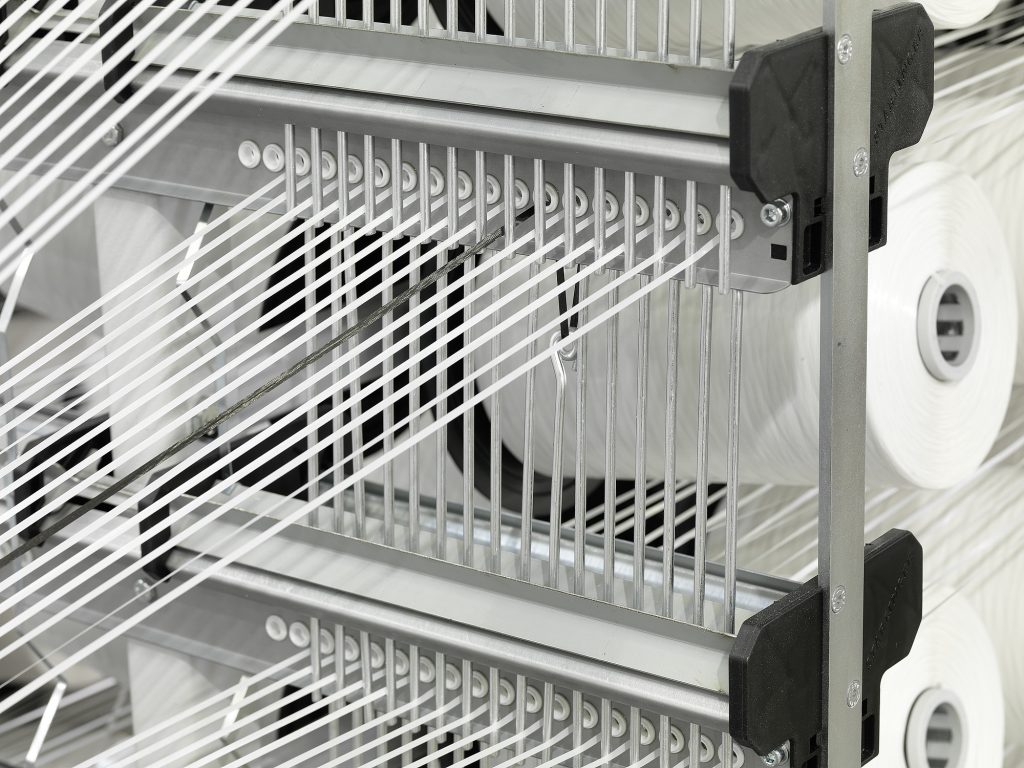
- Introduction: The Rising Significance of SOS PP Fabric Bags
- Mastering Key Production Variables: Pulling Temperature & Drawing Ratio
- Design and Style for Diverse Industries
- Technical Parameters and Options
- FAQs
- Step-by-Step Guide: Producing SOS PP Fabric Bags
- Staying Ahead: Trends and Innovations
- External Links
- Conclusion
Introduction: The Rising Significance of SOS PP Fabric Bags
SOS PP Fabric Bags—short for “Self-Opening Style” polypropylene fabric bags—are winning the attention of businesses across agriculture, construction, and retail. This surge in popularity stems from:
- Extraordinary Durability: Woven PP ensures enhanced load capacity, tear resistance, and longevity.
- Aesthetic Possibilities: Intricate color stripes, high-quality printing, and brand-level customization all elevate visual appeal.
- Eco-Conscious Approaches: Recyclable PP meets growing demands for sustainable, reusable packaging.
According to recent papers and global packaging journals, the trend toward reusability and brand-oriented packaging is forecasted to continue. Consequently, advanced weaving processes, refined finishing options, and next-generation equipment (e.g., Starlinger and W&H lines) are vital in controlling key production parameters—namely pulling temperature and drawing ratio. These factors set the standard for consistent quality.
Mastering Key Production Variables: Pulling Temperature & Drawing Ratio
1. Pulling Temperature Control
- Definition: Manages the heat applied during PP tape extrusion.
- Why It’s Critical:
- Structural Stability: Optimally heated filaments display consistent thickness and robust crystallinity.
- Reduced Defect Rates: Proper temperatures reduce micro-cracks, minimizing tears or “thin spots.”
2. Drawing Ratio
- Definition: The degree to which extruded tapes are stretched.
- Significance:
- Enhanced Tensile Strength: Higher stretch produces stronger tapes, ideal for heavy loads.
- Weight Efficiency: Balanced drawing ratio lowers material usage without sacrificing performance.
3. Machinery Excellence: Starlinger & W&H
VidePak relies on Austrian Starlinger and German W&H machines for weaving and lamination, both revered for:
- Real-Time Adjustments: Synchronized pulling and drawing speed.
- Automated Monitoring: Digital controls detect anomalies, safeguarding tape uniformity.
- High Throughput: Boosted productivity with minimal downtime or defects.
Design and Style for Diverse Industries
- Agriculture & Grain Packaging
- Ventilated Weaving: Lightweight weaves to allow airflow and prevent spoilage.
- Color-Coded Stripes: Blue or green stripes for quick warehouse identification.
- Construction Materials
- Heavy-Duty Reinforcement: Premium gsm (grams per square meter) to hold cement, sand, or gravel.
- Anti-Slip Coatings: Ideal for safe stacking and transportation.
- Retail & Bulk Consumer Goods
- High-Impact Printing: Full-color or offset printing for brand logos, product info, or promotional messages.
- Compact Storage: Foldable format for easy shelving or repeated usage by consumers.
- Sensitive Products
- Antimicrobial Layers: Inhibits bacterial growth for pharmaceuticals or medical supplies.
- Anti-Static Treatments: Protects electronic components from electrostatic discharge.
Technical Parameters and Options
Parameter | Common Range | Impact on Performance |
---|---|---|
Fabric Weight | 60–120 gsm | Balances cost-efficiency with load capacity. |
Weave Density | 8×8, 10×10, or 12×12 | Determines bag strength and tear resistance. |
Pulling Temperature | ~160–180°C | Ensures uniform tape formation and crystallinity. |
Drawing Ratio | 5–8× | Influences elasticity, tensile strength, and final bag weight. |
Printing Format | CMYK, Pantone, RAL | Allows photo-quality brand visuals or coded labeling. |
Machinery Used | Starlinger, W&H | Provides real-time adjustments to achieve optimal weaving outputs. |
Finishing Options | Antistatic, breathable | Expands usage scenarios (food, electronics, medical, etc.). |
FAQs
- How do pulling temperature and drawing ratio affect bag strength?
Proper heat and stretching lead to fewer weak points, enabling higher load capacities. - Can I add color stripes to separate product SKUs?
Yes. During weaving, various colors—blue, red, green—are introduced, simplifying warehouse sorting. - Is advanced printing possible on thinner-gauge material?
Absolutely. With meticulous tension control from Starlinger/W&H lines, even lightweight fabrics accept high-detail prints. - What about moisture or contamination concerns?
Lamination and specialized coatings (antimicrobial, anti-static) address these, ensuring product integrity. - Do these bags suit eco-friendly initiatives?
PP’s recyclability meets rising sustainability priorities, plus repeated usage cuts down on single-use waste.
Step-by-Step Guide: Producing SOS PP Fabric Bags
- Material Selection
- Evaluate polypropylene grade based on load demands and finishing requirements.
- Extrusion and Tape Formation
- Employ Starlinger/W&H extruders for uniform molten flow.
- Monitor pulling temperature to maintain the correct crystallization rate.
- Weaving and Drawing Ratio
- Set drawing ratio to produce tapes matching the desired gsm and tensile strength.
- Avoid over-stretching to prevent brittleness.
- Coating or Lamination
- Opt for microporous or fully sealed lamination, depending on moisture control needs.
- Incorporate anti-static or antimicrobial layers if required.
- Printing & Branding
- Use offset, flexographic, or digital printing for full-surface logos or imagery.
- Integrate color-coded stripes for quick product identification.
- Quality Inspections
- Conduct tensile, tear, and seam tests to confirm compliance with global packaging standards.
- Adjust equipment parameters if any variation arises.
- Logistics & Distribution
- Package folded or stacked bags in optimized shipments for minimal breakage.
- Provide instructions for safe storage and usage guidelines to distributors or end users.
Staying Ahead: Trends and Innovations
- IoT and Smart Tagging
Growing adoption of RFID tags or QR codes on the bags—enabling real-time inventory tracking and authenticity checks. - Advanced Coatings
Heat-reflective, odor-sealing, and humidity-scavenging finishes are emerging in sensitive product lines. - Recycled PP
Many producers experiment with partial recycled content to meet eco-friendly mandates and reduce virgin PP consumption. - Automation & Digital Twins
Real-time monitoring fosters consistent production, with “digital twin” simulations to predict any machinery flaws or misalignments.
External Links
For more on SOS PP Bags adapted to logistics and diverse packaging environments, explore the versatility of SOS-PP-bags in global transportation and logistics detailing how they excel in varied shipping conditions. Sustainability-oriented readers might discover additional insight on recyclable PP bags that demonstrate innovative methods to minimize plastic waste.
Conclusion
SOS PP Fabric Bags represent a transformative solution catering to multiple industries, from heavy-duty construction to delicate consumer packaging. Backed by Starlinger and W&H machinery, the refined temperature control and drawing ratio underpin their dependable quality. When paired with forward-thinking design options—breathable weaves, lamination, color-coding, and advanced printing—these bags meet both practical storage and aesthetic branding goals.
In a global landscape increasingly driven by reliability, sustainability, and brand aesthetics, SOS PP Fabric Bags deliver a compelling blend of performance and customizability. Whether for food products requiring ventilation, industrial materials necessitating sturdy handling, or consumer brands seeking vibrant packaging to engage buyers, these technologically advanced bags stand ready to elevate packaging solutions to a new standard of excellence.