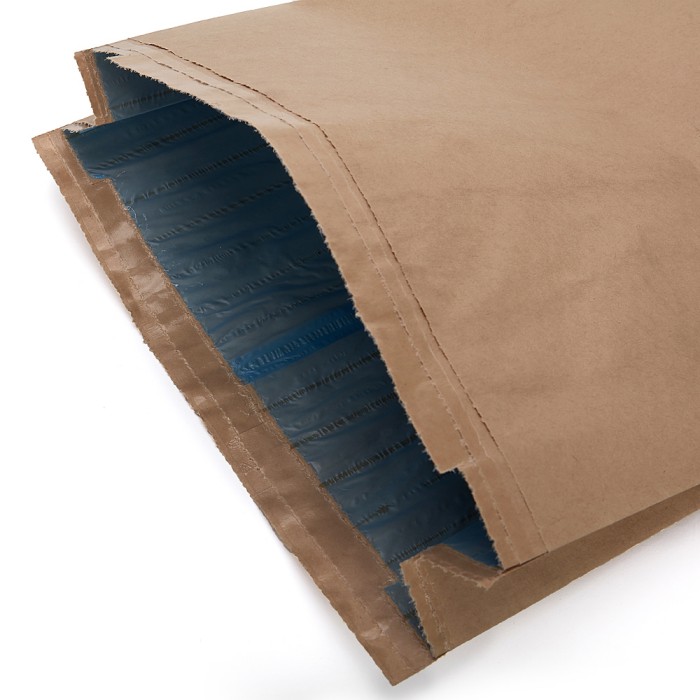
Multiwall Paper Bags are a widely used packaging solution across various industries, offering both strength and versatility in their design. These bags are typically composed of multiple layers of paper, providing an ideal balance between durability and environmental friendliness. This article will explore the different types of Multiwall Paper Bags, the structure of the layers involved, and how the lamination process plays a crucial role in enhancing the bag’s performance. We will also delve into the advantages of utilizing fine yarn technology, which is used to create bags with finer, more durable threads, resulting in better packaging performance.
Types of Multiwall Paper Bags and Their Lamination Structure
Multiwall Paper Bags have become an essential part of the packaging landscape, especially in industries like food, agriculture, construction, and chemicals. These bags are available in various designs and constructions, and their choice largely depends on the specific requirements of the product being packaged.
Multiwall Paper Sacks are generally constructed with multiple layers, each serving a distinct purpose:
- Outer Layer: This is typically made from kraft paper, which provides strength and durability. Kraft paper is highly resistant to tearing, making it an excellent choice for packaging heavy or bulk items. In some cases, the outer layer may also be printed with branding or product information.
- Middle Layer: Often referred to as the laminated layer, this layer is made from materials such as polypropylene (PP) or polyethylene (PE). The middle layer acts as a moisture barrier, preventing external moisture from compromising the contents inside. This is particularly important when packaging food products, grains, or construction materials that need to remain dry during storage and transport.
- Inner Layer: The innermost layer is usually a layer of paper that is either uncoated or lightly treated. The inner layer can be designed to offer added protection against spillage, while also facilitating easy filling and sealing.
The primary function of lamination in Multiwall Paper Bags is to enhance the barrier properties, adding strength, moisture resistance, and durability to the bags. Lamination is often achieved by using Kraft Paper PP Bags, which combine the environmental benefits of kraft paper with the enhanced durability of PP fibers.
Key Types of Lamination:
- Polyethylene Lamination: This is one of the most common lamination methods, providing a smooth and glossy finish to the bags. Polyethylene helps increase the strength of the bags, preventing punctures and tears.
- Polypropylene Lamination: Similar to polyethylene, Kraft Paper PP Bags offer a more durable and heat-resistant option. These bags are particularly popular in industries such as agriculture, chemicals, and heavy-duty packaging.
- Aluminum Foil Lamination: Used primarily for highly sensitive products that require protection from oxygen, light, and moisture, aluminum foil lamination provides an additional layer of protection, often for products in the food and pharmaceutical industries.
Fine Yarn Technology and Its Benefits
In recent years, fine yarn technology has revolutionized the production of woven bags, including those used for packaging in industries like agriculture, food, and construction. This technology enables manufacturers to weave extremely fine threads, resulting in Kraft Paper Woven Bags that are stronger and more efficient in holding heavy loads. The process of fine yarn weaving involves the following steps:
- Selection of Fine Yarns: High-quality, fine polypropylene threads are selected for their superior strength and flexibility. These threads are then woven tightly together to form the fabric.
- Weaving Process: The fine yarns are woven in a tight pattern to increase the density of the fabric. This tightness ensures that the woven bags have higher tensile strength and greater load-bearing capacity.
- Lamination and Coating: After weaving the fabric, a lamination layer may be applied to improve moisture resistance. This step is essential in protecting the contents of the bag from environmental factors such as humidity and water exposure.
The main advantage of using fine yarn technology in the production of woven bags is that the bags become lighter while maintaining superior strength. These Kraft Paper Woven Bags are less bulky and can hold heavier loads than traditional woven bags made from thicker threads. As a result, these bags can be used to pack heavier goods without compromising their durability.
Advantages of Fine Yarn Technology
1. Enhanced Strength and Durability: Fine yarn technology allows for the production of woven bags with a high tensile strength. These bags can withstand significant weights and resist tearing, making them ideal for heavy-duty applications.
2. Higher Density: The use of finer yarns results in a denser fabric that provides better protection against environmental conditions. This is especially beneficial in packaging sensitive products such as grains, chemicals, and pharmaceuticals.
3. Lightweight Packaging: Despite their strength, Kraft Paper PP Bags made with fine yarn technology are lighter in weight compared to traditional woven bags. This can lead to reduced shipping costs and easier handling, making them an ideal choice for logistics.
4. Superior Aesthetic Appeal: Fine yarn technology also improves the appearance of woven bags. The smoother finish provided by the fine yarns gives the bags a more polished and professional look, which is essential for brand image and product presentation.
Comparison of Multiwall Paper Bags with Fine Yarn Technology
The following table highlights key parameters for comparing traditional Multiwall Paper Bags with those made using fine yarn technology.
Parameter | Traditional Multiwall Paper Bags | Fine Yarn Technology Multiwall Bags |
---|---|---|
Strength | Moderate strength, sufficient for most products | High tensile strength, suitable for heavy-duty use |
Weight | Heavier due to thicker threads | Lighter, reducing overall shipping weight |
Moisture Resistance | Good (due to lamination) | Excellent, enhanced by tight weave and lamination |
Load Capacity | Suitable for medium-weight products | Suitable for heavy products with high load-bearing capacity |
Aesthetic Appeal | Standard appearance, functional | High-quality finish, more visually appealing |
Environmental Impact | Recyclable but heavier material | More sustainable due to lighter weight, leading to lower carbon footprint |
Conclusion
In conclusion, Multiwall Paper Bags and Kraft Paper PP Bags offer an excellent combination of strength, versatility, and environmental friendliness. By employing different lamination methods, manufacturers can create bags suited to various needs, from moisture resistance to heavy-duty use. The introduction of fine yarn technology in woven bag production further enhances their strength, load-bearing capacity, and aesthetic appeal. This innovation not only improves the functionality of packaging materials but also contributes to more sustainable and cost-effective solutions for businesses.
For more in-depth information on Multiwall Paper Bags, visit this article on the Role of Multiwall Paper Bags in Waste Management and Recycling, and for details on Multiwall Paper Bags Manufacturers, check out this article on Laminated Woven Bags: Advanced Manufacturing and VidePak’s Expertise.