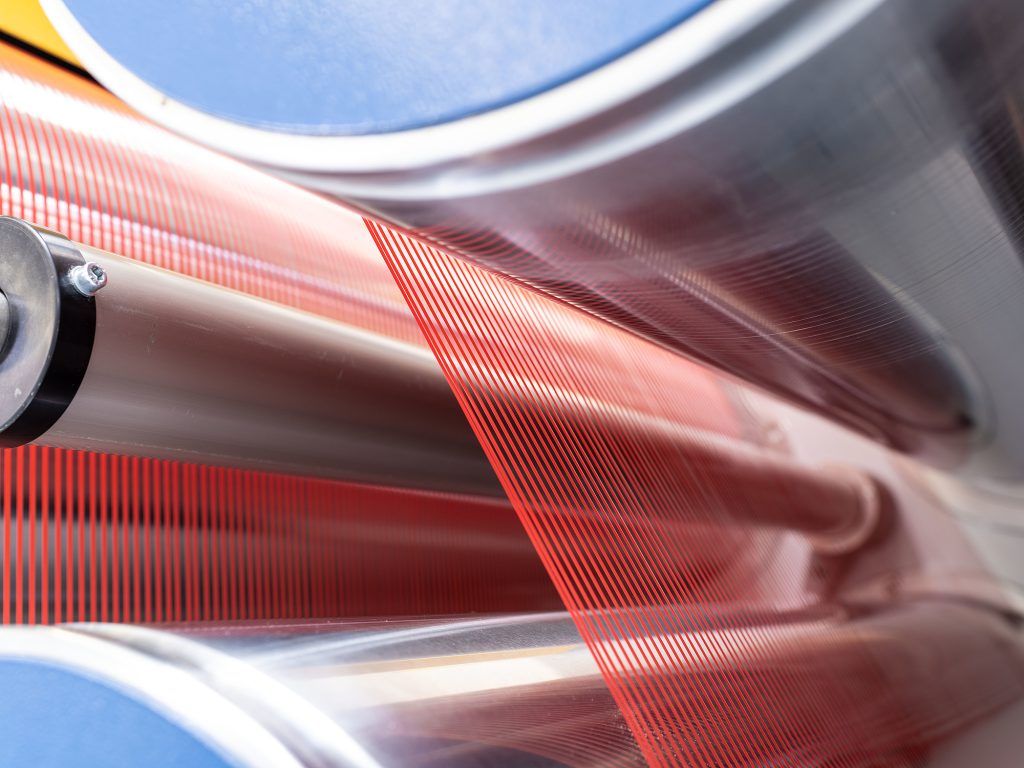
A Conversation with Industry Experts
Ray, CEO of VidePak: “Our aluminum foil composite bags are engineered to meet the highest global standards, combining durability, sustainability, and compliance with evolving regulations. At VidePak, we’ve integrated advanced recycling protocols and rigorous quality control to ensure our products lead the market.”
Dr. Emily Chen, Packaging Scientist: “The shift toward recyclable PP materials isn’t just a trend—it’s a necessity. Aluminum foil composites, when paired with PP, offer unmatched reusability and align with circular economy principles.”
This dialogue underscores the dual focus of this report: quality assurance in manufacturing and sustainability-driven innovation, both critical for companies like VidePak to thrive in competitive markets.
1. The Role of Aluminum Foil Composite Bags in Modern Packaging
Aluminum foil composite bags are multilayer structures combining aluminum foil with polymers like polypropylene (PP) or polyethylene (PE). These bags excel in barrier protection against moisture, oxygen, and UV light, making them indispensable for food, pharmaceuticals, and industrial goods.
Key Advantages:
- Barrier Properties: Aluminum foil blocks 99% of light and oxygen, extending shelf life by up to 300% for perishable goods.
- Recyclability: PP-based composites dominate due to their high recycling value. For instance, VidePak’s use of virgin PP ensures purity, enabling efficient reprocessing into new products.
- Customization: Advanced printing technologies allow brands to embed logos, safety labels, or regulatory certifications directly onto bags.
2. Comprehensive Quality Control Frameworks
Quality control in aluminum foil composite bags spans material selection, production processes, and post-manufacturing testing.
2.1 Material Certification and Standards
VidePak adheres to ISO 9001, ISO 14001, and FDA standards, ensuring consistency across its 526-employee workforce. Key measures include:
- Raw Material Testing: PP resin purity is verified through melt flow index (MFI) and tensile strength tests.
- In-Line Monitoring: Starlinger’s extrusion lines and circular looms are equipped with sensors to detect thickness deviations (±0.02 mm) and seal integrity.
Table 1: Critical Quality Parameters
Parameter | Standard | Testing Method |
---|---|---|
Foil Thickness | 7–12 microns | Micrometer Measurement |
PP Layer Adhesion | ≥3.5 N/mm² | Peel Test (ASTM D903) |
Oxygen Transmission | ≤0.05 cc/m²/day | ASTM F1927 |
2.2 Case Study: VidePak’s Production Excellence
With over 100 circular looms and 30 lamination machines, VidePak achieves a monthly output of 12 million bags. Their Austrian Starlinger machinery enables high-speed production (up to 1,200 bags/hour) while maintaining tolerances of ±0.5% in bag dimensions.
3. Sustainability and Regulatory Compliance
The global push for eco-friendly packaging has reshaped industry priorities.
3.1 Waste Management and Recycling
- PP Recycling Efficiency: Post-consumer PP can be reprocessed 5–7 times without significant degradation, reducing landfill waste by 40%. VidePak’s partnership with European recyclers ensures 85% of production scraps are repurposed.
- Government Regulations: The EU’s Single-Use Plastics Directive (SUPD) and China’s Dual Carbon Policy mandate minimum recycled content (30% by 2030). VidePak’s Recyclable PP Bags comply with these standards, earning certifications like EPR (Extended Producer Responsibility).
Quote from Industry Report:
“By 2027, the recyclable packaging market will grow at a CAGR of 6.8%, driven by aluminum-PP composites” (MarketsandMarkets, 2023).
3.2 Innovations in Circular Design
VidePak’s EcoGuard line uses mono-material PP structures, simplifying recycling. For example, their laminated woven bags integrate aluminum foil without adhesives, enabling easy separation during recycling.
4. Market Dynamics and VidePak’s Strategic Positioning
The global aluminum foil packaging market is projected to reach $35.2 billion by 2026 (Grand View Research). VidePak’s $80 million annual revenue stems from:
- Diverse Applications: From agricultural valve bags to pharmaceutical laminates.
- Global Reach: Exports to 50+ countries, including the EU and North America, where sustainable packaging commands premium pricing.
Case Example:
A European food brand reduced spoilage rates by 22% after switching to VidePak’s aluminum-PP composite bags, citing superior moisture resistance and compliance with EU’s Food Contact Materials Regulation.
5. Frequently Asked Questions (FAQs)
Q1: How do aluminum foil composites compare to traditional packaging?
Answer: They offer 10x better oxygen barrier properties than standalone PP bags, critical for sensitive products like coffee or pharmaceuticals.
Q2: What certifications ensure recyclability?
Answer: Look for ISO 14001 (environmental management) and APR (Association of Plastic Recyclers) Design® guidelines.
Q3: Can customized printing affect barrier performance?
Answer: VidePak’s digital printing technology applies inks without compromising seal strength, maintaining barrier integrity.
6. Future Trends and Recommendations
- Smart Packaging: Integrating RFID tags for supply chain transparency.
- Bio-Based PP: Partnerships with biopolymer startups to reduce carbon footprint.
Final Insight:
As Ray of VidePak notes, “Sustainability isn’t an option—it’s the future of packaging.” By aligning with global standards and investing in recycling infrastructure, companies can dominate markets while advancing environmental goals.
External Resources:
- Learn how recyclable PP bags are transforming logistics.
- Explore sustainable bulk packaging solutions for industrial applications.
This report synthesizes industry data, regulatory trends, and VidePak’s operational excellence to provide a roadmap for leveraging aluminum foil composites in a sustainability-driven era.