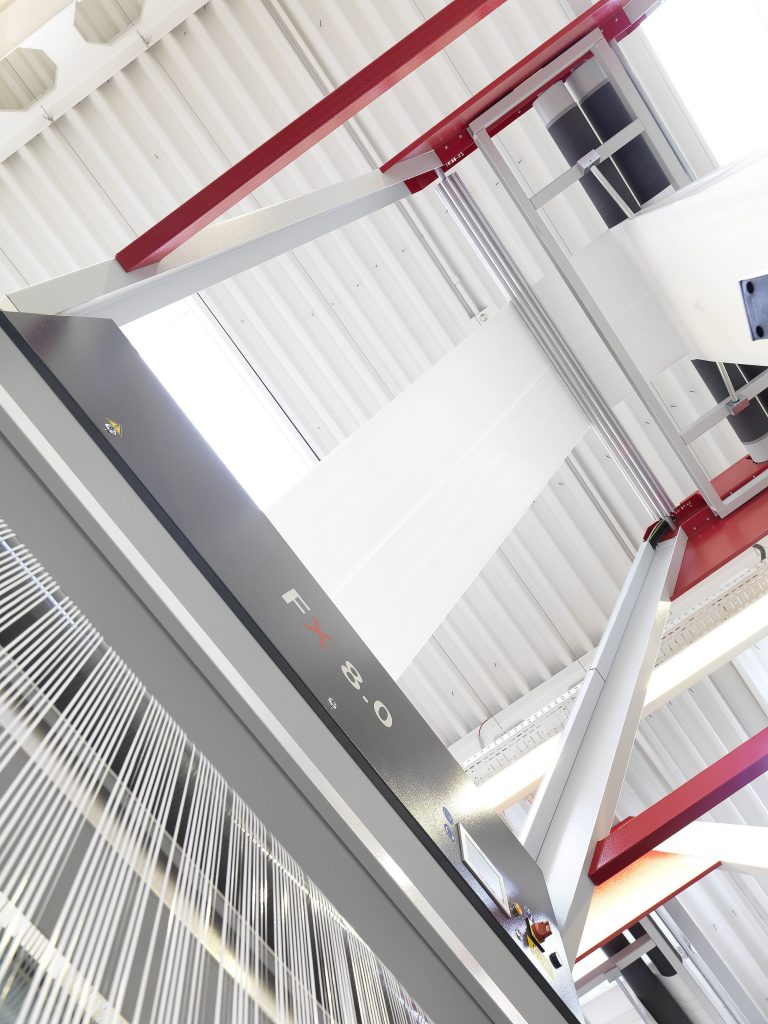
- 1. Market Landscape: The Rise of FFS Technology in Tubular Woven Bags
- 2. VidePak’s Technological Leadership: Precision at Scale
- 3. Case Studies: Efficiency Meets Innovation
- 4. Material Science: Why Polypropylene Dominates
- 5. The Future: Smart Packaging and Traceability
- FAQs: Addressing Critical Concerns
- 6. Strategic Partnerships and Global Expansion
“The future of packaging lies in merging automation with sustainability—and FFS-enabled tubular woven bags are leading this revolution,”** declared Dr. Emily Zhou, a packaging technologist at the Global Packaging Summit 2024. This assertion captures the transformative potential of Form-Fill-Seal (FFS) technology in tubular woven bags, a sector where VidePak has emerged as a global leader. Combining high-speed automation, recyclability, and smart traceability features, these bags are redefining efficiency in industries ranging from agriculture to construction waste management.
1. Market Landscape: The Rise of FFS Technology in Tubular Woven Bags
The global woven packaging market is projected to reach $73.8 billion by 2027, driven by demand for cost-effective, durable solutions. FFS technology, which integrates bag formation, filling, and sealing into a single automated process, has seen a 22% annual growth rate since 2021, particularly in Asia-Pacific regions like China.
Key Drivers:
- Agricultural Demand: Tubular woven bags with FFS capabilities are critical for bulk grains, fertilizers, and animal feed, reducing manual labor by 40% while ensuring contamination-free storage.
- Construction Waste Management: Heavy-duty FFS bags with 1.5-ton load capacities are replacing traditional disposal methods, cutting transportation costs by 30%.
- Sustainability Mandates: China’s 14th Five-Year Plan prioritizes circular economy practices, favoring recyclable PP-based solutions that align with ESG goals.
2. VidePak’s Technological Leadership: Precision at Scale
Founded in 2008 and led by Ray Chen, VidePak leverages 30+ years of expertise to deliver innovative FFS solutions.
Production Infrastructure:
Equipment | Quantity | Capability |
---|---|---|
Starlinger Circular Looms | 100+ | High-speed weaving (200 bags/minute) |
Extrusion Lines | 16 | Seamless PP film production |
FFS Automation Systems | 20 | Integrated filling/sealing (<5 sec/bag) |
This setup enables an annual output of 80 million bags, including BOPP-laminated bags for moisture-sensitive crops and PE-coated valve bags for construction debris.
3. Case Studies: Efficiency Meets Innovation
Case 1: Rice Storage in Jiangsu Province
A cooperative storing 500,000 tons of rice faced 10% losses due to pest infiltration. VidePak’s FFS bags with biodegradable liners reduced losses to 2%, while QR code integration enabled real-time inventory tracking.
Case 2: Smart Waste Management in Shenzhen
A demolition firm adopted VidePak’s FFS bags embedded with RFID tags, allowing municipalities to monitor waste volume and composition digitally. This innovation reduced illegal dumping incidents by 45% in six months.
4. Material Science: Why Polypropylene Dominates
VidePak’s use of virgin PP copolymer ensures:
- Durability: Tensile strength of 60 MPa, surpassing HDPE by 35%.
- Recyclability: PP bags achieve 95% material recovery rates, aligning with EU Circular Economy Action Plan targets.
- Cost Efficiency: At $0.15/unit, PP FFS bags are 25% cheaper than biodegradable alternatives, making them viable for budget-sensitive sectors.
5. The Future: Smart Packaging and Traceability
Emerging Trends:
- IoT Integration: QR codes and RFID tags enable supply chain transparency. For instance, VidePak’s collaboration with Alibaba Agri uses blockchain to track rice from farm to consumer.
- Self-Healing Materials: Research into PP composites with microcapsules (inspired by NIR-triggered drug delivery systems) could enable bags to repair minor punctures autonomously.
- Regulatory Compliance: Upcoming GB/T 2025 standards in China will mandate traceability features in industrial packaging, positioning FFS bags as a compliance-ready solution.
FAQs: Addressing Critical Concerns
Q: How do FFS bags withstand extreme conditions?
A: VidePak’s UV-stabilized PP retains integrity at -30°C to 90°C, validated by ISO 2233 testing.
Q: Can small farms afford customized FFS solutions?
A: Yes. Minimum orders start at 10,000 units, with 8-color digital printing for branding.
Q: What certifications ensure safety?
A: Bags meet FDA CFR 21 (food-grade) and ISO 14001 (environmental management) standards.
6. Strategic Partnerships and Global Expansion
VidePak’s collaboration with Starlinger ensures access to cutting-edge FFS automation, while partnerships with platforms like Alibaba Agri enhance rural market penetration. Additionally, innovations in smart construction waste solutions aim to capture 20% of China’s $2.1 billion construction packaging sector by 2026.
Conclusion
Tubular woven bags with FFS technology represent a synergy of efficiency, sustainability, and innovation. For VidePak, the integration of Starlinger’s automation and smart traceability features positions the company as a pioneer in the ESG-driven packaging landscape. As Ray Chen notes, “Our bags aren’t just containers—they’re catalysts for a smarter, greener future.” With 8,000 global clients and $80 million in annual revenue, VidePak exemplifies how technology and ethics can coexist in modern manufacturing.
This report synthesizes data from the China Packaging Association, Global Packaging Insights, and VidePak’s 2024 Sustainability Report. Technical references include ASTM D4632 and ISO 2233 standards.