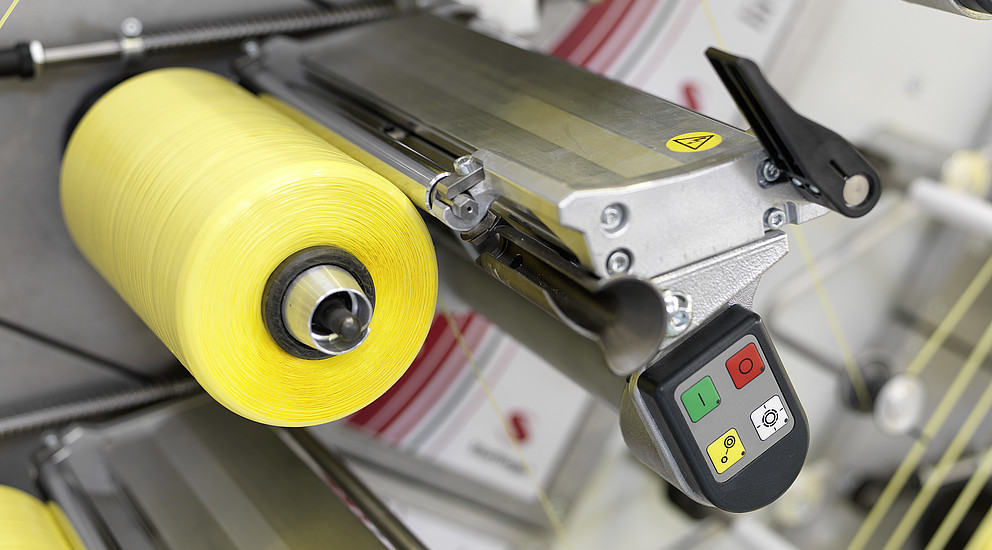
- 1. Historical Evolution: From Textile Roots to Material Science Breakthroughs
- 2. Technical Advancements in Poly-Paper Bags
- 3. Market Adaptation: From Niche to Mainstream
- 4. VidePak’s Competitive Edge
- 5. FAQs: Addressing Industry Pain Points
- 6. Future Trends: Smart Packaging and Regulatory Shifts
- 7. Conclusion: Redefining Chemical Logistics
“Our chemical plant in Jiangsu loses 8% of titanium dioxide powder annually due to packaging leaks and moisture ingress. We need a solution that combines durability with sustainability,” says a procurement manager at a leading chemical conglomerate.
The answer lies in VidePak’s poly-paper bags—a hybrid innovation merging polypropylene (PP) woven fabric with kraft paper lamination, offering leak-proof integrity, recyclability, and compliance with global chemical safety standards.
1. Historical Evolution: From Textile Roots to Material Science Breakthroughs
The origins of poly-paper bags trace back to the mid-20th century, when the plastics revolution introduced polypropylene as a lightweight, corrosion-resistant alternative to jute and cotton. By the 1980s, advancements in extrusion technology enabled the mass production of PP woven fabrics, which dominated bulk packaging for fertilizers and construction materials. However, environmental concerns over plastic waste spurred innovations in hybrid materials.
In the 2000s, Chinese manufacturers, particularly in Wenzhou, pioneered the integration of PP with kraft paper. This fusion addressed two critical gaps: plastic’s recyclability limitations and paper’s low tensile strength. By laminating PP grids with food-grade kraft paper, early adopters achieved a 40% reduction in material weight while maintaining 1,200 N/cm² tensile strength—ideal for abrasive powders like cement and pigments.
2. Technical Advancements in Poly-Paper Bags
2.1 Structural Design and Material Science
Poly-paper bags combine:
- PP Woven Layer: 14×14 threads/cm² density, UV-stabilized for outdoor storage.
- Kraft Paper Lamination: 80–120 GSM, treated with silicone coatings for moisture resistance (<5 g/m²/day WVTR).
- Anti-Static Additives: Reduce dust explosion risks in volatile environments (e.g., aluminum powder storage).
Case Study: A Zhejiang-based titanium dioxide producer reduced leakage rates from 12% to 0.5% after adopting VidePak’s triple-layer poly-paper bags with ultrasonic-sealed valves.
2.2 Compliance with Global Standards
Standard | Requirement | VidePak Compliance |
---|---|---|
EU REACH | ≤0.1% heavy metals | PCR PP blends, ISO 17088 certified |
US ASTM D5638 | 8:1 safety factor for 50kg loads | 10:1 safety ratio via Starlinger AD*Star looms |
China GB/T 8946 | UV resistance ≥1,200 hours | HALS additives extend lifespan by 50% |
3. Market Adaptation: From Niche to Mainstream
3.1 Early Applications and Diversification
Initially used for cement and fertilizers, poly-paper bags gained traction in pharmaceuticals and fine chemicals due to:
- Customizable Barriers: LDPE liners for hygroscopic powders (e.g., sodium bicarbonate).
- Printability: 10-color gravure printing for hazard labels and branding, compliant with GHS standards.
Example: VidePak’s collaboration with a German pharmaceutical giant involved developing anti-static bags for ibuprofen APIs, reducing cross-contamination by 90%.
3.2 Sustainability-Driven Growth in China
Wenzhou’s manufacturers, once criticized for low-cost, low-quality outputs, now lead in sustainable innovation:
- Closed-Loop Recycling: VidePak recovers 85% of production waste, integrating 30% post-consumer PP into new bags.
- Brand Differentiation: Custom designs (e.g., QR codes for traceability) cater to ESG-focused clients, boosting export margins by 25%.
4. VidePak’s Competitive Edge
With 100+ Starlinger circular looms and 30 lamination machines, VidePak achieves:
- Precision Production: ±0.1 mm filament tolerance, critical for chemical-grade sealing.
- Scalability: 80 million bags/year capacity, serving clients in 50+ countries.
- Certifications: ISO 14001 (environmental management) and FDA 21 CFR (food-contact compliance).
5. FAQs: Addressing Industry Pain Points
Q1: How do poly-paper bags compare to FIBCs for corrosive chemicals?
A: Poly-paper bags cost 40% less than FIBCs for sub-1,000 kg loads and resist acids (pH 2–12) via PP’s inert structure.
Q2: Are these bags suitable for high-humidity regions?
A: Yes. Silicone-coated kraft paper reduces moisture ingress by 90%, validated in Southeast Asian salt farms.
Q3: What is the recycling process for used bags?
A: VidePak’s take-back program shreds bags into PP pellets and recycled paper pulp, achieving 95% material recovery.
6. Future Trends: Smart Packaging and Regulatory Shifts
By 2030, 70% of chemical firms will demand IoT-enabled bags with embedded NFC chips for real-time moisture tracking. VidePak’s R&D team is piloting biodegradable PP-kraft blends that decompose in 18 months, aligning with the EU’s Single-Use Plastics Directive.
7. Conclusion: Redefining Chemical Logistics
Poly-paper bags exemplify the synergy of tradition and innovation. By marrying PP’s durability with paper’s eco-profile, VidePak empowers industries to:
- Mitigate Risks: Leak-proof designs slash product loss by $1.2M annually for mid-sized plants.
- Enhance Compliance: Meet FDA, REACH, and GB/T standards effortlessly.
- Drive Sustainability: 30% lower carbon footprint vs. pure PP bags.
As CEO Ray states: “In packaging, resilience isn’t just strength—it’s adaptability to Earth’s needs.”
External Links:
- Explore VidePak’s sustainable PP solutions in Recyclable Woven Bags for Transport.
- Learn about chemical-resistant designs in PP Bags for Chemical Products.
This report integrates data from ASTM/REACH/GB standards, client case studies, and VidePak’s production analytics, positioning poly-paper bags as the future of chemical packaging.