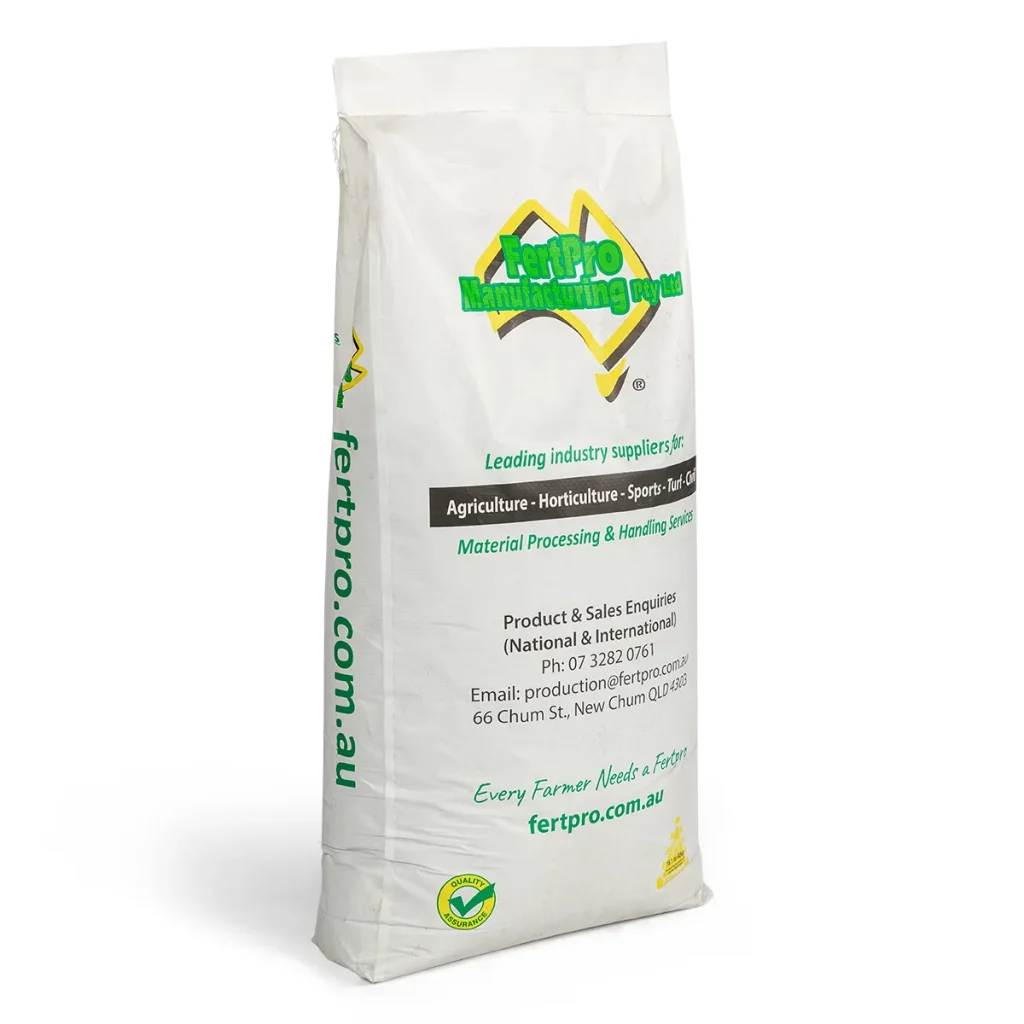
Sewn Open Mouth (SOM) bags have become increasingly popular in various industries due to their versatility, durability, and cost-effectiveness. These bags are especially valued in packaging applications, as they can accommodate a wide range of products, from agricultural goods to chemicals. In this blog post, we will delve into the characteristics of SOM PP Fabric Bags and explore the different materials used in woven bag production, including their manufacturing processes, with a particular emphasis on the co-extrusion blow molding technology.
Understanding SOM PP Fabric Bags
SOM PP Fabric Bags, also known as Sewn Open Mouth Bags, are designed to hold various types of bulk products. These bags are constructed primarily from polypropylene (PP) fabric, which provides several advantageous properties:
- Durability: The strength of PP fabric makes SOM bags highly resistant to tearing and puncturing, making them suitable for heavy loads.
- Lightweight: Despite their strength, these bags are lightweight, which can reduce transportation costs.
- Moisture Resistance: The inherent properties of polypropylene make SOM bags resistant to moisture, which is crucial for protecting the contents during storage and transit.
- Customization: SOM bags can be tailored in terms of size, thickness, and printing, allowing businesses to promote their brands effectively.
- Cost-Effectiveness: With a relatively low production cost, SOM bags are a budget-friendly option for many businesses.
Materials Used in SOM Bags
While the primary material for SOM bags is polypropylene, various other materials can be used in the production of woven bags, each offering distinct properties and advantages. Here’s an overview of some common materials:
Material | Description | Common Applications |
---|---|---|
Polypropylene (PP) | A thermoplastic polymer known for its strength, moisture resistance, and lightweight properties. | Agricultural products, chemicals, pet food |
Polyethylene (PE) | A versatile plastic that offers good flexibility, impact resistance, and moisture barrier properties. | Food packaging, industrial products |
PVC (Polyvinyl Chloride) | A durable and weather-resistant material that can be rigid or flexible. | Construction materials, outdoor applications |
Aluminum Foil | A thin sheet of aluminum that provides excellent barrier properties against moisture and gases. | Food packaging, chemical products |
Advantages of Using Different Materials
- Polypropylene (PP): This is the most commonly used material for SOM bags due to its exceptional strength-to-weight ratio, making it ideal for heavy-duty applications.
- Polyethylene (PE): Often used in conjunction with PP, PE enhances moisture barrier properties, making it suitable for products sensitive to humidity.
- PVC: While not as commonly used in bags, PVC can be beneficial for products that require increased durability and resistance to weather elements.
- Aluminum Foil: This material is ideal for applications requiring a high level of protection against moisture and oxygen, which is critical for food and sensitive chemicals.
The Manufacturing Process of SOM Bags
The production of SOM bags involves several steps, each critical to ensuring the final product meets the required specifications. Below are the key stages in the manufacturing process:
- Material Selection: Choosing the right material is essential. Factors such as the type of product being packaged and environmental considerations play a significant role in this decision.
- Weaving: The selected polypropylene fibers are woven together to create a fabric. This fabric forms the basis of the SOM bags and is known for its strength and durability.
- Co-Extrusion Blow Molding: This innovative technology is often employed to enhance the barrier properties of the bags. Co-extrusion involves the simultaneous extrusion of multiple layers of different materials to create a single film. This process allows for the combination of the best features of various materials, resulting in bags that are strong, lightweight, and moisture-resistant.
- Benefits of Co-Extrusion:
- Improved Barrier Properties: By incorporating multiple layers, co-extruded films can provide superior protection against moisture, oxygen, and light.
- Customization: Different layers can be tailored to meet specific requirements, such as transparency, color, or enhanced strength.
- Cost-Effectiveness: The process allows manufacturers to optimize material usage, leading to lower production costs.
- Cutting and Sewing: The woven fabric is then cut into the desired size and sewn into bags. The open mouth design allows for easy filling, making them suitable for various products.
- Printing: Many manufacturers choose to print branding or product information directly onto the bags. High-quality printing techniques ensure that the designs are durable and resistant to fading.
- Quality Control: Before packaging, each batch of SOM bags undergoes rigorous quality control testing. This includes checking for defects, ensuring dimensions are accurate, and verifying that the bags meet industry standards.
- Packaging and Distribution: Once quality checks are completed, the bags are packaged and prepared for distribution to clients.
Applications of SOM PP Fabric Bags
SOM PP Fabric Bags find extensive use across various industries, including:
- Agriculture: Used for packaging seeds, fertilizers, and grains, these bags protect products from moisture and pests.
- Construction: Ideal for holding materials such as sand, gravel, and other bulk construction products.
- Food Industry: They are often employed in packaging pet food, animal feed, and other non-perishable food items.
- Chemical Industry: Used for safely transporting and storing chemicals, powders, and granules.
Conclusion
SOM PP Fabric Bags are an excellent choice for businesses looking for a robust, lightweight, and cost-effective packaging solution. The versatility of materials used in their production, coupled with advanced manufacturing processes like co-extrusion blow molding, allows for customized solutions that meet specific industry requirements. As the demand for sustainable and efficient packaging continues to grow, understanding the characteristics and applications of these bags will help businesses make informed decisions that enhance their product offerings and brand visibility.
By working with experienced woven bag manufacturers, companies can ensure they select the right type of SOM bags tailored to their unique needs, ultimately enhancing their operational efficiency and customer satisfaction.