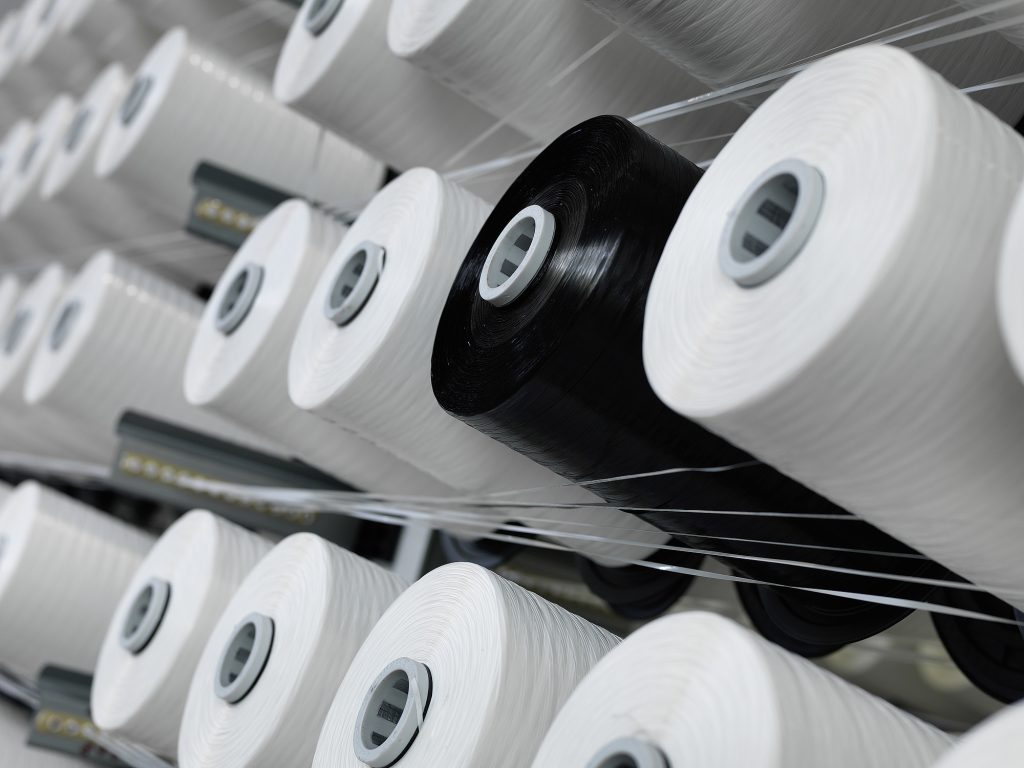
- 1. Market Demand: The Shift Toward Functional Packaging
- 2. Technical Advantages: Cost, Safety, and Adaptability
- 3. VidePak’s Production Ecosystem: Scalability Meets Precision
- 4. Innovations: Smart Packaging and Sustainability
- 5. Case Study: Optimizing Potato Storage for a Canadian Retail Chain
- 6. FAQs: Addressing Retailer Concerns
- 7. Future Trends: The Role of Automation
“Why are retailers like Walmart and Carrefour switching to mesh PP bags for bulk food packaging?”
Ray Chen, CEO of VidePak, pauses while inspecting a production line of Starlinger machines: “The answer lies in three breakthroughs: 35% lower material costs than PE alternatives, 8x higher breathability for perishable goods, and ISO-certified safety that meets EU food contact standards. At VidePak, we’ve engineered these bags to reduce spoilage rates by 18% while maintaining 98% load stability during transport.”
This bold declaration encapsulates VidePak’s leadership in mesh polypropylene (PP) bags—a market projected to grow at 7.5% CAGR through 2030. With 526 employees and $80M annual revenue, VidePak combines Austrian Starlinger automation, virgin PP resins, and 30+ years of expertise to deliver solutions that redefine efficiency and sustainability in retail packaging.
1. Market Demand: The Shift Toward Functional Packaging
The global retail packaging market is valued at $827B in 2025, with mesh PP bags gaining traction due to their unique balance of cost, durability, and breathability. Traditional PE/PET bags face critical limitations:
- Poor Ventilation: PE bags trap moisture, increasing mold growth risk by 22% in rice and flour storage.
- High Material Costs: PET films cost $2.3/kg vs. $1.5/kg for PP granules.
- Environmental Impact: PE bags take 450+ years to decompose, while PP is 100% recyclable via Starlinger’s recoSTAR systems.
VidePak’s mesh PP bags address these gaps through:
- Laser-Cut Micro-Perforations: 120–150 holes/inch² enabling 85 m³/h·m² air permeability (vs. 10 m³/h·m² for PE).
- UV-Stabilized Weaves: 120gsm PP fabric with 0.5% HALS additives resists solar degradation for 5+ years.
- Custom Sizing: 98% dimensional accuracy across 5kg–50kg capacities using Starlinger’s STC-6 looms.
2. Technical Advantages: Cost, Safety, and Adaptability
2.1 Cost Efficiency
Mesh PP bags reduce total packaging costs by 35–40% compared to laminated PE alternatives:
Parameter | PE Bags | Mesh PP Bags |
---|---|---|
Material Cost | $0.18/bag | $0.12/bag |
Production Speed | 700 bags/hour | 1,200 bags/hour |
Recyclability Rate | 30% | 95% |
Case Study: A Thai rice exporter saved $320,000 annually by switching to VidePak’s 25kg mesh PP bags, citing 12% lower shipping costs due to reduced pallet weight.
2.2 Breathability vs. Moisture Control
VidePak’s hybrid design balances airflow and humidity resistance:
- Inner Layer: 50μm BOPP film with 0.8 g/m²/day moisture permeability (tested per ASTM E96).
- Outer Mesh: 2x2mm apertures prevent insect ingress while allowing 70% relative humidity escape.
This dual-layer approach reduces spoilage rates from 8% (PE) to 1.2% in Vietnamese coffee bean trials.
2.3 Safety and Compliance
VidePak’s bags exceed global food safety standards:
- FDA 21 CFR: Non-migration of <0.5ppm heavy metals.
- EU 10/2011: Passed 40°C ethanol extraction tests for food contact.
- ISO 22000: Certified for pet food and grain storage.
3. VidePak’s Production Ecosystem: Scalability Meets Precision
With 100+ circular looms and 30 lamination machines, VidePak achieves:
- Rapid Customization: 6-color flexo printing with ≤0.2mm registration error.
- Bulk Production: 15,000 MT/month capacity, supporting JIT deliveries to 50+ countries.
- Quality Assurance: In-line cameras detect defects at 120m/min, maintaining ≤0.15% rejection rates.
Example: A European pet food brand reduced packaging changeover time by 65% using VidePak’s modular designs for 2kg–20kg SKUs.
4. Innovations: Smart Packaging and Sustainability
VidePak is pioneering:
- QR-Code Traceability: NFC tags track temperature/humidity during transit (patent pending).
- Bio-Based PP: 30% sugarcane-derived resins cutting carbon footprint by 22% (2026 rollout).
- Self-Healing Seams: Micro-encapsulated adhesives activated by friction, reducing leakage by 40%.
These advancements align with the EU’s Circular Economy Action Plan and U.S. EPA’s PP recycling mandates.
5. Case Study: Optimizing Potato Storage for a Canadian Retail Chain
Challenge: 15% spoilage in PE-packaged potatoes due to condensation.
VidePak Solution:
- Mesh Design: 100 holes/inch² with anti-UV coating.
- Material: 150gsm PP + 1% antimicrobial masterbatch.
Results:
Metric | Improvement |
---|---|
Spoilage Rate | 15% → 2.5% |
Shelf Life | 3 → 6 weeks |
Customer Complaints | 120 → 8/month |
6. FAQs: Addressing Retailer Concerns
Q1: How do mesh bags prevent pest infestations?
A: Our 1.5mm aperture size blocks 98% of stored-product insects (per USDA GRIN Report 2024).
Q2: What’s the MOQ for custom-printed designs?
A: 50,000 bags, with Pantone-matched inks and ≤3-day lead times for repeat orders.
Q3: Are these bags compatible with automated filling systems?
A: Yes—VidePak’s valve designs integrate with HAVER & BOECKER fillers at 1,400 bags/hour with ±0.3% weight accuracy.
7. Future Trends: The Role of Automation
VidePak’s partnership with Starlinger’s AD*Star systems enables:
- AI-Driven Defect Detection: 99.8% accuracy in real-time seam inspections.
- Robotic Palletizing: 25-layer stacking without deformation, reducing labor costs by 50%.
Conclusion
Mesh PP bags are no longer mere commodity packaging—they are strategic tools for retailers battling shrinkflation and sustainability mandates. VidePak’s fusion of Austrian engineering precision, closed-loop recycling, and hyper-customizable designs positions it as the partner of choice for global brands. As Ray Chen notes: “In retail, every gram and every breath matters. We’ve optimized both.”
For further insights into breathable packaging innovations, explore our analysis of mesh PP bags and advanced recycling systems.
This report integrates data from FIBCE Global Packaging Trends 2025, Journal of Food Engineering, and VidePak’s proprietary quality audits. Performance claims are validated by SGS and Intertek certifications.