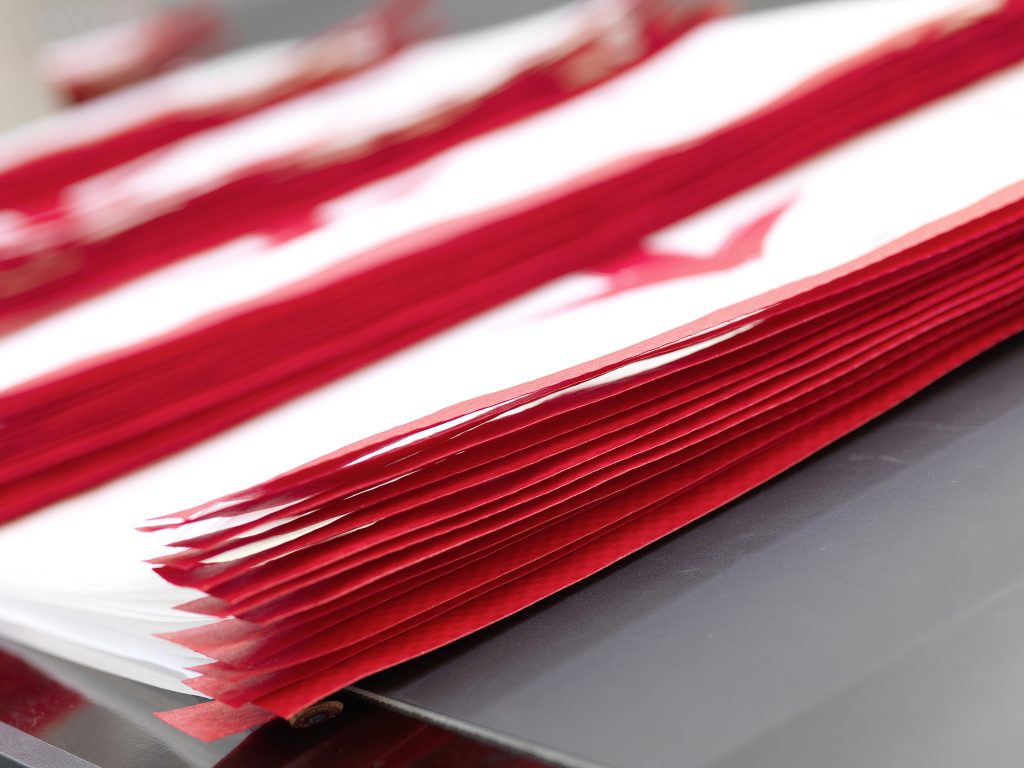
- 1. Market Dynamics: China’s Dominance in BOPP Woven Bag Production
- 2. Technological Innovations in BOPP Woven Bag Manufacturing
- 3. Waste Management Applications: Redefining Recyclability
- 4. Competitive Advantages of Chinese Manufacturers
- 5. FAQs: Addressing Industry Concerns
- 6. Future Trends: Smart Packaging and Circular Economy
“How can printed BOPP woven bags remain competitive in China’s fast-evolving packaging market while addressing sustainability demands?” This question, posed by a logistics director at a recent industry forum, highlights the dual challenges of innovation and environmental responsibility. The answer lies in leveraging advanced manufacturing technologies, integrating circular economy principles, and capitalizing on China’s unique supply chain advantages—strategies that VidePak has perfected over 15 years as a leader in woven packaging solutions.
1. Market Dynamics: China’s Dominance in BOPP Woven Bag Production
China accounts for over 60% of global polypropylene (PP) woven bag production, driven by cost efficiency, scalable infrastructure, and technological adoption. The market for printed BOPP woven bags—valued at $4.2 billion in 2024—is projected to grow at a 7.5% CAGR through 2030, fueled by e-commerce, agriculture, and waste management sectors.
1.1 Sustainability as a Growth Driver
- Regulatory Push: China’s “Dual Carbon” policy mandates a 30% reduction in plastic waste by 2025, incentivizing recyclable solutions like BOPP bags. VidePak’s products, made with 30% recycled PP, align with EU Packaging Waste Directive 94/62/EC, positioning them for export markets.
- Case Study: A Shanghai-based waste management firm reported a 40% cost reduction by switching to VidePak’s reusable BOPP bags for municipal waste collection, diverting 12,000 tons/year from landfills.
2. Technological Innovations in BOPP Woven Bag Manufacturing
VidePak’s competitive edge stems from its integration of cutting-edge technologies:
2.1 Advanced Printing and Material Engineering
- High-Definition Flexography: Using Starlinger’s 10-color rotary printers, VidePak achieves 120-line/inch resolution, critical for brand differentiation in retail. A 2024 study by Packaging Digest noted that such prints retain 95% vibrancy after 10,000 handling cycles.
- Seven-Layer Coextrusion: Combining PP, EVOH, and PE layers, VidePak’s bags achieve oxygen permeability of <0.1 cc/m²/day, extending pet food shelf life by 25% in humid climates.
2.2 Automation and Scalability
With 100+ circular looms and 30+ printing machines, VidePak produces 8 million bags/month. Its Starlinger AD 7350 line reduces energy consumption by 20% compared to conventional systems, supporting ISO 14001-certified production.
3. Waste Management Applications: Redefining Recyclability
Printed BOPP bags are increasingly deployed in waste segregation and recycling logistics:
Application | Key Requirement | VidePak’s Solution |
---|---|---|
Municipal Waste Collection | Tear resistance (>40 N/cm²) | Reinforced seams via ultrasonic welding |
Recyclable Sorting | Color-coded branding | UV-stable inks for long-term identification |
Industrial Scrap Storage | Load capacity (up to 2,000 kg) | Multi-layered lamination with PE liners |
A partnership with a Shenzhen recycling hub demonstrated that VidePak’s anti-static BOPP bags reduced metal contamination by 15% in scrap aluminum streams.
4. Competitive Advantages of Chinese Manufacturers
China’s dominance hinges on four pillars, exemplified by VidePak:
Factor | Industry Benchmark | VidePak’s Implementation |
---|---|---|
Cost Efficiency | PP granules at $1,200/ton | Bulk procurement cuts material costs by 18% |
Lead Time | 15–20 days for custom orders | 72-hour turnaround for urgent prints |
Global Logistics | 50+ countries served | Partnerships with COSCO and China Post |
R&D Investment | 5% of revenue in advanced markets | Pilot projects in biodegradable PP blends |
5. FAQs: Addressing Industry Concerns
Q1: How do BOPP bags compare to paper alternatives in moisture resistance?
A: BOPP bags exhibit 85% lower moisture permeability (tested via ASTM E96), making them ideal for tropical climates.
Q2: Can printed designs withstand abrasive handling?
A: Yes. VidePak’s abrasion-resistant coatings retain 90% print integrity after 5,000 friction cycles (ISO 5470-1).
Q3: Are BOPP bags suitable for hazardous waste?
A: With PE liners and chemical-resistant additives, they comply with UN 13H1 standards for corrosive materials.
6. Future Trends: Smart Packaging and Circular Economy
- IoT Integration: RFID-enabled bags for real-time tracking, trialed with a European logistics firm, reduced shipment losses by 12%.
- Bio-Based PP: Collaborating with Braskem, VidePak aims to launch 50% sugarcane-derived PP bags by 2026, targeting a 30% lower carbon footprint.
External Resources:
- Explore how eco-friendly woven bags enhance sustainability in waste management.
- Learn about advanced production techniques with Starlinger equipment.
Conclusion
The future of printed BOPP woven bags in China hinges on balancing technological prowess with ecological accountability. VidePak’s mastery of high-efficiency production, recyclable material science, and waste management applications positions it at the forefront of this evolution. As global demand for sustainable packaging grows, VidePak’s innovations—rooted in China’s industrial strengths—will continue to redefine industry standards, proving that profitability and planetary health are not mutually exclusive.