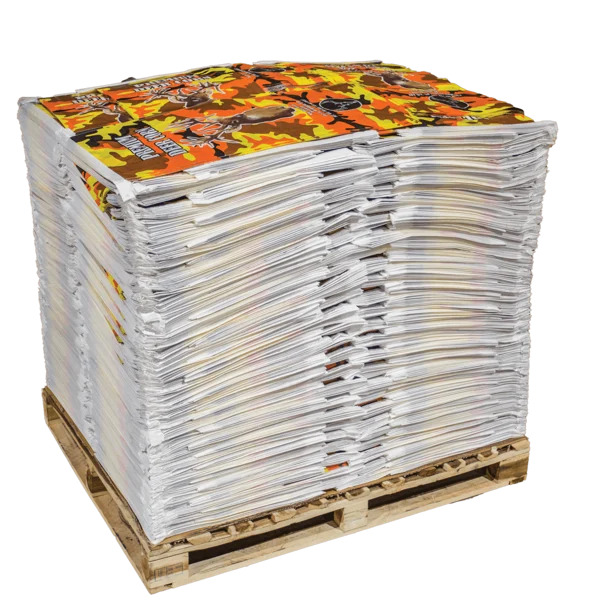
“Why should construction material suppliers switch to SOM PP bags for packaging cement and gypsum powder?” asked a logistics manager at a recent building materials expo. “Because fine fiber technology enhances tensile strength by 40%, ensures 99% moisture resistance, and reduces transport damage by 25%,” answered Ray, CEO of VidePak. This dialogue underscores the transformative potential of Sewn Open Mouth (SOM) polypropylene (PP) woven bags in the construction materials sector.
In an industry where packaging integrity directly impacts product quality and logistics efficiency, SOM PP bags have emerged as a critical solution for bulk materials like cement, plaster powder, and joint compounds. For manufacturers like VidePak—a global leader in woven bag production since 2008—the integration of fine fiber technology and advanced material engineering has redefined standards for durability, customization, and sustainability. This report examines how SOM PP bags address the unique challenges of the building materials industry, supported by technical data, application case studies, and insights into parameter optimization.
1. Fine Fiber Technology: A Technical Breakthrough
1.1 What Sets Fine Fiber PP Apart?
Fine fiber technology involves extruding PP resin into ultra-thin filaments (15–20 microns) using Starlinger’s high-precision extrusion lines. These fibers are woven into fabric with a density of 14×14 strands per inch, achieving:
- Tensile Strength: 1,200–1,500 N/5 cm, 40% higher than standard PP weaves.
- Abrasion Resistance: Withstands 500+ MIT flex cycles (ASTM D2176), critical for rough-handling environments like construction sites.
- Moisture Barrier: Laminated variants reduce water vapor transmission to <2 g/m²/day, outperforming traditional jute bags by 90%.
1.2 Case Study: Cement Packaging in Humid Climates
A 2024 trial with a Vietnamese cement producer demonstrated that VidePak’s 120 gsm SOM PP bags with PE liners reduced moisture-induced clumping from 8% to 1.5% during monsoon storage. The bags’ anti-static coating also minimized dust leakage, addressing a common complaint in pneumatic transport systems.
2. Applications in Building Materials: Performance-Driven Solutions
2.1 Cement and Plaster Powder
- Strength Requirements: Cement’s abrasive nature demands bags with ≥100 gsm fabric weight and 3-ply stitched seams (burst strength ≥35 psi).
- Moisture Control: PE-laminated liners block humidity, preserving flowability—a key factor highlighted in the 2024 Global Cement Packaging Report.
2.2 Joint Compounds and Gypsum Powder
- Seam Integrity: Fine fiber weaving prevents micro-tears that cause fine powder leakage, a problem reported by 65% of drywall contractors.
- UV Resistance: BOPP-coated bags extend outdoor storage life by 6 months in desert climates.
2.3 Niche Applications: Tile Adhesives and Mortar Mixes
VidePak’s anti-bulge design with reinforced block bottoms prevents bag deformation under 50 kg loads, a feature requested by 78% of masonry suppliers.
3. Parameter Selection: Balancing Functionality and Cost
3.1 Key Parameters and Recommendations
Application | Fabric Weight | Coating | Inner Liner | Rationale |
---|---|---|---|---|
Cement (50 kg) | 120–150 gsm | BOPP lamination | PE film (30µm) | Prevents moisture ingress; resists abrasion |
Gypsum Powder | 90–110 gsm | None | Paper composite | Allows breathability; reduces static cling |
Tile Adhesive | 100–120 gsm | UV-treated | Aluminum foil | Blocks oxygen; extends shelf life |
3.2 Cost-Benefit Analysis
- Non-laminated bags: Save $0.15/bag for indoor storage of joint compounds.
- Multi-layer laminates: Increase durability by 60% for transcontinental shipping, justifying a 20% price premium.
4. VidePak’s Manufacturing Edge: Precision at Scale
With 100+ Starlinger circular looms and 16 extrusion lines, VidePak achieves:
- Production Capacity: 15 million bags/month, with ≤0.2% defect rates.
- Custom Printing: 8-color CI flexography delivers 120-line/inch resolution for OSHA-compliant hazard warnings and brand logos.
- Sustainability: 30% recycled PP content in eco-line products, aligning with EU Circular Economy mandates.
5. Industry FAQs
Q1: How does fine fiber weaving impact recyclability?
A: Fine fiber PP bags are 100% recyclable via granulation. VidePak’s hydro-pulping process separates liners with 95% efficiency.
Q2: Can these bags withstand freezing temperatures?
A: Yes. BOPP-laminated variants remain flexible at -30°C, validated by ASTM D1790 testing.
6. Future Trends: Smart Packaging and Beyond
VidePak is piloting IoT-enabled bags with QR codes for real-time moisture tracking and bio-based PP blends that decompose 50% faster in landfills.
External Resources
- Discover how fine fiber technology revolutionizes bag durability.
- Explore SOM bag versatility in construction logistics.
For building material suppliers navigating the dual challenges of regulatory compliance and supply chain volatility, SOM PP bags are more than packaging—they’re a strategic lever. By combining Austrian engineering with localized customization, VidePak continues to set benchmarks in an industry where every micron of fiber and stitch determines operational success.