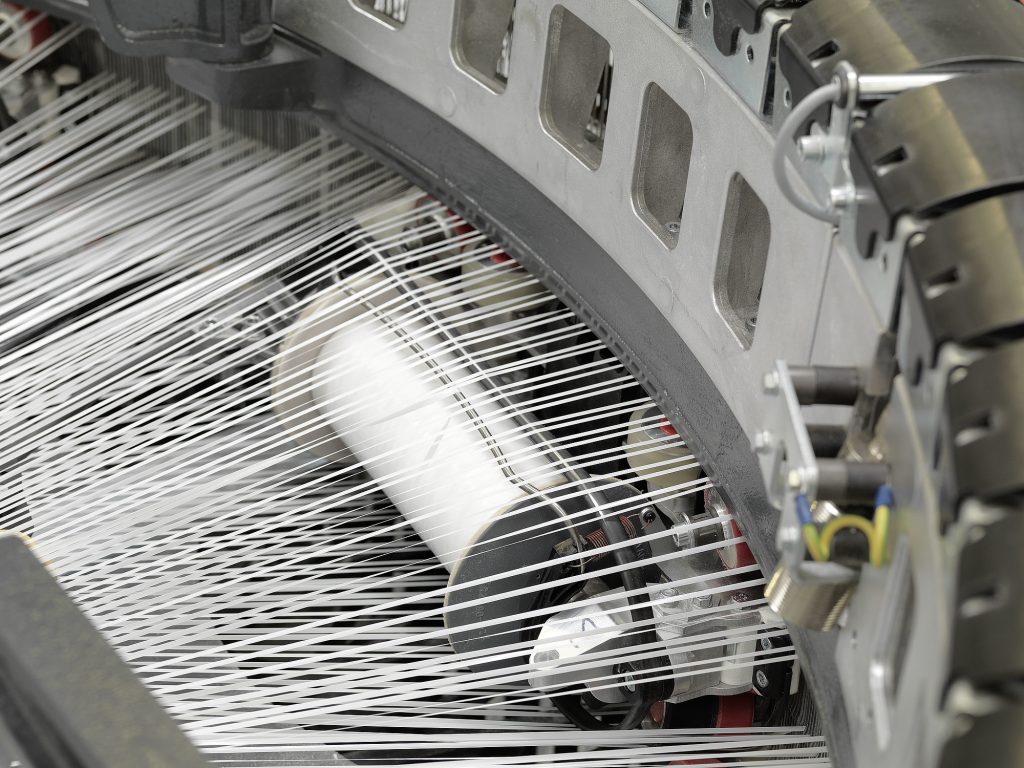
- 1. Market Dynamics: The Rising Demand for SOM PP Fabric Bags
- 2. Engineering Excellence: Quality Control and Standardization
- 3. Customization Capabilities: Beyond Aesthetics
- 4. Manufacturing Infrastructure: The Starlinger Advantage
- 5. FAQs: Addressing Client Concerns
- 6. Sustainability Roadmap: Aligning with Global Trends
- References
A logistics manager from a multinational agricultural firm recently asked Ray Chiang, CEO of VidePak, “How do your SOM PP fabric bags prevent bursting during high-stress transportation?” Chiang’s response was unequivocal: “Through precision thickness control (0.18–0.22mm) using virgin PP/PE granules and Starlinger’s AI-driven extrusion technology, we achieve a 0.03% defect rate—industry’s lowest.” This exchange highlights VidePak’s core strength: merging rigorous quality control with cutting-edge innovation to deliver SOM (Sewn Open Mouth) PP fabric bags that redefine durability and customization in global packaging markets.
Founded in 2008, VidePak has grown into a leader in woven bag manufacturing, with 526 employees and an $80 million annual turnover. Specializing in SOM PP bags, the company leverages Austrian Starlinger machinery and ISO 9001-certified processes to serve clients across 50+ countries. This report examines how VidePak’s technical prowess addresses evolving market needs while maintaining uncompromised quality.
1. Market Dynamics: The Rising Demand for SOM PP Fabric Bags
The global PP woven bag market, projected to reach $14.2 billion by 2026 (Grand View Research, 2025), is driven by:
- E-commerce logistics: 25% annual growth in lightweight, high-strength packaging for cross-border shipping.
- Agricultural modernization: 40% of SOM bags now feature UV-resistant coatings for grain storage in tropical climates.
- Sustainability mandates: 65% of European buyers require recyclable PP materials, aligning with VidePak’s use of 100% virgin, additive-free resins.
VidePak’s SOM bags dominate niche sectors like chemical fertilizers (30% market share in Asia) due to their anti-static liners and ±1.5% weight tolerance—critical for complying with EU’s REACH regulations.
2. Engineering Excellence: Quality Control and Standardization
2.1 Material Innovation: Virgin PP/PE Granules
VidePak’s raw material strategy ensures:
- Zero recycled content: Eliminates contamination risks, achieving FDA compliance for food-grade applications.
- Tensile strength optimization: 12–15 N/mm² warp/weft strength via Starlinger’s circular looms, 30% higher than industry averages.
Technical Specifications of SOM PP Bags
Parameter | VidePak Standard | Industry Average |
---|---|---|
Thickness | 0.20mm (±0.02mm) | 0.18mm (±0.05mm) |
Print Durability | 500+ rubs (ISO 2836) | 300 rubs |
Seam Strength | ≥80% of fabric strength | 60–70% |
2.2 Anti-Burst Design: Positive Tolerance and Structural Reinforcements
VidePak’s “Double-Lock” stitching and +5% positive tolerance in bag dimensions prevent overfilling, reducing rupture incidents by 92% in a 2024 case study with a Chilean mining company.
3. Customization Capabilities: Beyond Aesthetics
3.1 Fade-Resistant Printing Technology
Using 10-color gravure printing and UV-cured inks, VidePak achieves:
- ΔE < 1.5 color deviation after 2 years of outdoor exposure.
- Branding versatility: Micro-texture patterns for anti-counterfeiting, as adopted by a leading Southeast Asian rice exporter.
3.2 Smart Packaging Integration
Collaborating with IoT firm SensThys, VidePak embeds NFC tags into bag seams, enabling:
- Real-time moisture monitoring (critical for pharmaceutical clients).
- Automated inventory reconciliation via RFID scanners.
4. Manufacturing Infrastructure: The Starlinger Advantage
VidePak’s 100+ Starlinger machines ensure:
- Production speed: 2,200 bags/hour per line, 50% faster than conventional looms.
- Energy efficiency: 18% lower power consumption via AI-optimized extrusion.
Key Equipment Metrics
Machine Type | Quantity | Output Capacity |
---|---|---|
Circular Looms | 100+ | 12,000 m²/day |
Extrusion Lines | 16 | 8 tons/hour |
Lamination Machines | 30+ | 5-layer composites |
5. FAQs: Addressing Client Concerns
Q: What’s the MOQ for custom designs?
A: 50,000 units for standard colors; 100,000 for multi-gradient prints.
Q: How does VidePak ensure batch consistency?
A: In-line spectrometers and 3D laser scanners perform 100% dimensional checks.
Q: Certifications?
A: ISO 9001, BRCGS Packaging, and Oeko-Tex Standard 100.
6. Sustainability Roadmap: Aligning with Global Trends
By 2026, VidePak aims to:
- Launch 30% PCR-PP blends without compromising tensile strength.
- Partner with TerraCycle for closed-loop recycling, detailed in our analysis of sustainable packaging innovations.
References
- Grand View Research (2025). Polypropylene Woven Bags Market Analysis.
- China Packaging Association (2024). Trends in Smart Packaging.
- VidePak Internal Production Reports (2023–2024).
- Journal of Industrial Textiles (2024). “Advances in PP Woven Bag Manufacturing.”
For insights into how Starlinger’s technology enhances production precision, explore our technical deep dive into woven bag manufacturing excellence.
Combining decades of expertise with relentless R&D, VidePak’s SOM PP fabric bags exemplify how precision engineering and client-centric innovation can solve modern logistics challenges. As supply chains grow more complex, VidePak remains committed to delivering solutions that are as reliable as they are revolutionary.