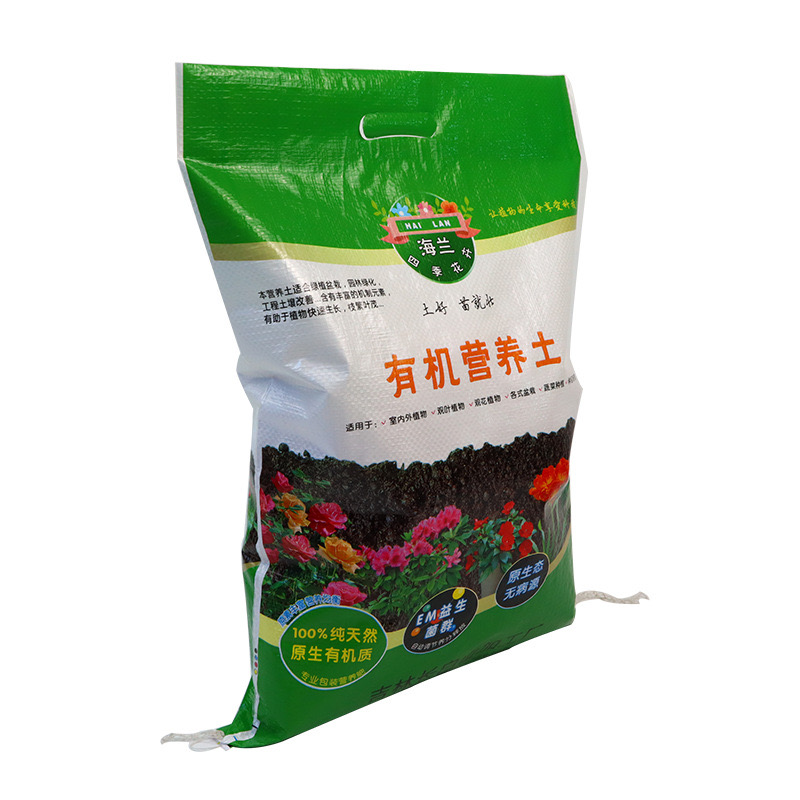
The packaging industry has seen tremendous advancements over the years, particularly in the field of woven bags. Among these innovations, FFS Roll Bags (Form-Fill-Seal Roll Bags) have become an essential packaging solution for a wide range of industries. Not only do they streamline the packaging process, but they also provide excellent strength, durability, and versatility for a variety of applications. This article will discuss the key attributes of FFS Roll Bags, including the number of bags in a typical roll, their usage in construction materials like cement, plaster powder, and joint fillers, and the benefits of materials such as polypropylene in these applications.
How Many Bags Are Typically in an FFS Roll?
When it comes to FFS Roll Bags or FFS Roll Sacks, understanding the number of bags per roll is essential for both manufacturers and end users. Typically, an FFS roll consists of 200 to 300 bags, depending on the size and weight of the bags as well as the specifications provided by the manufacturer. These bags are pre-formed and connected in a roll for easy loading into automatic packaging machines, reducing the time and labor associated with packing.
For example, when dealing with Tubular Woven Bags or FFS PP Bags, the rolls may vary slightly in size based on the dimensions of the individual bags. A Tubular Woven Bag is particularly popular in bulk packaging due to its strength and ability to withstand rough handling during transportation.
Bag Type | Number of Bags per Roll | Common Sizes | Usage |
---|---|---|---|
FFS Roll Bags | 200–300 bags | 12″ x 24″ to 20″ x 40″ | Cement, plaster powder, food-grade packaging |
FFS Woven Bags | 100–250 bags | 16″ x 24″ to 24″ x 40″ | Agricultural products, construction materials |
Tubular Woven Bags | 250–300 bags | 18″ x 28″ to 24″ x 40″ | Chemicals, bulk storage |
FFS PP Bags | 100–200 bags | 16″ x 24″ to 20″ x 36″ | Food packaging, pet food |
Applications in the Construction Industry
The construction industry has diverse needs when it comes to packaging materials. FFS Woven Bags and FFS Roll Bags are commonly used for packaging building materials such as cement, joint fillers, gypsum powder, and plaster powder. Their ability to endure rough handling, exposure to moisture, and high impact makes them perfect for such applications. Let’s explore how these bags are used across various construction materials:
1. Cement and Plaster Powder Packaging
Cement and plaster powder require sturdy, moisture-resistant packaging that can keep the material dry and intact during transportation. FFS PP Bags and FFS Roll Bags provide the ideal solution due to their high tensile strength and resistance to tears, abrasions, and punctures. Polypropylene (PP), the material of choice for these bags, is lightweight yet durable, ensuring the bags remain intact even under challenging handling conditions.
In this context, Tubular Woven Bags are often favored because they can be customized with multiple layers of lamination or coating to further improve moisture resistance. This ensures that the powder stays dry, even in humid conditions, maintaining its integrity for end users.
2. Joint Fillers and Gypsum Powder
Another common application is the packaging of joint fillers and gypsum powder, both of which are sensitive to moisture. For these applications, FFS Woven Bags are often preferred due to their ability to offer extra protection against water penetration. With the added benefit of customizable printing options, these bags can be branded and designed to meet specific needs, making them an excellent choice for large-scale construction projects.
Material Advantages: Polypropylene in Construction Packaging
The material used for FFS Woven Bags, primarily polypropylene, has a range of properties that make it ideal for construction packaging. Let’s look at some of the key advantages:
1. Strength and Durability
Polypropylene is known for its exceptional strength-to-weight ratio, making it one of the most durable materials for woven bags. This strength is critical when packaging heavy construction materials such as cement and plaster powder, where the bags need to endure both the weight of the contents and rough handling during transport.
2. Wear and Abrasion Resistance
The wear resistance of polypropylene ensures that FFS Roll Bags can withstand the rough environments commonly found in construction sites and warehouses. They can be subjected to friction, scraping, and handling without tearing or wearing thin.
3. Moisture Resistance
One of the most significant challenges in packaging building materials like plaster and cement is moisture exposure. FFS Woven Bags made from polypropylene offer excellent water resistance, ensuring that the contents remain dry during storage and transport. This is particularly important for materials that can clump or degrade when exposed to moisture.
4. Tear Resistance
FFS PP Bags provide superior tear resistance, which is essential for materials like gypsum and cement. These products often experience rough handling, and polypropylene’s inherent resistance to tearing means the bags can survive multiple stages of handling without breaking open.
5. Cost-Effectiveness
Polypropylene bags are not only strong and durable but also cost-effective. The cost of manufacturing Tubular Woven Bags from PP is lower compared to other materials, which is an important factor for large-scale construction projects. These bags offer a balance between affordability and high performance, making them an excellent choice for construction material packaging.
Sustainability and Innovations in Packaging
As sustainability becomes more important across industries, the packaging sector has also embraced eco-friendly innovations. While FFS Woven Bags and Tubular Woven Bags made from polypropylene remain popular for their durability and performance, there are growing trends in reducing the environmental footprint of these products.
For instance, companies like VidePak are innovating with recycled polypropylene (rPP), which helps reduce waste and the carbon footprint associated with the production of virgin plastic. By incorporating FFS Roll Bags made from rPP, manufacturers can offer a more sustainable packaging solution while maintaining the high performance that is critical for construction materials.
Conclusion: Optimizing Packaging Efficiency in the Construction Industry
In conclusion, FFS Roll Bags and Tubular Woven Bags are indispensable in the packaging of construction materials such as cement, joint fillers, plaster powder, and gypsum. Their strength, durability, moisture resistance, and tear resistance make them the optimal choice for safeguarding these essential materials during transportation and storage. By using FFS PP Bags and other woven polypropylene solutions, manufacturers can ensure that construction materials remain intact, secure, and ready for use in various projects.
Furthermore, the ongoing developments in sustainable packaging practices offer exciting opportunities for the future. By embracing eco-friendly materials and reducing the reliance on single-use plastics, the packaging industry, including companies like VidePak, is playing a crucial role in creating a more sustainable future.
For more insights into FFS Roll Bags and their applications, take a look at Optimizing Packaging Efficiency with FFS Roll Bags and Tubular Woven Bags with Form-Fill-Seal Systems: A Revolution in Safe and Efficient Packaging.