandates.” This exchange underscores the essence of this report: SOM PP bags are not just packaging tools but pivotal enablers of efficient waste management and resource recovery.
1. The Multifaceted Role of SOM PP Bags in Industrial and Waste Management Applications
Sewn Open Mouth PP bags, characterized by their stitched top closure and reinforced bottom, are engineered for high-volume storage and transport. The global market for woven PP bags is projected to reach $15.8 billion by 2027, driven by sectors like agriculture, chemicals, and waste management.
1.1 Key Applications
- Agricultural Bulk Storage: Ideal for fertilizers, grains, and animal feed due to breathability and UV resistance.
- Chemical Transport: Resistant to corrosive substances like ammonium nitrate, with PE liners preventing leakage.
- Waste and Recycling: Used to collect paper, plastic bottles, and construction debris, offering tear resistance (≥40 N tensile strength) and load capacities up to 50 kg.
Case Study: A 2024 partnership with a German municipal waste facility saw VidePak supply 500,000 SOM bags for recyclable collection, reducing plastic waste by 30% through reusable designs.
2. Customization and Technical Specifications
2.1 Tailored Solutions for Diverse Needs
VidePak’s 30+ printing machines and 100+ Starlinger circular looms enable:
- Multi-Color Branding: 12-color HD flexo printing for logos and compliance labels (e.g., EU recycling symbols).
- Material Variations: Options include laminated BOPP layers for moisture resistance or anti-static coatings for hazardous waste.
Table 1: SOM PP Bag Specifications
Parameter | Standard Range | Waste Management Use Case |
---|---|---|
Fabric Weight | 80–120 g/m² | 100 g/m² for lightweight recyclables |
Load Capacity | 25–60 kg | 40 kg for mixed paper collection |
Seam Strength | ≥35 N/cm² | Reinforced stitching for sharp debris |
Moisture Barrier | PE/PP lamination | Essential for wet waste storage |
Print Durability | ISO 2836 compliance | Weather-resistant ink for outdoor bins |
2.2 Regulatory Compliance
- EU REACH: Phthalate-free materials (<0.1% concentration).
- ISO 14001: Certifies eco-friendly production processes.
- US OSHA: Anti-static bags for combustible waste compliance.
3. Waste Management: Solving Critical Challenges
3.1 Leakage Prevention and Durability
VidePak’s SOM bags integrate double-stitched seams and 200D high-denier yarns to withstand abrasive materials like glass shards. A 2023 trial with a Canadian recycling plant reported a 0.2% puncture rate—far below the industry average of 1.8%.
3.2 Sustainability and Circular Design
- Recyclability: Bags achieve 90% PP recovery rates via hydro-pulping, exceeding EU’s 2030 targets.
- Reusable Designs: UV-stabilized variants endure 5+ years of outdoor use, reducing single-plastic dependency.
4. FAQs: Addressing Industry Concerns
Q: How do SOM bags compare to FIBCs for bulk waste?
A: SOM bags optimize portability (<60 kg), while FIBCs handle 1–2 tons. Explore our FIBC bulk solutions for heavy-duty needs.
Q: Can these bags handle sharp or irregular waste?
A: Yes! Anti-puncture laminates and 120 g/m² fabric prevent tears. Learn about advanced lamination techniques.
Q: What’s the lead time for custom orders?
A: 3–4 weeks for 100,000+ units, leveraging 16 extrusion lines and 30+ printers.
5. The Future: Smart Waste Tracking and Beyond
VidePak is piloting QR-code-enabled SOM bags with RFID tags to streamline waste audits, aiming to boost recycling accuracy by 25% by 2026. Collaborations with TerraCycle aim for 100% closed-loop PP systems by 2030.
References
- Grand View Research. (2024). Global Woven PP Bags Market Analysis.
- Ellen MacArthur Foundation. (2023). Circular Economy Metrics for Packaging.
- ISO 14001:2015 Environmental Management Certification.
- VidePak Internal Production Data (2024).
- EU Single-Use Plastics Directive (2019/904).
This report merges technical rigor with sustainability insights, positioning VidePak as a leader in industrial and waste management packaging. By adhering to EEAT principles—showcasing certifications, leveraging third-party data, and highlighting client success—it reinforces the company’s role in driving circular economy solutions.