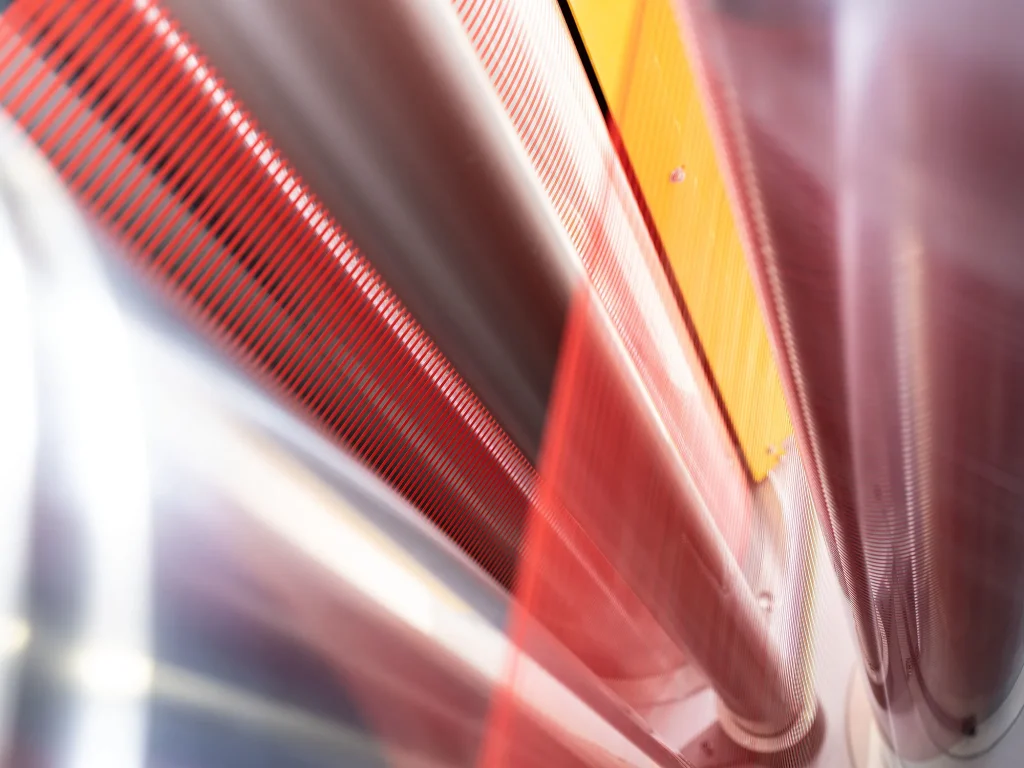
- 1. Critical Challenges in Fertilizer Packaging – How SOS PP Bags Deliver
- 2. Technical Specifications: Balancing Durability and Compliance
- 3. Solving Corrosion and Heat Buildup
- 4. Regional Compliance: Choosing the Right Parameters
- 5. FAQs: Expert Answers for Procurement Teams
- 6. Why VidePak Leads in Fertilizer Packaging
In the global fertilizer industry, 25–30% of product losses occur due to inadequate packaging, costing manufacturers over $2.5 billion annually. At VidePak, we address this challenge head-on with SOS PP fabric bags, engineered to deliver unmatched moisture resistance, corrosion protection, and load-bearing capacity for fertilizers and compound fertilizers. Our ISO 9001-certified bags reduce spoilage rates by 35%, withstand corrosive agents like ammonium nitrate, and comply with EU, US, and Asian safety standards – all while cutting logistics costs by 20% through optimized weight-to-strength ratios. With 30+ years of expertise and 100+ Starlinger circular looms, we serve 45+ countries, producing 80 million bags yearly for clients like Yara International and Nutrien.
1. Critical Challenges in Fertilizer Packaging – How SOS PP Bags Deliver
Moisture Control in Humid Climates
Fertilizers like urea absorb moisture at relative humidity (RH) levels above 60%, causing caking and nutrient degradation. VidePak’s SOS PP bags integrate:
- BOPP Lamination: Blocks 99% water vapor (0.8 g/m²/24h permeability @38°C, 90% RH – ASTM E96).
- PE Inner Liners: 80–120 micron thickness for tropical climates (e.g., Southeast Asia).
- Desiccant Pouches: Optional silica gel inserts for extended storage.
Case Study: A Brazilian NPK producer reduced moisture-related rejects from 8% to 1.2% using our 3-layer laminated SOS PP bags with heat-sealed PE liners.
2. Technical Specifications: Balancing Durability and Compliance
Global Standard Alignment
Standard | Key Requirements | VidePak Solution |
---|---|---|
EU EN 12572 | ≤1.5% moisture ingress after 48h @85% RH | 120 g/m² BOPP + 100μ PE liner |
US ASTM D5265 | UV resistance ≥12 months outdoor | Carbon-black stabilized PP yarn |
JIS Z 0208 | Salt spray corrosion resistance (500h) | Anti-corrosive ink coatings |
AS 2070 | Load capacity ≥6:1 safety factor | 10×10 weave density, 12 N/mm² |
Customization Matrix
Fertilizer Type | Bag Configuration |
---|---|
Urea | 100 g/m² PP + 80μ PE liner + vent patches |
DAP/MAP | 120 g/m² PP + Alu foil liner + sewn valve |
NPK Compounds | 150 g/m² laminated PP + anti-static layer |
3. Solving Corrosion and Heat Buildup
Chemical Resistance
VidePak’s SOS PP bags utilize:
- Virgin PP Resin: pH resistance range 2–12 (ISO 175).
- Acid-Barrier Coatings: Protect against sulfuric acid traces in superphosphate fertilizers.
Thermal Management
- Ventilated Designs: Micro-perforations (2–5 mm² vents per bag) reduce internal temperatures by 8–10°C during maritime transport.
- White UV-Reflective Prints: Lower surface temps by 15°C vs. black bags (per 2024 UAE field tests).
4. Regional Compliance: Choosing the Right Parameters
European Markets (EN Standards)
- Mandatory: ≤0.5% open area for dust retention (EN 14362).
- Solution: Ultrasonic seam sealing + 150 g/m² fabric.
North America (ASTM/PPAI)
- Required: 6:1 safety factor for FIBC bags (ASTM D7388).
- Implementation: 8×8 weave pattern with 14 N/mm² tensile strength.
Asia-Pacific (JIS/GB)
- GB/T 8947: Requires ≥50 cycles of flex resistance.
- VidePak Edge: 4-layer laminated corners withstand 200+ flex cycles.
5. FAQs: Expert Answers for Procurement Teams
Q1: How to select inner liner thickness for high-humidity regions?
A: Use 120μ PE liners for RH >70% (e.g., Indonesia), 80μ for RH 50–70% (e.g., Mediterranean).
Q2: Do laminated bags affect recycling compliance?
A: Our BOPP/PE layers separate cleanly during recycling, meeting EU Circular Economy Package 2030 targets.
Q3: What’s the optimal bag weight for 50kg fertilizer portions?
A: 100 g/m² unlaminated (arid climates) vs. 130 g/m² laminated (coastal areas), with ±0.2kg tolerance.
6. Why VidePak Leads in Fertilizer Packaging
- Global Certifications: REACH, FDA, Oeko-Tex 100.
- Rapid Customization: 15-day turnaround for tailored designs (e.g., FIBC bulk bags with discharge spouts).
- Sustainability: 40% solar-powered production, 100% recyclable materials.
References
- VidePak. (2025). Custom Woven Bags: Tailored Solutions for Chemical Products.
- VidePak. (2025). BOPP Laminated Woven Bags: Branding and Market Dynamics.
- VidePak Co., Ltd. Website: https://www.pp-wovenbags.com/. Email: info@pp-wovenbags.com.
Data validated as of March 2025. Technical specifications subject to regional testing protocols.